배터리
Contamination removal in battery cell production
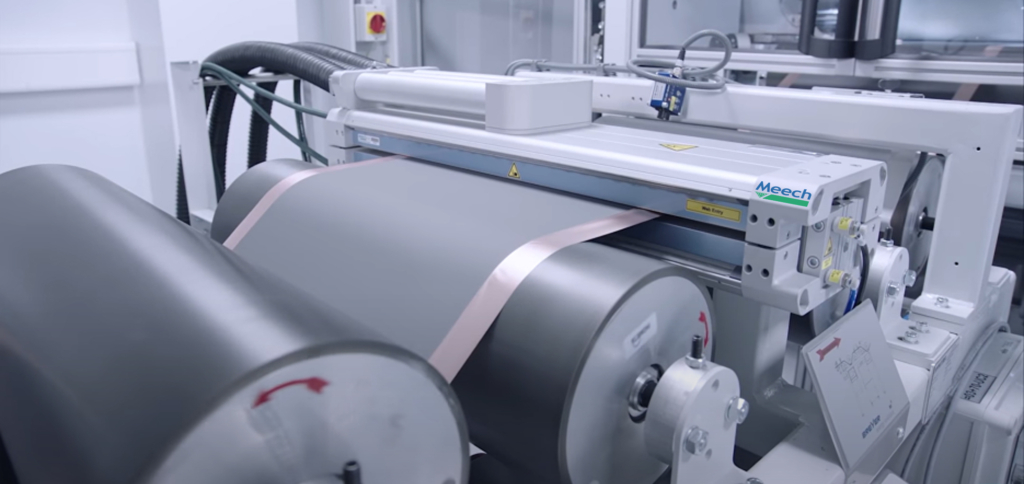
The rise of the EV market in recent years has led manufacturers to rapidly develop and manufacture lithium-ion batteries to fuel the boom in sales. With giga-factories opening across the globe to meet the demand, competition is growing and quality is paramount.
With technologies developing at speed, battery manufacturers are looking to create a battery which rivals petrol or diesel-fed vehicles, in order to deliver impressive mileage range and performance.
In order to achieve this, every stage of the battery manufacturing process must be meticulously analysed in order to produce the best results.
Operating in the lithium battery manufacturing environment:
One of the critical focus areas for EV battery production is the manufacturing environment conditions. From initial raw materials to cell assembly the manufacturing conditions must be tightly controlled. This creates challenges for equipment manufacturers and operators alike. There are 3 main areas of critical consideration:
Lithium metal is extremely sensitive to even the smallest amounts of moisture in air and temperature inconsistencies in production.
The slightest exposure leads to reduced performance and impacts on reduced product life of Lithium-ion batteries.
Room temperature should be maintained at recommended levels, around 25°C (77°F), with tolerance of +/(-) 2°C (36°F) along with low dew points in the range of <1%.
The air change rate in the production room should be 20 to 50 air changes per hour while maintaining minimum fresh air introduction for positive room pressure and essential ventilation for operators.
Contamination of any type into the battery materials or wound into the cell can lead to direct or soft electrical shortages – leading to end of line rejects or low battery range performance.
ISO 8 cleanroom condition (or higher) is likely with major focus on contamination removal in the environment as well as on personnel.
Of course, contamination cannot always be removed and so there is still a risk of contamination and an impact on production yields.
Problems and free particles can also be created within the processes of unwinding/winding, changeovers, coating, calendaring, slitting, stamping, laser cutting and more.
All of these have potential to find their way into the anode/cathode/separator film layers.
Some contamination will be dry, free, unbound particles, while others will be moist, or bound contamination which is more difficult to remove.
Another risk area is toxic contamination from the coating materials as they are transferred over rollers, cut, wound and rolled – this can dissipate into the air and become a breathing hazard for the operator.
Static charges within the manufacturing environment can lead to a number of problems:
EV battery components are very sensitive to static charges – components must be uncharged within the process.
Uncontrolled static charges will also affect the material flow and will cause material misbehaviour or failure.
If uncontrolled, static discharges (sparks) will create surface dendritic burns affecting the dielectric properties of the separator film – leading to inconsistent charge and discharge behaviours and product failure.
Static charges generated on insulative materials such as the separator film also attract particles adding to contamination risk problems.
당사의 제로 결함 전진 접근 방식
We have identified a number of stages during the battery manufacturing process that are prone to contamination on the line. By applying the right solutions at these points, you make sure there are no weak links to your production chain. We explore these below and demonstrate our solutions…
Prior to the coating stage of the copper/aluminium web, we recommend the use of a web cleaner on the substrate to remove any surface contamination that may impact the thickness and quality of the coated web. By removing the contamination at this stage, it ensure no unwanted particles are trapped within the layers, affecting the battery performance down the line.
롤러 자체에서 기판 코팅에 오염이 찍히는 것을 방지하려면 롤러에 사용하기에 이상적인 CyClean-R을 사용하거나 RoClean에 문의하는 것이 좋습니다. 이렇게 하면 롤러의 오염 물질을 효과적으로 청소하여 웹으로 전파되지 않도록 할 수 있습니다.
이 단계에서 웹과 코팅층은 올바른 두께로 함께 압축되어 웹 자체의 코팅을 활성화합니다. 이 중요한 단계 이전에 웹을 청소하면 레이어 사이에 오염 물질이 갇히는 것을 방지할 수 있습니다.
슬리팅 공정에서는 코팅된 웹 기판을 오염시킬 수 있는 많은 잔해가 발생할 수 있습니다. 이 단계에서 웹 클리너를 사용하면 입자가 웹 표면에서 제거되고 작동 대기에서 필터링되어 재오염을 방지할 수 있습니다. 이 단계에서는 오염 위험이 매우 높기 때문에 향후 전기 부족 및 값비싼 불량품의 위험을 피하기 위해 청소가 필수적입니다.
Similar to the post-slitting stage, during electrode cutting, particles and debris can contaminate the web. In order to avoid this, web cleaning at this stage will clean the surface of the substrate, leading to clean and clear separation layers.
와인딩 과정에서 우리는 최상의 결과를 위한 다양한 솔루션을 제안합니다. 권취하기 전에 기판 표면을 청소하여 배터리 필름 바람에 오염 물질이 갇히지 않도록 하는 것이 좋습니다. 위험하고 배터리 성능에 극도로 해로울 수 있는 정적 문제를 극복하려면 효과적인 정적 제어도 도입되어야 합니다. 이렇게 하면 와인딩 과정으로 인해 발생하는 정전기가 중화됩니다.
* All drawings show a CyClean-R profile. This is for illustrative purposes only. The web cleaner and position most suitable for your process will depend on certain factors of your application.
웹 클리닝 솔루션
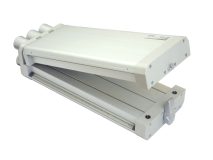
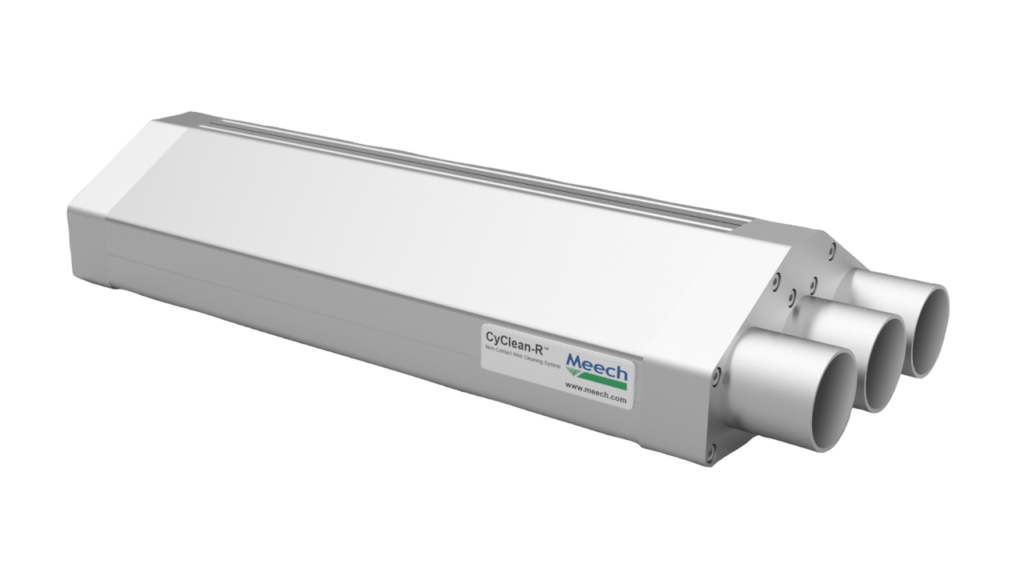
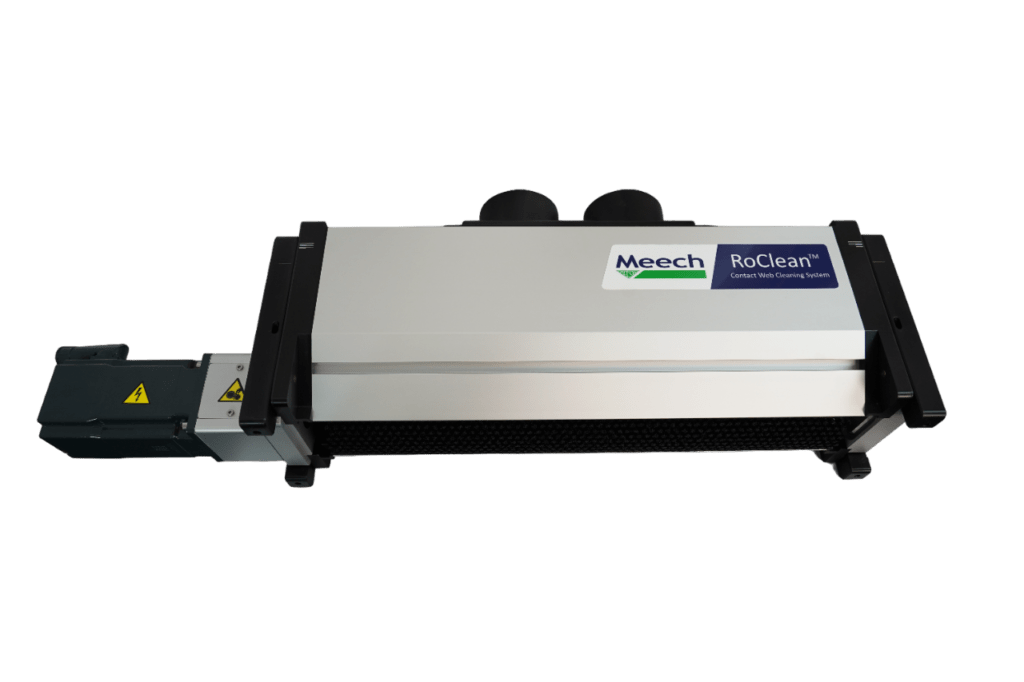
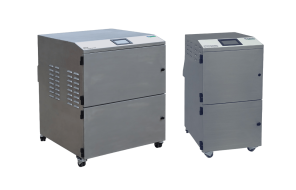
Meech CyClean™은 소형, 고성능, 비접촉 웹 클리너에 대한 수요에 부응하여 설계되었습니다.
CyClean은 첨단 전산유체역학을 적용하여 1미크론 미만의 오염물질을 제거하고 추출합니다.
CyClean-R은 저압 웹 클리닝을 위한 특수 솔루션을 제공합니다.
CyClean-R은 웹 장력이 가장 높은 롤러에 위치하도록 설계되어 장력이 낮은 문제를 우회하면서도 우수한 표면 청소 기능을 제공합니다.
RoClean은 배터리 필름 제조 산업에 탁월한 표면 청소 결과를 제공하는 최신 접촉식 웹 클리너입니다.
RoClean은 정전기 제어와 효율적인 강모 롤러 브러시를 모두 사용하여 웹 표면을 효과적으로 청소합니다.
Meech 웹 클리너에는 Meech 공기조화장치(AHU)가 함께 제공되어 공기 균형을 유지하여 공기압과 진공의 정확성을 완벽하게 제어합니다. 이는 컴팩트한 산업용 사양 장치이며 PLC 제어를 통해 성능을 모니터링할 수도 있습니다.
배터리 환경의 경우 독성 오염 폐기물 포집 및 작업자의 안전한 필터 제거를 향상시키기 위해 새로운 AHU 옵션이 개발되었습니다.
정적 제어 솔루션
24V DC로 구동되는 Hyperion 924IPS는 시중에서 가장 컴팩트한 펄스 DC 바입니다.
924IPS는 Meech의 ICM(이온 전류 모니터링) 기술을 갖추고 있어 바를 청소해야 할 때 로컬 및 원격 경고를 통해 성능이 유지되도록 보장합니다.
당사의 폐쇄 루프 피드백 시스템은 펄스 DC 이온화 시스템의 조정 가능한 균형을 활용합니다.
이 시스템은 Hyperion SmartControl과 폐쇄 루프 피드백을 위한 최대 5개의 Hyperion 이온화 제품으로 구성됩니다. SmartControl 센서에 연결되면 이온화 바의 웹 다운스트림 전압을 측정합니다.
이 측정값은 완전히 중립적인 웹을 달성하기 위해 출력 균형을 자동으로 조정하는 이온화 제품으로 피드백될 수 있습니다. 이는 항상 최고의 정적 제어를 달성하기 위해 지속적으로 측정하고 조정하는 지속적인 프로세스입니다.
모델 983v2 정적 위치 측정기는 재료의 정전기 전하를 명확하게 표시합니다. 일반 산업용으로 설계되었으며 200mm 거리에서 측정 시 +/-150kV의 넓은 측정 범위를 갖습니다.
983v2는 "연속" 또는 "피크 홀드" 모드에서 작동하여 각각 충전 수준의 변화 또는 감지된 최고 충전량의 변화를 기록할 수 있습니다. 이는 생산, 유지보수, 검사 및 품질 엔지니어가 사용하는 정전하 수준에 대한 좋은 표시를 제공하는 데 적합합니다. 983v2는 정전기가 문제가 될 수 있는 모든 재료에 사용할 수 있습니다.
SmartControl Touch는 현대 자동화 산업의 요구 사항과 Industry 4.0의 성장을 충족하여 생산성과 출력 품질을 극대화하도록 설계된 Meech의 최신 혁신 기술입니다.
SmartControl Touch를 사용하면 사용자는 통합 터치스크린을 통해 또는 원격으로 연결된 여러 Hyperion 이온화 바와 센서의 성능을 모니터링, 제어 및 조정할 수 있습니다.
귀하의 배터리 제조 공정을 개선하는 데 도움을 드릴 수 있습니까?
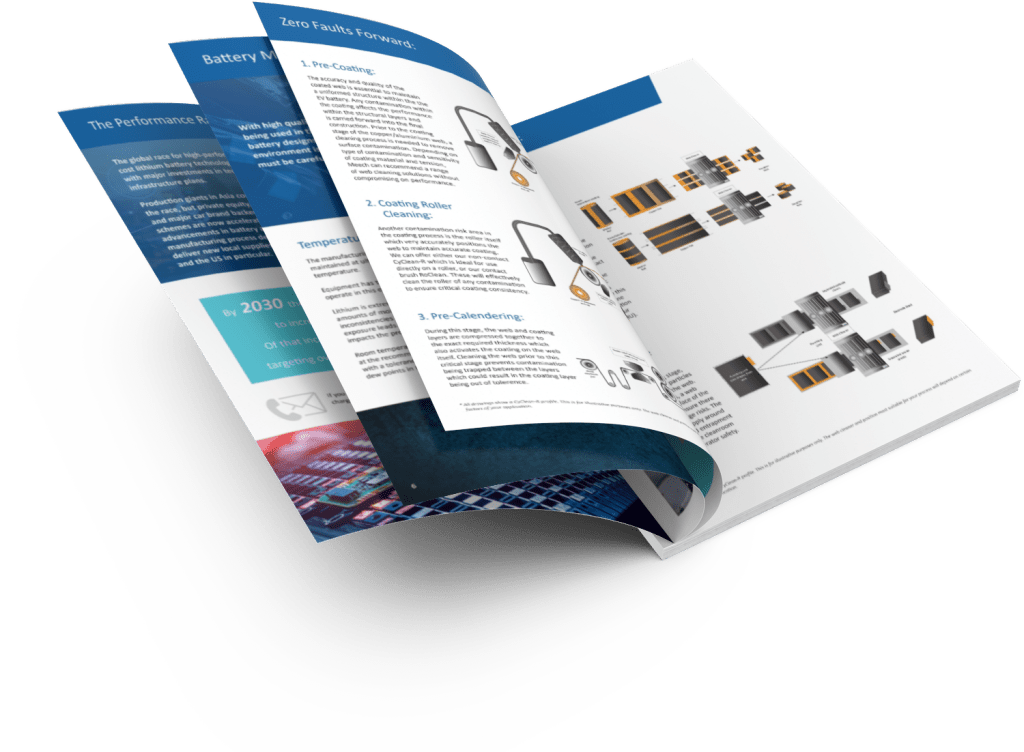