IonWash for Automotive
Delivering Clarity To The Automotive Industry
Contamination can be costly for component manufacturers:
The Problem with Handheld Cleaning
Traditionally, manufacturers have employed a handheld ioniser cleaning method to clean automotive light clusters. However, this presents its own issues, especially when under such stringent measures:
Inconsistent
The time spent cleaning a unit could vary from piece to piece.
Not Thorough
The surfaces of complex 3D components could be missed or not cleaned effectively due to human error.
Labourious
Using handheld ioinisers takes longer than due to human speed and capability.
That's Why We Designed IonWash
Case Study: Engineering IonWash
The Solution
IonWash: At A Glance
The Meech IonWash™ is a revolutionary nozzle cleaning system, designed to remove dry un-bonded contamination from components.
The IonWash incorporates specially designed Meech adjustable ionising nozzles which direct the ionisation and air flow towards the components to blow the contamination from the surface of a three-dimensional object in a time and labour efficient manner.
Developed specifically with three-dimensional ionisation in mind, the IonWash is the latest innovation in large product and component contamination removal.
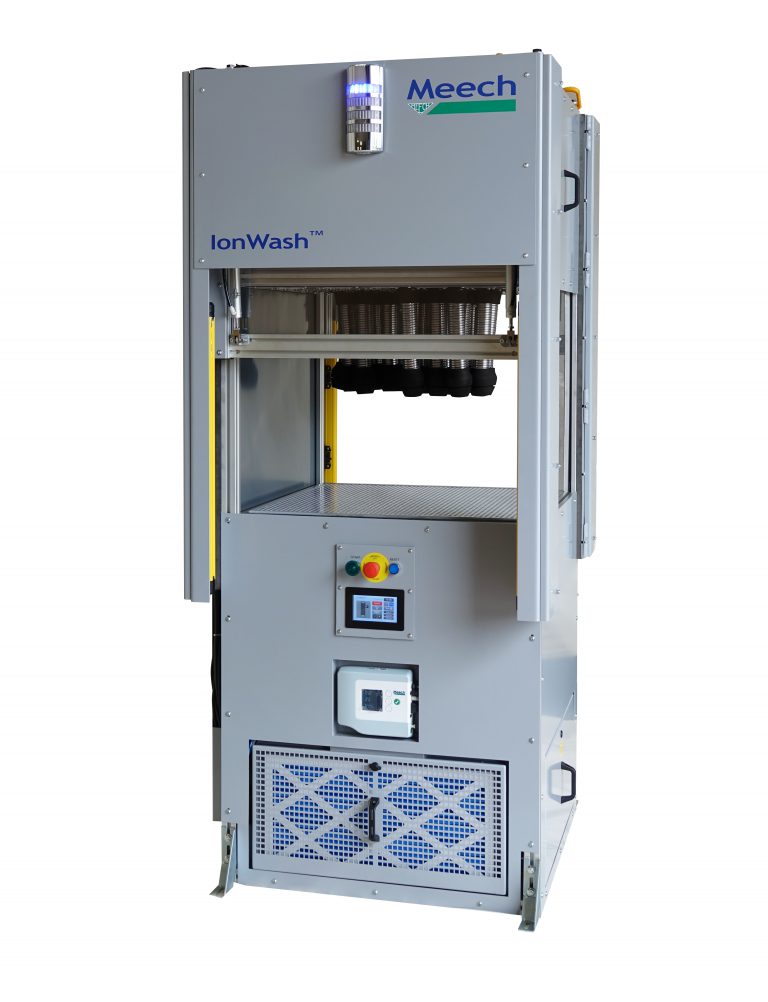
The 3 Steps of IonWash
Powerful ionisation neutralises static charges on the components, loosening the contaminats.
High volume (blown) air flows through the multi-directional nozzles, towards the component, removing the contamination from the surface.
High volume negative (vacuum) air then pulls the contamination into the vacuum chamber/filter media.
The Benefits of IonWash
Consistent Cleaning
IonWash can be set to run at programmed times to achieve the optimum cleaning. This means each headlight cluster unit is exposed to the same level and time of cleaning.
Thorough Coverage
The manouverable nozzles of the IonWash can be aimed to provide full surface ionisation and air pressure of 3D components, ensuring a thorough cleaning performance with every unit.
Efficient
Simply place the headlight cluster unit into the mount in the IonWash and press the start button to commence the cleaning cycle.

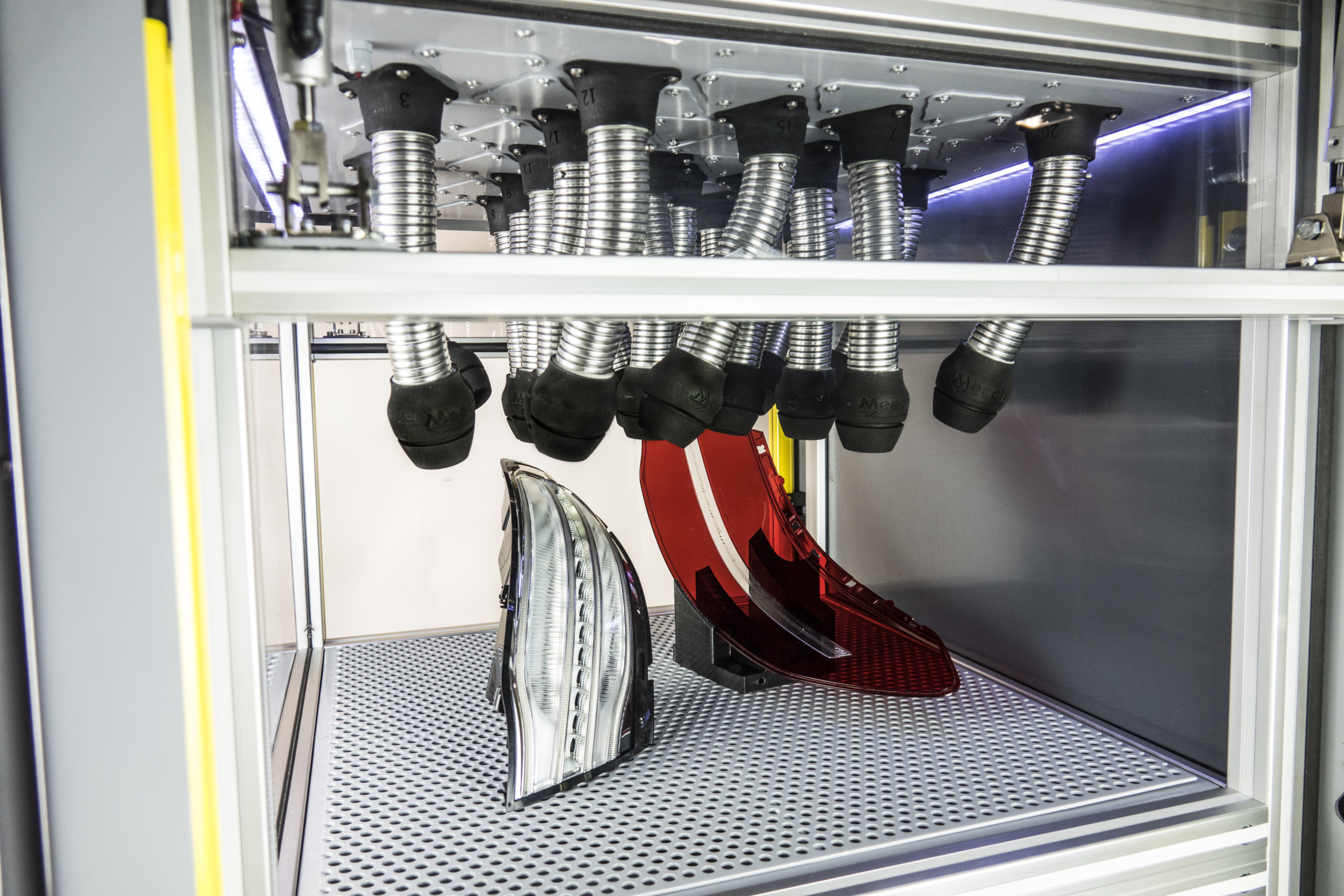
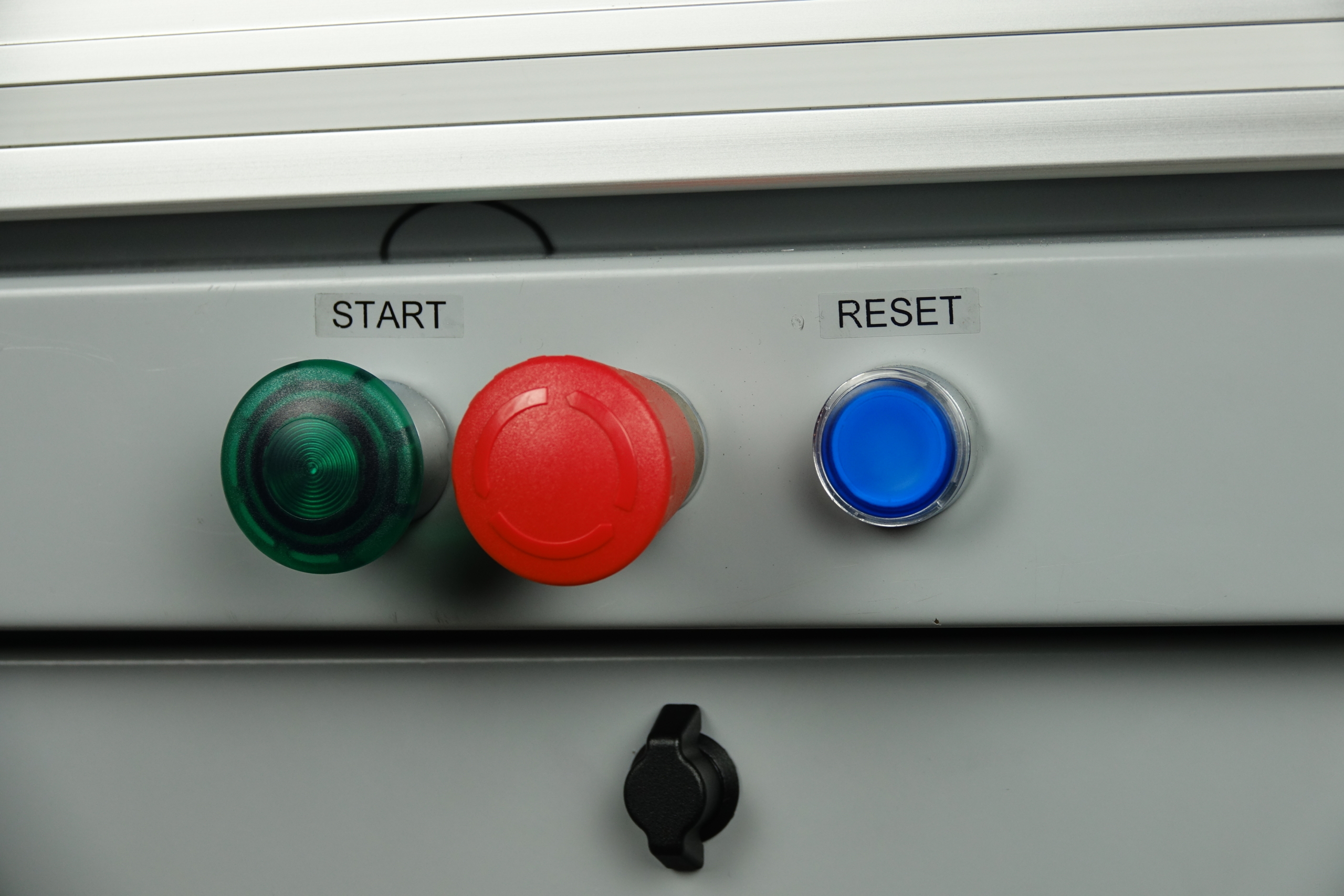
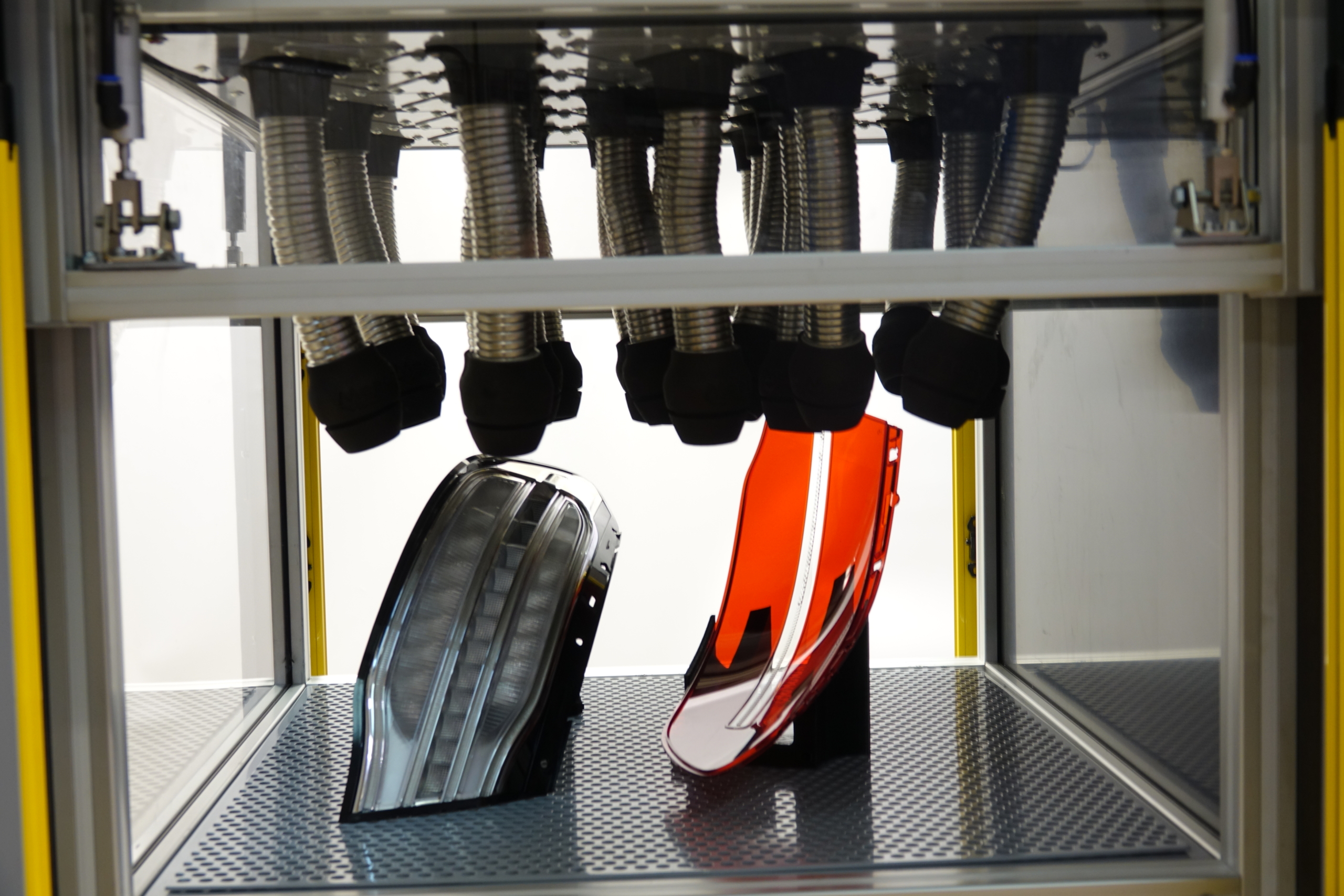
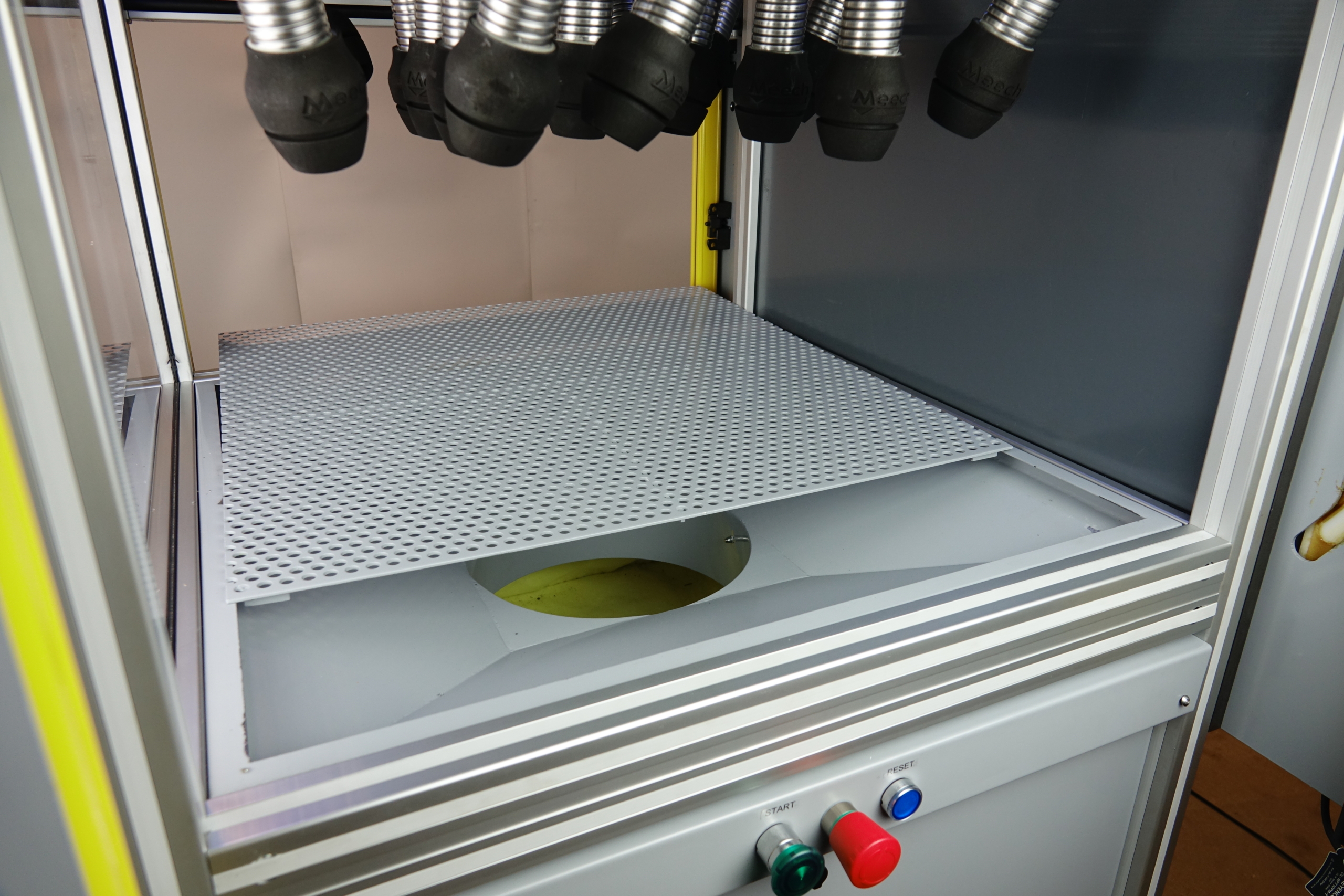
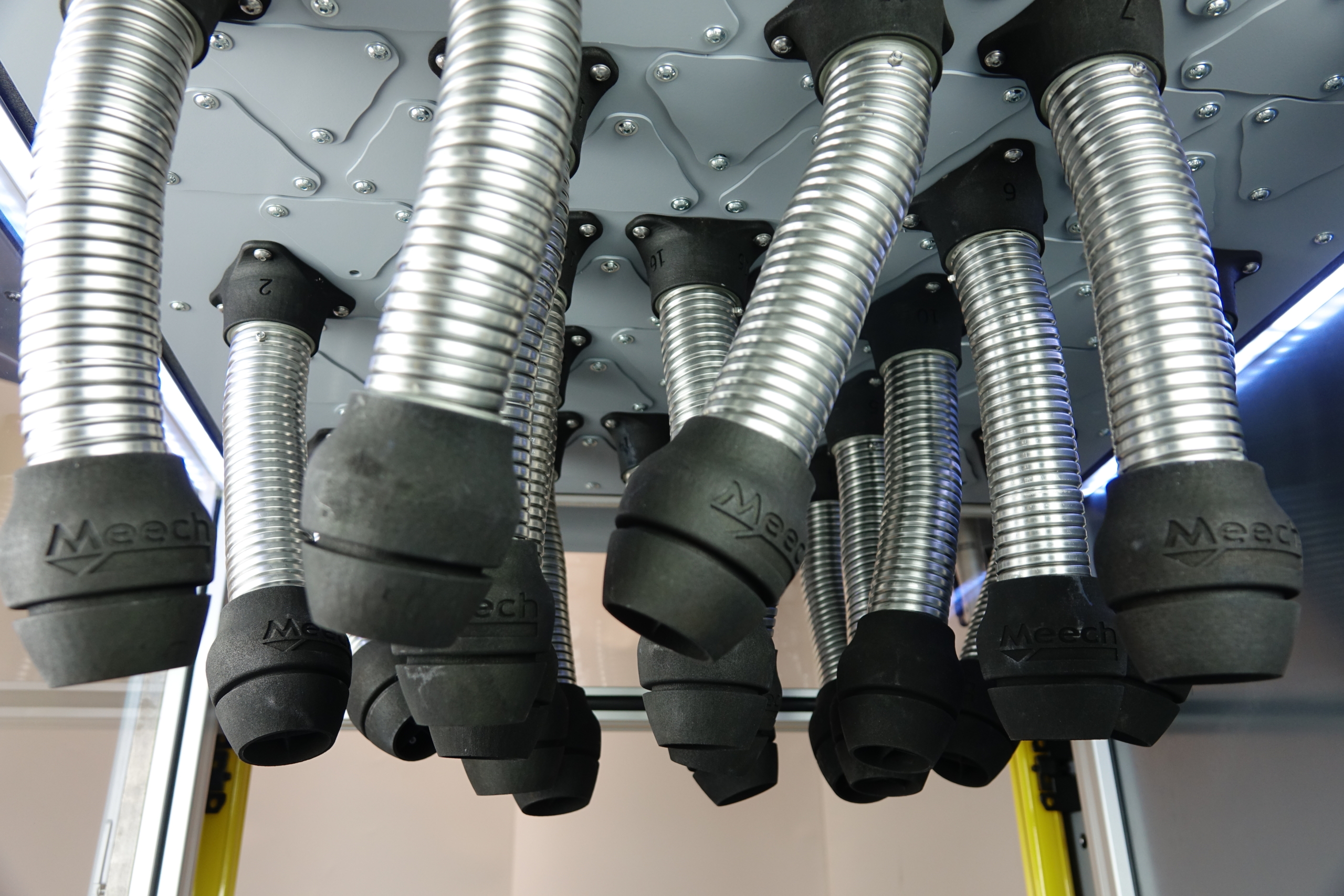