Батарея
Удаление загрязнений при производстве аккумуляторных элементов
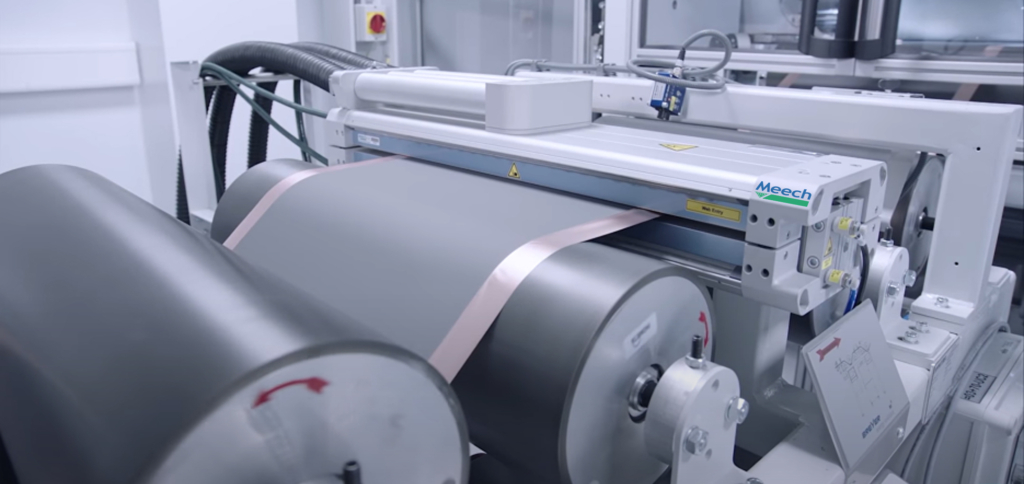
Рост рынка электромобилей в последние годы побудил производителей быстро разрабатывать и производить литий-ионные аккумуляторы, чтобы стимулировать бум продаж. В связи с открытием гигантских заводов по всему миру для удовлетворения спроса конкуренция растет, а качество имеет первостепенное значение.
В условиях быстрого развития технологий производители аккумуляторов стремятся создать батарею, которая могла бы конкурировать с автомобилями с бензиновым или дизельным двигателем, чтобы обеспечить впечатляющий запас хода и производительность.
Чтобы достичь этого, каждый этап процесса производства аккумуляторов должен быть тщательно проанализирован, чтобы получить наилучшие результаты.
Работа в условиях производства литиевых батарей:
Одним из важнейших направлений производства аккумуляторов для электромобилей являются условия производственной среды. От исходного сырья до сборки клеток условия производства должны строго контролироваться. Это создает проблемы как для производителей оборудования, так и для операторов. Есть 3 основные области критического рассмотрения:
Металлический литий чрезвычайно чувствителен даже к малейшему количеству влаги в воздухе и перепадам температуры на производстве.
Малейшее воздействие приводит к снижению производительности и сокращению срока службы литий-ионных аккумуляторов.
Температуру в помещении следует поддерживать на рекомендуемом уровне, около 25°C (77°F), с допуском +/(-) 2°C (36°F) и низкой точкой росы в диапазоне <1%.
Скорость воздухообмена в производственном помещении должна составлять от 20 до 50 воздухообменов в час при минимальном притоке свежего воздуха для создания положительного давления в помещении и необходимой вентиляции для операторов.
Загрязнения любого типа в материалах батареи или в обмотке элемента могут привести к прямому или мягкому отключению электроэнергии, что приводит к отказу в конце линии или снижению дальности действия батареи.
Условия чистых помещений ISO 8 (или выше), скорее всего, будут сосредоточены на удалении загрязнений из окружающей среды, а также с персонала.
Конечно, загрязнение не всегда можно удалить, поэтому все еще существует риск загрязнения и влияния на урожайность.
Проблемы и свободные частицы также могут возникнуть в процессах размотки/намотки, замены, нанесения покрытия, каландрирования, продольной резки, штамповки, лазерной резки и многого другого.
Все они могут проникнуть в слои анодной/катодной/сепараторной пленки.
Некоторые загрязнения будут представлять собой сухие, свободные, несвязанные частицы, тогда как другие будут влажными или связанными загрязнениями, которые труднее удалить.
Еще одной зоной риска является токсическое загрязнение материалов покрытия при их перемещении по роликам, резке, намотке и прокатке – оно может рассеиваться в воздухе и представлять опасность для дыхания оператора.
Статические заряды в производственной среде могут привести к ряду проблем:
Компоненты аккумуляторной батареи электромобиля очень чувствительны к статическому заряду — при этом компоненты необходимо разряжать.
Неконтролируемые статические заряды также влияют на поток материала и приводят к его неправильному поведению или поломке.
Если не контролировать статические разряды (искры), они вызовут поверхностные дендритные ожоги, влияющие на диэлектрические свойства сепараторной пленки, что приведет к неравномерному поведению заряда и разряда и выходу изделия из строя.
Статические заряды, образующиеся на изоляционных материалах, таких как сепарационная пленка, также притягивают частицы, увеличивая риск загрязнения.
Наш перспективный подход с нулевым уровнем ошибок
Мы определили ряд этапов процесса производства аккумуляторов, которые подвержены загрязнению на линии. Применяя правильные решения в этих точках, вы гарантируете отсутствие слабых звеньев в вашей производственной цепочке. Мы рассмотрим их ниже и продемонстрируем наши решения…
Перед нанесением покрытия на медно-алюминиевое полотно мы рекомендуем использовать очиститель полотна для удаления любых поверхностных загрязнений, которые могут повлиять на толщину и качество полотна с покрытием. Удаление загрязнений на этом этапе гарантирует, что нежелательные частицы не попадут в слои, что повлияет на производительность батареи в дальнейшем.
Чтобы избежать отпечатка каких-либо загрязнений с самого валика на покрытии подложки, мы предлагаем использовать либо наш CyClean-R, который идеально подходит для использования на валике, либо наш контактный RoClean. Это позволит эффективно очистить валик от любых загрязнений и исключить их попадание на полотно.
На этом этапе полотно и слои покрытия сжимаются до нужной толщины, активируя покрытие на самом полотне. Очистка полотна до этого критического этапа предотвращает попадание загрязнений между самими слоями.
Процесс продольной резки может привести к образованию большого количества мусора, который может загрязнить подложку полотна с покрытием. Использование очистителя полотна на этом этапе гарантирует, что частицы будут удалены с поверхности полотна и отфильтрованы из рабочей атмосферы, чтобы избежать повторного загрязнения. Учитывая такой высокий риск загрязнения на этом этапе, очистка необходима, чтобы избежать риска будущих перебоев в электроснабжении и дорогостоящего брака.
Как и на этапе после резки, во время резки электродом частицы и мусор могут загрязнять полотно. Чтобы избежать этого, очистка полотна на этом этапе очистит поверхность подложки, что приведет к получению чистых и четких разделительных слоев.
В процессе намотки мы предлагаем ряд решений для достижения наилучших результатов. Перед намоткой рекомендуется очистить поверхность подложки, чтобы не допустить попадания загрязнений в пленку аккумулятора. Чтобы преодолеть проблемы со статикой, которые могут быть как опасными, так и чрезвычайно вредными для работы батареи, необходимо также ввести эффективный контроль статики. Это нейтрализует любые статические заряды, возникающие в процессе намотки.
* На всех рисунках показан профиль CyClean-R. Это только для иллюстративных целей. Очиститель полотна и положение, наиболее подходящее для вашего процесса, будут зависеть от определенных факторов вашего применения.
Решения для очистки веб-страниц
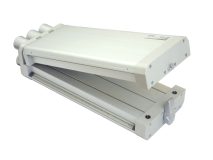
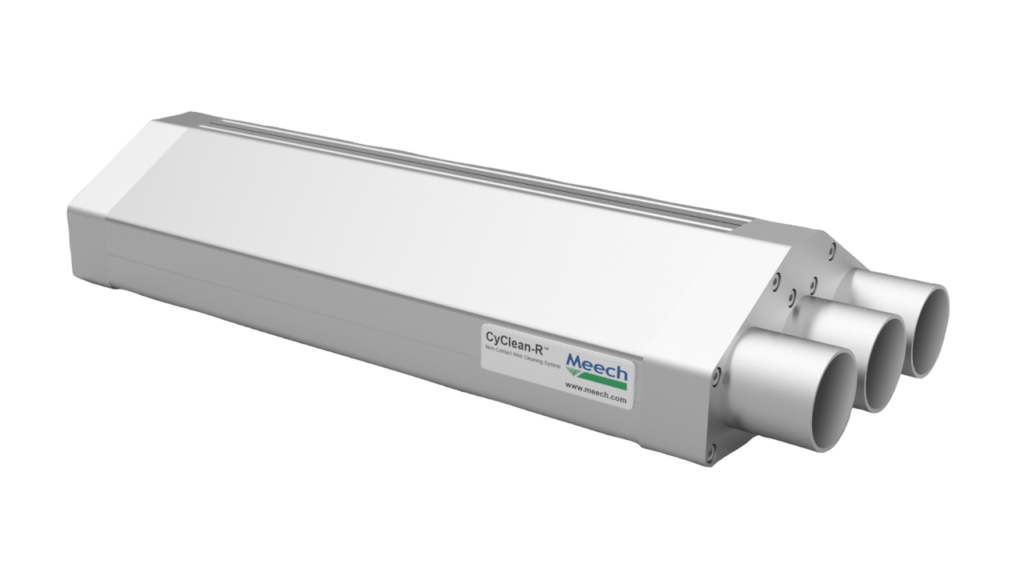
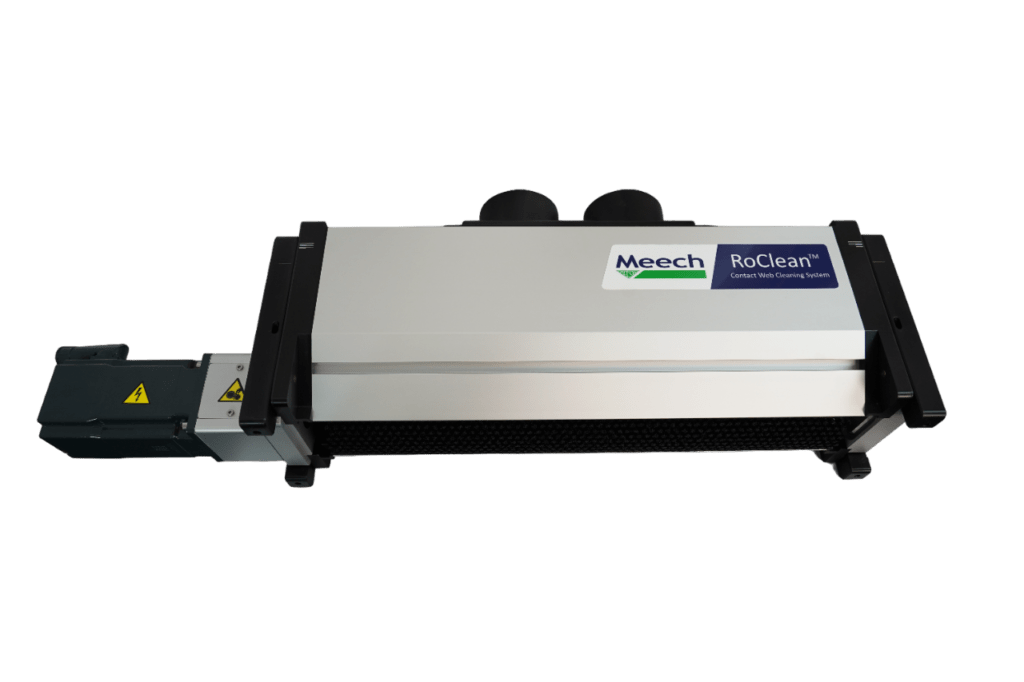
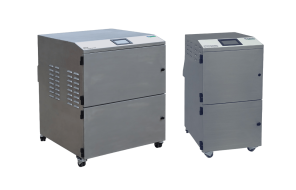
Meech CyClean™ был разработан в ответ на спрос на компактное, высокопроизводительное бесконтактное средство для очистки полотна.
Благодаря применению передовой вычислительной гидродинамики CyClean удаляет и извлекает загрязнения размером менее 1 микрона.
CyClean-R представляет собой специализированное решение для очистки полотна с низким натяжением.
CyClean-R предназначен для установки на валик, где натяжение полотна максимальное, что позволяет обойти проблемы низкого натяжения и при этом обеспечить превосходную очистку поверхности.
RoClean — это новейший очиститель контактного полотна, обеспечивающий превосходные результаты очистки поверхности для промышленности по производству аккумуляторной пленки.
RoClean эффективно очищает поверхность полотна благодаря использованию как статического контроля, так и эффективной щетинной роликовой щетки.
Очистители полотна Meech поставляются с блоками обработки воздуха Meech (AHU), обеспечивающими поддержание воздушного баланса и идеальный контроль точности давления воздуха и вакуума. Это компактные устройства промышленного назначения, производительность которых также можно контролировать с помощью ПЛК.
Для аккумуляторных батарей была разработана новая опция AHU, позволяющая улучшить улавливание токсичных загрязнений и безопасное удаление фильтра оператором.
Решения для статического контроля
Hyperion 24IPS, работающий от источника постоянного тока 924 В, является самой компактной импульсной планкой постоянного тока, доступной на рынке.
Модель 924IPS оснащена технологией мониторинга ионного тока (ICM) Meech, которая обеспечивает поддержание производительности с помощью локальных и удаленных предупреждений, когда планка нуждается в очистке.
Наша система обратной связи с обратной связью использует преимущества регулируемого баланса импульсных ионизирующих систем постоянного тока.
Система включает в себя Hyperion SmartControl и до 5 ионизирующих устройств Hyperion для обратной связи с обратной связью. После подключения к датчику SmartControl измеряет напряжение на ленте после ионизирующей планки.
Это измерение может быть передано обратно на ионизирующий продукт, который автоматически регулирует баланс выходного сигнала для достижения полностью нейтрального полотна. Это непрерывный процесс, который постоянно измеряет и корректирует для достижения наилучшего статического контроля в любое время.
Статический локатор модели 983v2 обеспечивает четкую индикацию электростатических зарядов материалов. Он предназначен для общепромышленного использования и имеет широкий диапазон измерения +/- 200 кВ, измеренный на расстоянии 150 мм.
983v2 может работать в режиме «Непрерывный» или «Удержание пикового значения» для регистрации изменений уровня заряда или самого высокого обнаруженного заряда соответственно. Он подходит для надежного определения уровня статического заряда для использования инженерами по производству, техническому обслуживанию, контролю и качеству. 983v2 можно использовать с любым материалом, для которого может возникнуть проблема со статическим зарядом.
SmartControl Touch — это новейшая инновация от Meech, разработанная для удовлетворения потребностей современных автоматизированных отраслей и развития Индустрии 4.0 для достижения максимальной производительности и качества продукции.
SmartControl Touch позволяет пользователю отслеживать, контролировать и регулировать работу нескольких подключенных ионизирующих стержней и датчиков Hyperion через встроенный сенсорный экран или удаленно.
Можем ли мы помочь улучшить процесс производства аккумуляторов?
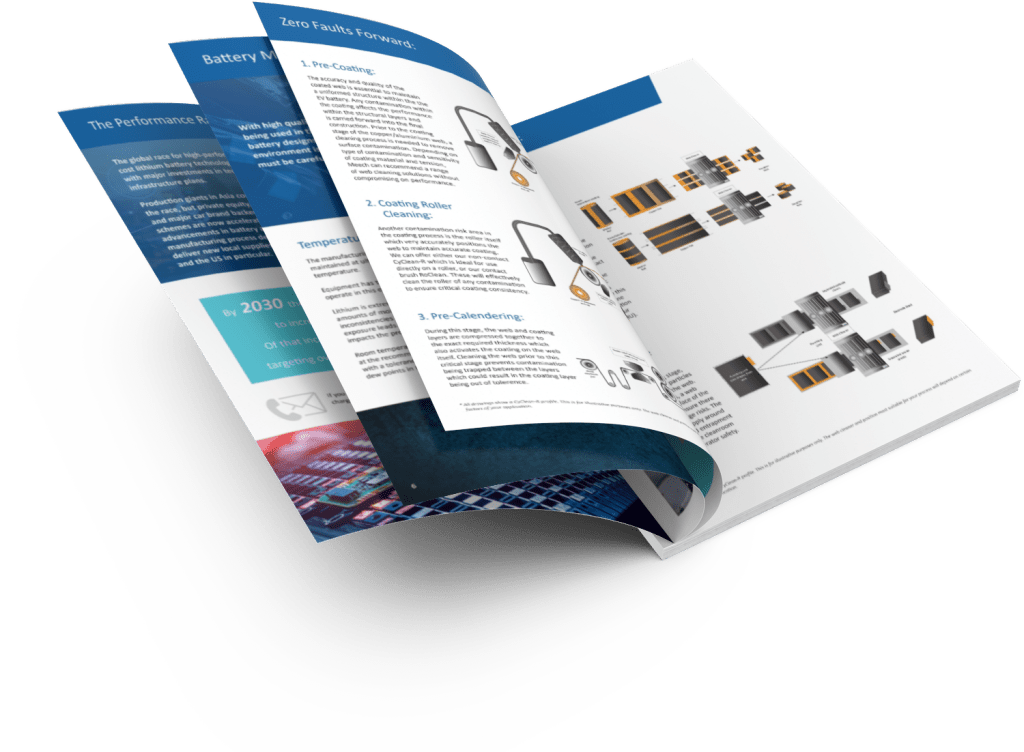