Schmutzentfernung in Batterie Produktion

Der Aufstieg des Elektrofahrzeugmarktes in den letzten Jahren hat die Hersteller dazu veranlasst, schnell Lithium-Ionen-Batterien zu entwickeln und herzustellen, um den Verkaufsboom anzukurbeln. Da auf der ganzen Welt Giga-Fabriken eröffnet werden, um die Nachfrage zu befriedigen, wächst der Wettbewerb und Qualität steht an erster Stelle.
Da sich die Technologien rasant weiterentwickeln, sind Batteriehersteller bestrebt, eine Batterie zu entwickeln, die mit Benzin- oder Dieselfahrzeugen mithalten kann, um eine beeindruckende Reichweite und Leistung zu bieten.
Um dies zu erreichen, muss jede Phase des Batterieherstellungsprozesses sorgfältig analysiert werden, um die besten Ergebnisse zu erzielen.
Betrieb im Umfeld der Herstellung von Lithiumbatterien:
Einer der entscheidenden Schwerpunkte bei der Produktion von Elektrofahrzeugbatterien sind die Bedingungen der Fertigungsumgebung. Von den ersten Rohstoffen bis zur Zellmontage müssen die Herstellungsbedingungen streng kontrolliert werden. Dies stellt sowohl Gerätehersteller als auch Betreiber vor Herausforderungen. Es gibt drei Hauptbereiche, die kritisch zu berücksichtigen sind:
Lithiummetall reagiert äußerst empfindlich auf kleinste Mengen Feuchtigkeit in der Luft und Temperaturschwankungen bei der Produktion.
Die geringste Belastung führt zu einer verminderten Leistung und wirkt sich auf eine verkürzte Produktlebensdauer von Lithium-Ionen-Batterien aus.
Die Raumtemperatur sollte auf dem empfohlenen Niveau von etwa 25 °C (77 °F) gehalten werden, mit einer Toleranz von +/(-) 2 °C (36 °F) und niedrigen Taupunkten im Bereich von <1 %.
Die Luftwechselrate im Produktionsraum sollte 20 bis 50 Luftwechsel pro Stunde betragen und gleichzeitig eine minimale Frischluftzufuhr für einen positiven Raumdruck und eine notwendige Belüftung für die Bediener aufrechterhalten.
Verunreinigungen jeglicher Art in den Batteriematerialien oder in der Zelle können zu direkten oder sanften Stromausfällen führen – was zu Ausschuss am Ende der Produktionslinie oder zu einer geringen Batteriereichweite führen kann.
Der Reinraumzustand ISO 8 (oder höher) ist wahrscheinlich, wobei der Schwerpunkt auf der Entfernung von Verunreinigungen in der Umgebung sowie auf dem Personal liegt.
Natürlich können Verunreinigungen nicht immer entfernt werden, daher besteht immer noch das Risiko einer Kontamination und einer Beeinträchtigung der Produktionsausbeute.
Probleme und freie Partikel können auch bei den Prozessen Ab-/Aufwickeln, Umrüsten, Beschichten, Kalandrieren, Schlitzen, Stanzen, Laserschneiden und mehr entstehen.
All dies hat das Potenzial, in die Anoden-/Kathoden-/Separatorfilmschichten einzudringen.
Bei einigen Verunreinigungen handelt es sich um trockene, freie, ungebundene Partikel, während es sich bei anderen um feuchte oder gebundene Verunreinigungen handelt, die schwieriger zu entfernen sind.
Ein weiterer Risikobereich ist die toxische Kontamination durch die Beschichtungsmaterialien, wenn diese über Rollen übertragen, geschnitten, gewickelt und gerollt werden – diese können in die Luft gelangen und zu einer Atemgefahr für den Bediener werden.
Statische Aufladungen in der Fertigungsumgebung können zu einer Reihe von Problemen führen:
Batteriekomponenten von Elektrofahrzeugen reagieren sehr empfindlich auf statische Aufladungen – die Komponenten müssen dabei entladen werden.
Unkontrollierte statische Aufladungen wirken sich auch auf den Materialfluss aus und führen zu Fehlverhalten oder Ausfällen des Materials.
Bei unkontrollierten statischen Entladungen (Funken) kommt es zu dendritischen Verbrennungen an der Oberfläche, die die dielektrischen Eigenschaften des Separatorfilms beeinträchtigen – was zu inkonsistentem Lade- und Entladeverhalten und zu Produktausfällen führt.
Statische Ladungen, die auf isolierenden Materialien wie der Separatorfolie erzeugt werden, ziehen ebenfalls Partikel an, was das Kontaminationsrisiko erhöht.
Wir verstehen diese entscheidenden Anforderungen und haben unsere Geräte in Trockenräumen und Trockentestkammern getestet. Unsere PDie Produktkonstruktionen wurden angepasst, um potenziell vorzeitig verschleißende Teile wie Riemen und Riemenscheiben zu eliminieren und durch Direktantriebsmotoren zu ersetzen. Aufbauend auf unserem Fachwissen und unseren Kernkompetenzen bietet Meech eine maßgeschneiderte Palette an Lösungen zur Entfernung statischer Aufladungen und Verunreinigungen, um in jeder Anwendungsphase einen Null-Fehler-Ansatz zu liefern.
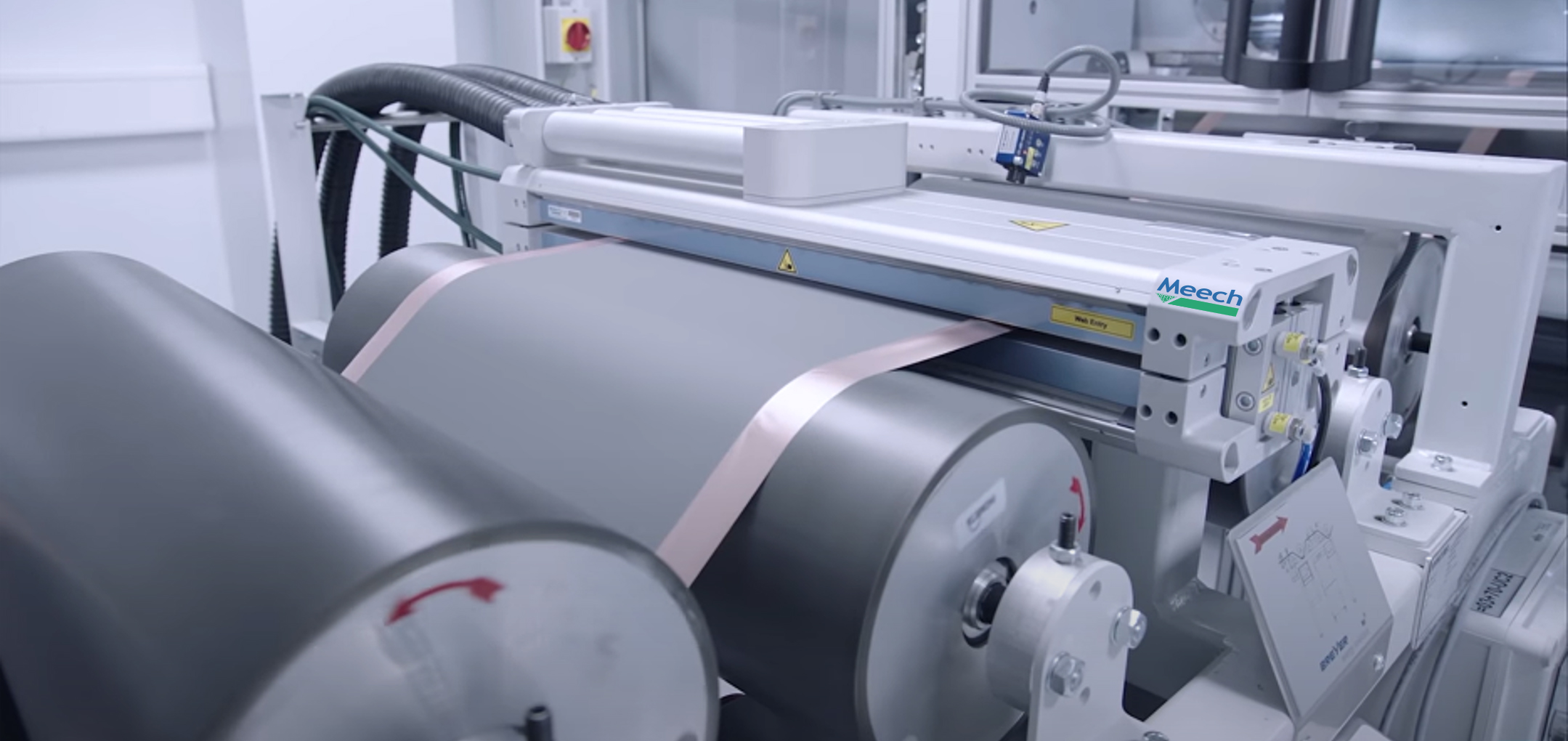
Unser Zero-Faults-Forward-Ansatz
Wir haben eine Reihe von Phasen während des Batterieherstellungsprozesses identifiziert, die anfällig für Kontaminationen in der Produktionslinie sind. Indem Sie an diesen Stellen die richtigen Lösungen anwenden, stellen Sie sicher, dass Ihre Produktionskette keine Schwachstellen aufweist. Wir untersuchen diese im Folgenden und demonstrieren unsere Lösungen…
Vor der Beschichtungsphase der Kupfer-/Aluminiumbahn empfehlen wir die Verwendung eines Bahnreinigers auf dem Substrat, um jegliche Oberflächenverunreinigungen zu entfernen, die sich auf die Dicke und Qualität der beschichteten Bahn auswirken könnten. Durch die Entfernung der Verunreinigungen in diesem Stadium wird sichergestellt, dass keine unerwünschten Partikel in den Schichten eingeschlossen werden, die die Batterieleistung auf der ganzen Linie beeinträchtigen würden.
Um zu vermeiden, dass sich Verunreinigungen von der Walze selbst auf der Substratbeschichtung abzeichnen, empfehlen wir die Verwendung unseres CyClean-R, das sich ideal für die Verwendung auf einer Walze eignet, oder unseres Kontakt-RoClean. Dadurch wird die Walze effektiv von jeglichen Verunreinigungen befreit, um sicherzustellen, dass es nicht zu einer Übertragung auf die Bahn kommt.
In dieser Phase werden die Bahn- und Beschichtungsschichten auf die richtige Dicke zusammengepresst, wodurch die Beschichtung auf der Bahn selbst aktiviert wird. Durch Reinigen der Bahn vor dieser kritischen Phase wird verhindert, dass Verunreinigungen zwischen den Schichten selbst eingeschlossen werden.
Beim Schlitzvorgang können viele Ablagerungen entstehen, die das beschichtete Bahnsubstrat verunreinigen können. Der Einsatz eines Bahnreinigers stellt in dieser Phase sicher, dass die Partikel von der Oberfläche der Bahn entfernt und aus der Betriebsatmosphäre gefiltert werden, um eine erneute Kontamination zu vermeiden. Angesichts des hohen Kontaminationsrisikos in dieser Phase ist eine Reinigung unbedingt erforderlich, um das Risiko zukünftiger Stromausfälle und teuren Ausschusses zu vermeiden.
Ähnlich wie beim Nachschneiden können beim Elektrodenschneiden Partikel und Ablagerungen die Bahn verunreinigen. Um dies zu vermeiden, reinigt die Bahnreinigung in dieser Phase die Oberfläche des Substrats, was zu sauberen und klaren Trennschichten führt.
Für den Wickelprozess schlagen wir eine Reihe von Lösungen vor, um die besten Ergebnisse zu erzielen. Vor dem Aufwickeln wird eine Oberflächenreinigung des Substrats empfohlen, um keine Verunreinigungen in der Batteriefolie einzufangen. Um statische Probleme zu überwinden, die sowohl gefährlich als auch äußerst schädlich für die Batterieleistung sein können, sollte auch eine wirksame statische Kontrolle eingeführt werden. Dadurch werden eventuelle statische Aufladungen, die durch den Wickelvorgang entstehen, neutralisiert.
* Alle Zeichnungen zeigen ein CyClean-R-Profil. Dies dient nur zur Veranschaulichung. Welcher Bahnreiniger und welche Position für Ihren Prozess am besten geeignet sind, hängt von bestimmten Faktoren Ihrer Anwendung ab.
Bahnreinigungslösungen
Mit einer Reihe speziell entwickelter Kontakt- und kontaktloser Bahnreiniger kann Meech Lösungen für die Anoden-/Kathoden-/Separatorfilmreinigung für unterschiedliche Bahnbreiten, Spannungen, Standorte und Materialien liefern.
Für anspruchsvollere „gebundene“ Verschmutzungen bieten wir eine neue Batteriereinigungsreihe mit Bürstenoberflächenreinigern an – mit Materialien, die speziell für Trockenraumanwendungen geeignet sind.
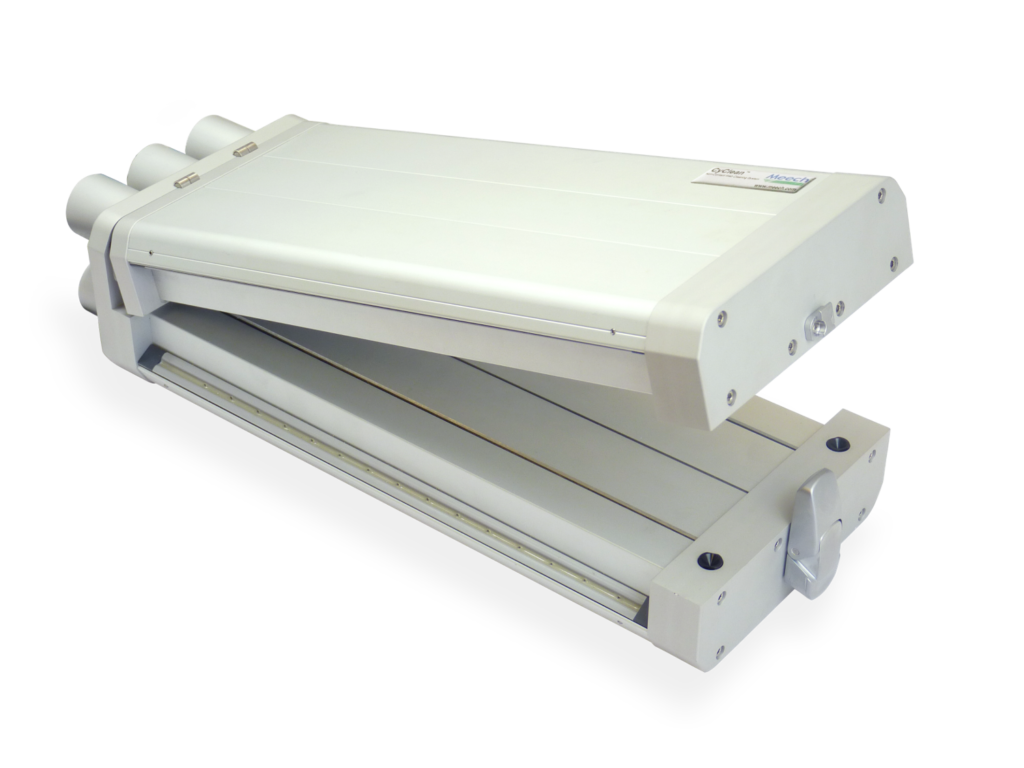
CyClean™ berührungsloser Bahnreiniger
Meech CyClean™ wurde als Reaktion auf die Nachfrage nach einem kompakten, leistungsstarken, berührungslosen Bahnreiniger entwickelt.
Durch die Anwendung fortschrittlicher numerischer Strömungsmechanik entfernt und extrahiert CyClean Verunreinigungen unter 1 Mikrometer.

CyClean-R™ berührungsloser Bahnreiniger
Der CyClean-R bietet eine spezielle Lösung für die Bahnreinigung bei geringer Spannung.
Der CyClean-R ist so konzipiert, dass er auf der Walze positioniert wird, wo die Bahnspannung am höchsten ist, wodurch die Probleme einer niedrigen Spannung umgangen werden und dennoch eine hervorragende Oberflächenreinigung erzielt wird.
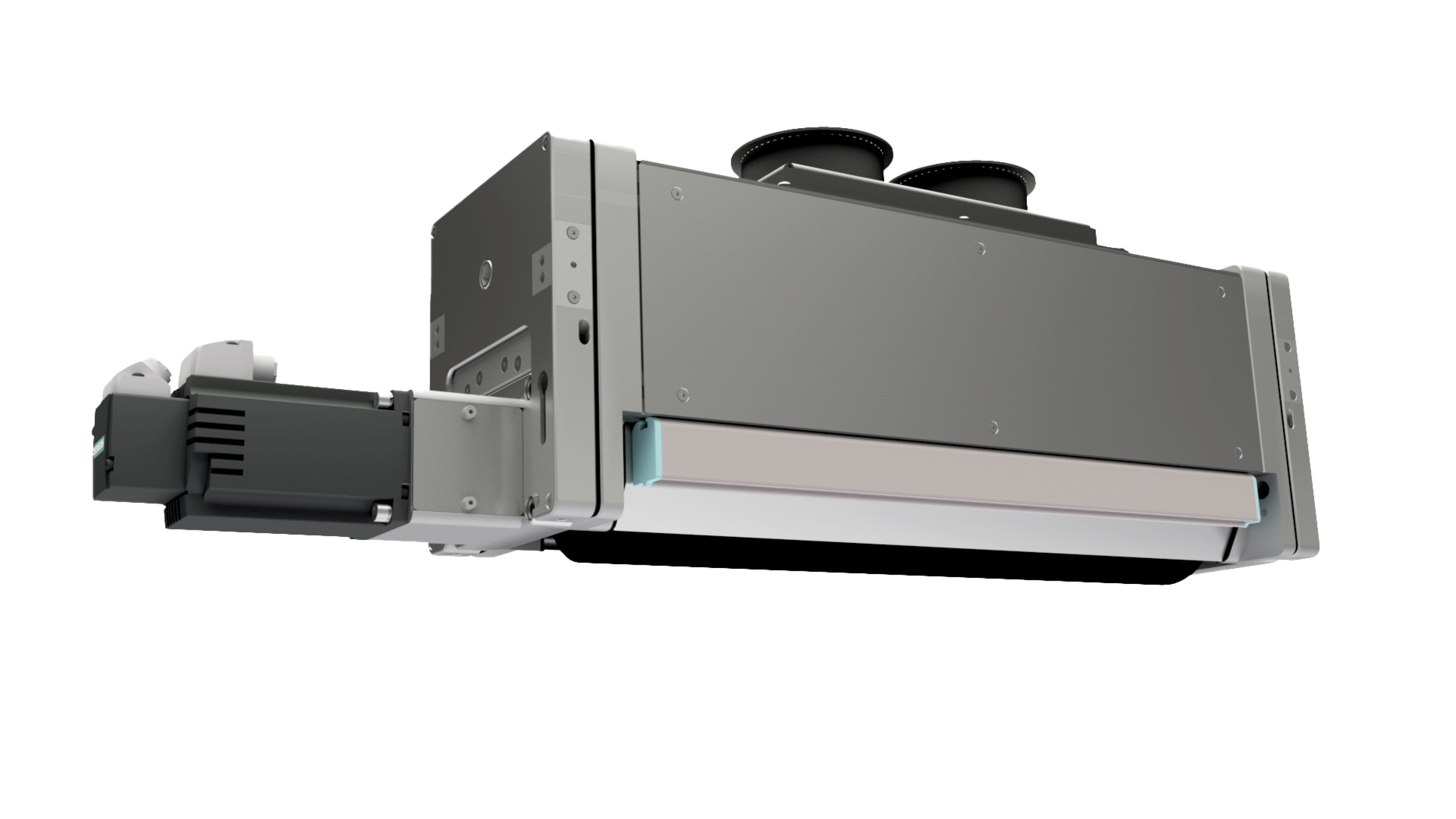
RoClean™ Kontaktbahnreiniger
RoClean ist der neueste Kontaktbahnreiniger, der hervorragende Oberflächenreinigungsergebnisse für die Batteriefolienherstellungsindustrie liefert.
RoClean reinigt die Bahnoberfläche effektiv durch den Einsatz sowohl statischer Kontrolle als auch einer effizienten Borstenwalzenbürste.
Lüftungsgeräte
Meech-Bahnreiniger werden mit Meech-Luftbehandlungseinheiten (AHUs) geliefert, um sicherzustellen, dass das Luftgleichgewicht aufrechterhalten wird, um die Genauigkeit von Luftdruck und Vakuum perfekt zu steuern. Hierbei handelt es sich um kompakte, industrietaugliche Geräte, deren Leistung auch über eine SPS-Steuerung überwacht werden kann.
Für die Batterieumgebung wurde eine neue AHU-Option entwickelt, um das Einfangen giftiger Schadstoffabfälle und die sichere Filterentfernung durch den Bediener zu verbessern
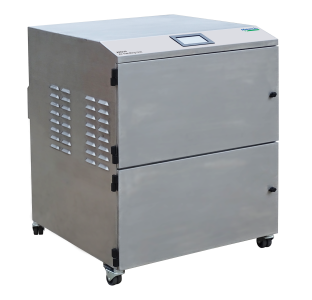
Lösungen zur statischen Kontrolle
Hochleistungs-Gleichstrom-Ionisationsstäbe sind spezifiziert, bei denen Frequenz, Spannung und Polarität genau auf Material, Entfernung und Restladung abgestimmt werden können. Dazu gehören EX-Versionen für brennbare Umgebungen.
Um den Betrieb zu gewährleisten und die Leistung zu protokollieren, sind diese häufig mit einer SMART-Steuerung der Industrie 4.0 ausgestattet – um die Leistung sofort zu programmieren und die Leistung in Echtzeit aufzuzeichnen und zu überwachen.

Hyperion™ 924IPS Ionisationsstab
Der Hyperion 24IPS wird mit 924 V Gleichstrom betrieben und ist der kompakteste gepulste Gleichstrombalken, der auf dem Markt erhältlich ist.
Der 924IPS ist mit der ICM-Technologie (Ion Current Monitoring) von Meech ausgestattet. Diese gewährleistet die Aufrechterhaltung der Leistung mit lokalen und Fernwarnungen, wenn die Bar gereinigt werden muss.

Hyperion SmartControl Touch
SmartControl Touch ist die neueste Innovation von Meech, die den Anforderungen moderner automatisierter Industrien und dem Wachstum von Industrie 4.0 gerecht wird, um maximale Produktivität und Ausgabequalität zu erreichen.
Mit SmartControl Touch kann der Benutzer die Leistung mehrerer angeschlossener Hyperion-Ionisationsstäbe und -Sensoren über den integrierten Touchscreen oder aus der Ferne überwachen, steuern und anpassen.
Könnten wir Ihnen helfen, Ihren Batterieherstellungsprozess zu verbessern?
Laden Sie unseren Branchenführer herunter oder kontaktieren Sie unsere Branchenexperten ...
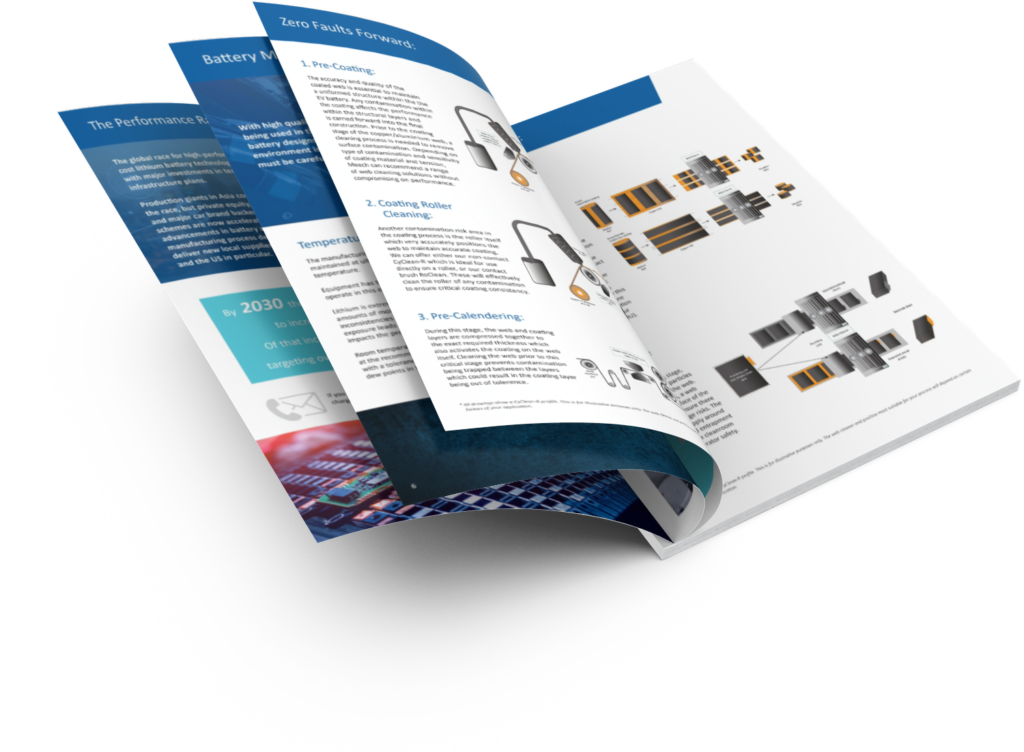