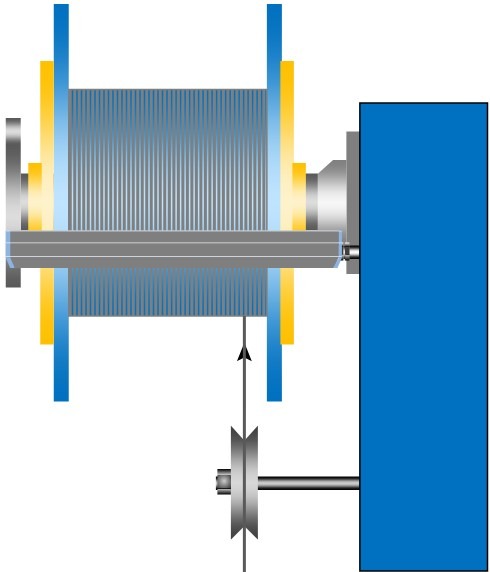
Electrical wire rewind
PROBLEM
To create the bubbles in Polystyrene Butane is injected into the liquid plastic during extrusion. As the extruded Polystyrene cools the Butene escapes and static charges are generated on the material, producing a risk of fire.
Though out the slitting, transfer and rewinding processes, the static charges need to be controlled.
SOLUTION
There are four critical areas which require static control. Incorporating SmartControl and sensors allows for greater control to ensure equipment is maintained appropriately, static levels in key areas are measured and data logged and offers closed loop static control auto adjusting ioniser performance to optimum levels.
Extrusion head
This may be classified as an ATEX area requiring an EX approved static control system. If not ATEX, a medium range Hyperion bar is required.
Slitting
Butane will collect inside the Polystyrene sock, the knives used for slitting offer a potential for static charges to spark too. The use of an ionising blower neutralises the static charges and helps disperse the Butane
Web drive rollers
As the web continues to cool, static charges continue to rebuild, and the material continues to degas. The drive rollers offer an earth potential for the static charges to spark too. Removing the charges prior to web contact, controls the risk of fire.
Rewinds
The last area requiring static control, is on the rewinds. Friction of material on material during rewind will generate static charges. Controlling these charges, prevents the risk of ignition during storage to allow the material to completely degas.
Note: storing rolls on wooden pallets during degassing allows the Butene which is heavier than air to escape. Storing rewound rolls on a concrete floor, traps the gases and offers any static charges to spark to the concrete.
Download- Related Products