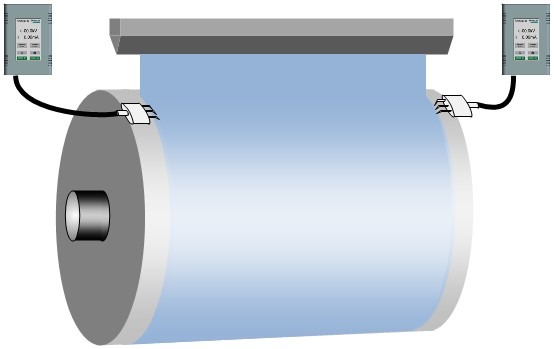
Cold roller pinning
PROBLEM
Cast plastic film exits from the die in a semi molten (and hot) state directly on to a chill roller. As the plastic cools on the roller, it shrinks in width – known as ‘Necking’.
This is undesirable as it makes the finished film uneven and impairs quality. Previously, compressed air jets have been used to hold the edges of the plastic at the desired width.
This is costly, noisy and can leave excessive marking on the film.
SOLUTION
The use of electrostatic pinning reduces the compressed air usage, minimises film edge damage making greater use of the extruded film.
The Meech 995-CLAW is specifically designed for this application. Each side of the extruded film is pinned to the cold roller, locking into place stopping width shrinkage producing uniform thickness across the web width.
The 25mm diameter mounting rod allows the three flexible titanium pins can be positioned in an array to suit the application. Each pin is individually resistively coupled to provide powerful independent pinning, without the risk of sparks damaging the expensive roller.
Download- Related Products