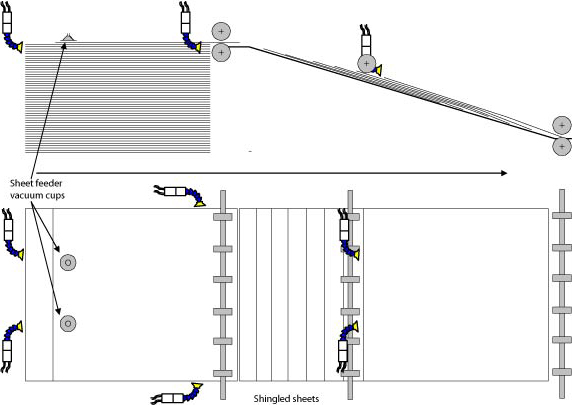
Blocking Of Sheets While Sheet Feeding Due To Static
Problem
Problems that are typically faced with offset printing are as follows :
The constant generation of friction during the feeding of paper or plastic sheets at the unstacker, creates static electricity. This increases as the unstacking process take place…
- This will cause the sheets to stick together as static electricity acts as a form of magnet
- Some unstacker are fitted with compressed or pumped air nozzles that blow air hoping to separate the sheets during the unstacking process
- The air actually creates more static electricity as the air creates friction on the sheets
- Two or more sheets of paper will then be picked up and conveyed into the printing press, a sensor will detect this and stop the machine
- Static charges can also cause sheets to stick to the machine bed, preventing registration of the sheets
- The sheets will then need to be cleared from the conveyor and some test run will need to be carried out when resuming the machine
- If the sheets are not detected by the sensor and passes through onto the printing area, this may damage the blanket
Related problems in the process that arise :
- Fanning of paper or pile turning is carried out hoping to loosen the paper before placing onto the unstacker meaning that time is taken to load the sheets of paper
- Stopping of machine to clear the multiple sheets of paper and testing to resume consumes time and waste material
- Blanket is at risk of getting damaged, which is expensive to replace
Solution
With our solution of installing the 261 Flexi Nozzles (positions as depicted in the attached), the following can be expected as a result:
- Fanning of paper or pile turning is no longer necessary as the Ionizing Nozzles will blow ionized air between the sheets to ensure that only a single sheet of paper is picked up and transferred onto the conveyor from the unstacker:
a. The 2 Ionizing Nozzles installed near the suction cups will blow ionized air between the sheets as it is being picked up
b. Any sticking sheets will drop and ensuring only 1 sheet of paper remains to be transferred
c. The 2 Ionizing Nozzles installed by the 2 sides will ensure a wider area of coverage by the ionized air as well as any static electricity that is created by the friction of moving sheets of paper onto the conveyor is neutralized - The machine will not stop due to multiple sheets being fed ensuring a continuous run
- Risk of damaging blanket due to multiple sheets of paper being fed will be eliminated
The benefits of installing our solution are :
- No time required to fan the sheets of paper
- No time and material wasted to clear the multiple sheets and testing when resuming the machine
- Blanket will not be damaged due to multiple sheets of paper being fed
- Machine can be set to run faster
- Production yield increases
- Output in a production shift increases meaning a reduction in working hours (and overtime)
- Saved time can be used for other tasks