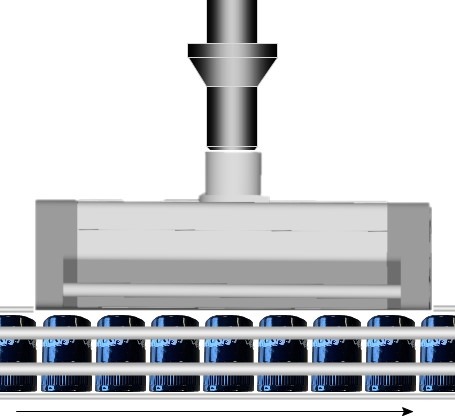
Closure Cleaning
PROBLEM
During the production of bottle closures contamination produced during the production of the closure can become entrapped inside the closure. This results on the contamination entering the liquid after the bottle filling and capping process.
Removal of contamination from the finished closure can be affected by static charges making removal difficult at production speeds.
Existing systems are reliant on compressed air making them expensive to run and require FDA approved filtration systems.
SOLUTION
A Meech closure cleaning system has been proven to be effective at removal of paint flex’s, aluminium and plastic swarf at production speeds.
Ionised air is blown into the closure as it travels the length of the cleaning manifold neutralising static charges and dislodging contamination. Vacuum extracts the contamination and captures it in the fan driven air handling unit requiring no compressed air within the cleaning process.
Download