Automotive
Contamination removal in automotive production
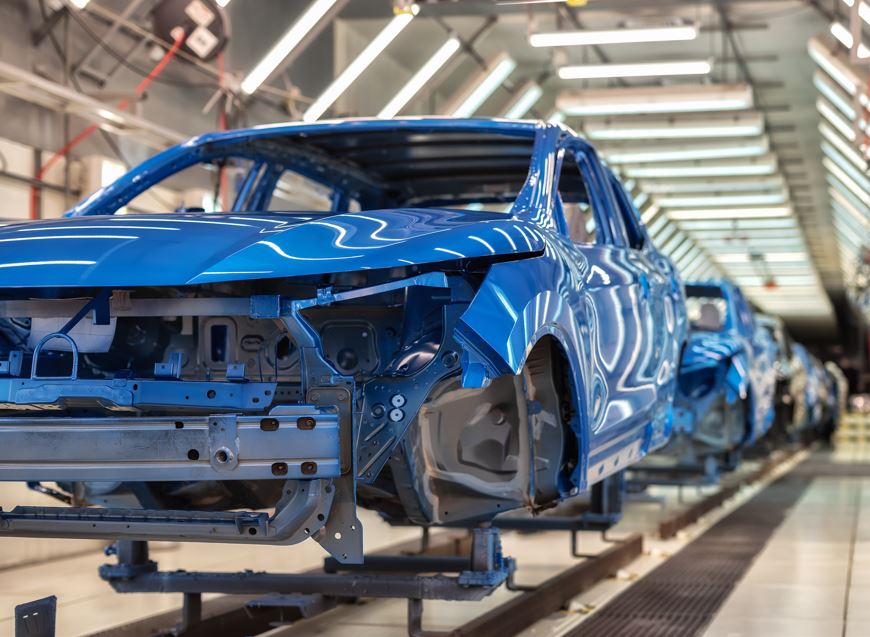
Issues relating to static charges within the automotive industry are vast and can occur at multiple stages throughout manufacturing process. Problems arising from static and ensuing contamination (such as dust build-up) are particularly common in both injection moulding and blow moulding, as well as vacuum forming, part spraying and extrusions.
Other processes such as painting, sealing, and coating vehicle bodies and components also require the surfaces to be dust and contamination free. If not, then static charges can lead to defects such as blending issues, shading and uneven application; resulting in failed quality checks, slowed production rates, and increasing costs.
Meech Static Eliminators Ltd, offer an advanced range of static control, air technology and surface cleaning technology solutions designed to neutralise static charges and remove surface particles, enabling clean and contamination free production.
Our Zero Faults Forward Approach
We have identified a number of manufacturing applications within the automotive industry that are prone to contamination on the line. By applying the right solutions at these points, you make sure there are no weak links to your production chain. We explore these below and demonstrate our solutions…
Automotive manufacturing applications
It is critical that static electricity is controlled during the manufacturing of automotive supplies. Below are some of the main areas affected by static charges during production, and our solutions to remove static charges and other contaminants
Removal of surface contamination from automotive bodies and body parts prior to the primer application stage.
Automotive bodies and car parts are often covered in contamination from previous production processes and because static charges are inherent in plastic components, this causes more contamination to be attracted. The neutralisation of any static charges on the parts and removal of surface contamination is vitally important prior to the parts entering the paint booth. The cost of a poor-quality paint finish includes the cost of rework and rejection and reduced productivity.
Solution: Use of an air knife surface cleaning system that uses a powerful blade of fan blown ionised air to remove unbonded surface contamination from the target area.
Surface cleaning and static neutralisation of automotive plastic mouldings.
The focus is on enabling the best possible paint finish by the removal of contaminants (dust, dirt, fibres) prior to painting. This reduces the level of product rejects reducing the cost of rejection and rework by increasing the first-time pass rate.
Solution: Use of an air knife surface cleaning system that uses a powerful blade of fan blown ionised air to remove unbonded surface contamination from the target area.
Static neutralisation and cleaning of automotive light clusters and other 3D components prior to assembly
When automotive light clusters and other 3D components are assembled electrostatic charges must be neutralised and contamination removed in order to ensure the desired quality of the final part. Cleaning of parts is often a manual process that takes time and is not consistent. Also, manual cleaning processes prior to assembly can result in contamination being blown into the local atmosphere and contaminating other nearby parts.
Solution – Use of an automated surface cleaning system that uses high volume ionised fan blown air to quickly eliminate static charges and effectively remove and contain unbonded contamination from 3D parts.
* All drawings are for illustrative purposes only. The position of the static control solutions most suitable for your process will depend on certain factors of your application.
Web Cleaning Solutions
Meech is a leading Web Cleaning manufacturer with a comprehensive range of four systems. Each system is based on a different cleaning principle, this uniquely allows us to provide our customers with a system best suited for their application. All Meech systems incorporate the latest shockless AC static control bars as standard which is crucial for comprehensive contamination removal. Meech has more than 200 successful web cleaning installations in a range of industries including Packaging, Printing and Converting.
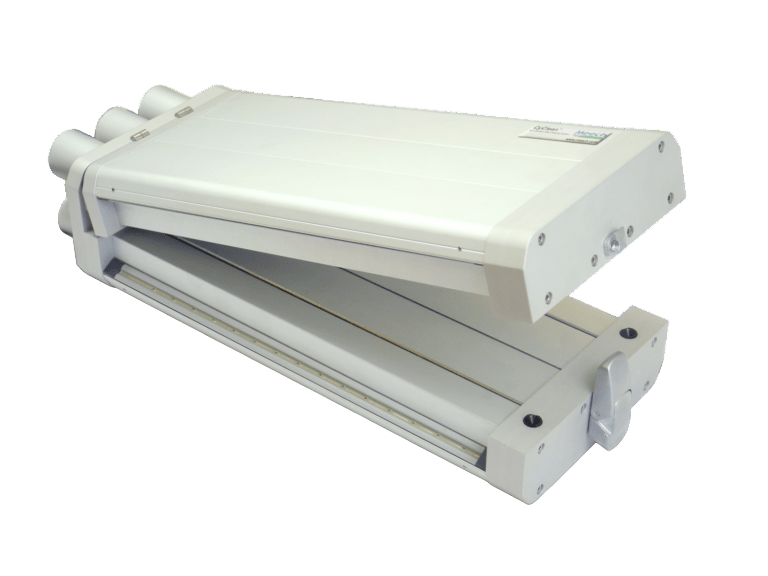
Meech CyClean™ has been designed in response to demand for a compact, high performance, non-contact web cleaner.
Through the application of advanced computational fluid dynamics, CyClean removes and extracts contamination below 1 micron.
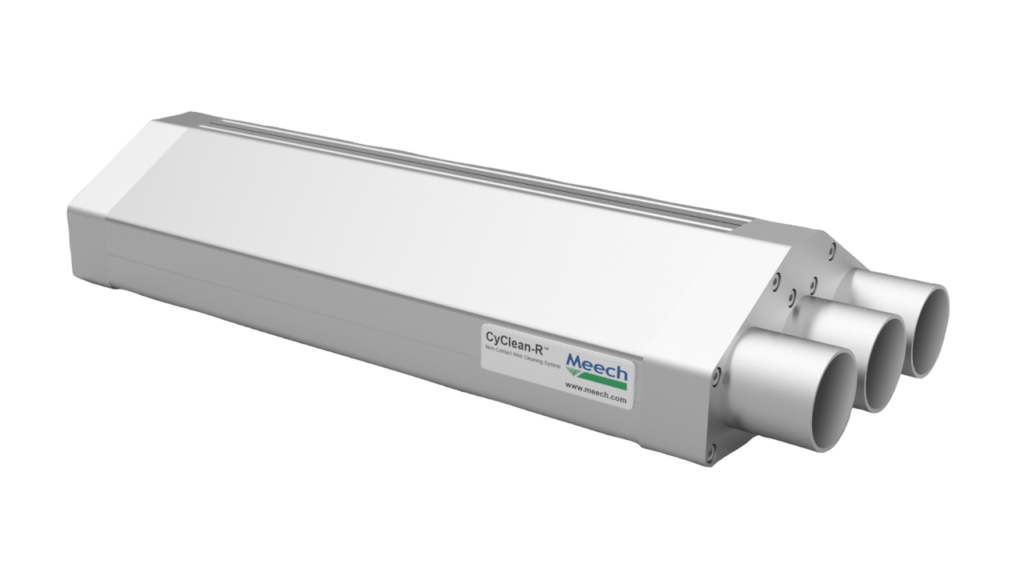
The CyClean-R provides a specialised solution for low-tension web cleaning.
The CyClean-R is designed to be positioned on the roller, where the web tension is at its highest, therefore bypassing the issues of low tension and still delivering excellent surface cleaning.
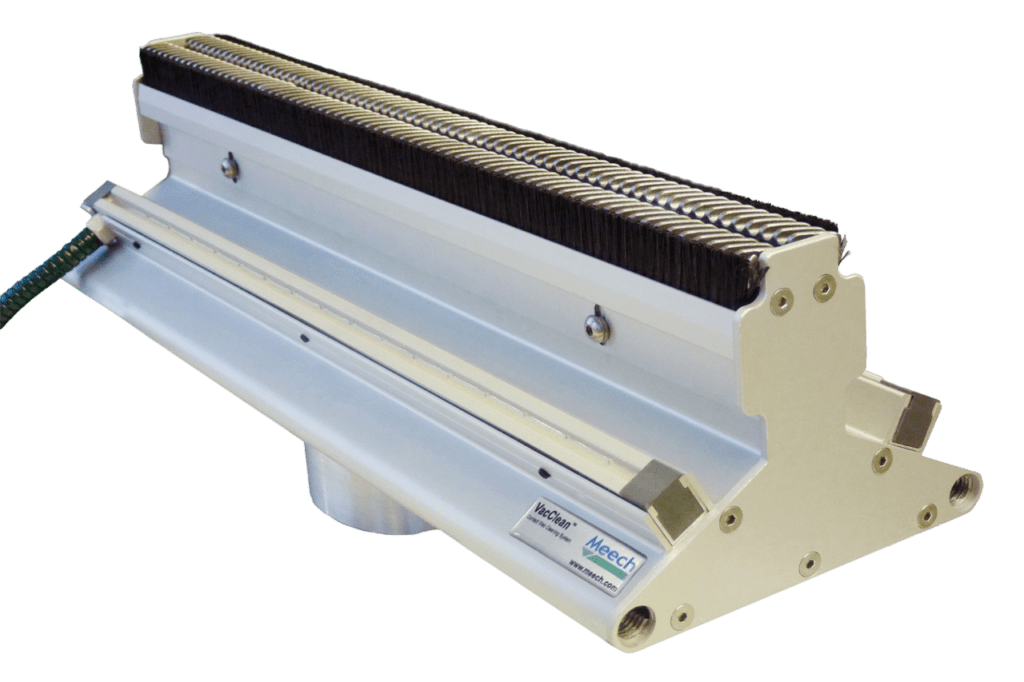
The Meech VacClean™ contact web cleaning system is an evolution of Meech’s successful Tornado system, of which there are hundreds of installations globally. VacClean systems incorporate an enhanced contact cleaning manifold with either an Air Handling Unit (AHU) or vacuum fan unit, depending on the installation environment and web width.
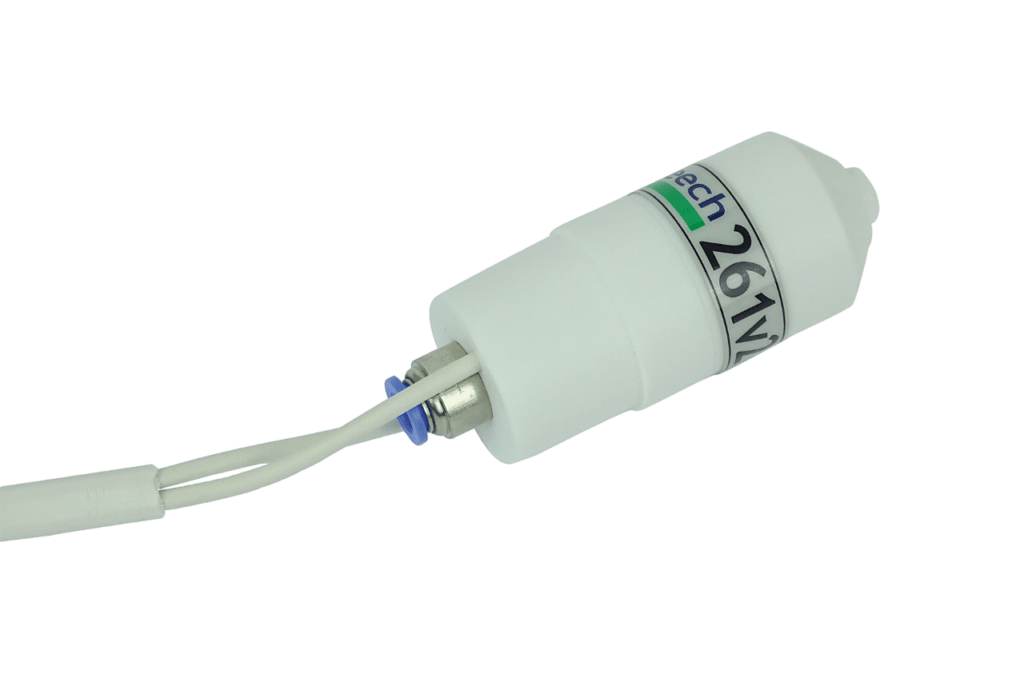
The Model 261v2 Ion Nozzle is a small, robust ionising nozzle and provides an ionised airflow for cleaning and neutralising static charges. It is powered by a Meech Model 233v4 and is suitable for industrial, electronic and cleanroom environments and is quick to install and easy to use.
Static Control Solutions
Meech is a market leader in manufacturing and supplying static control products since the 1960’s; offering a wide range of electrostatic products that provide anti-static and ESD protection and measurement, static generation, electrostatic control and elimination.
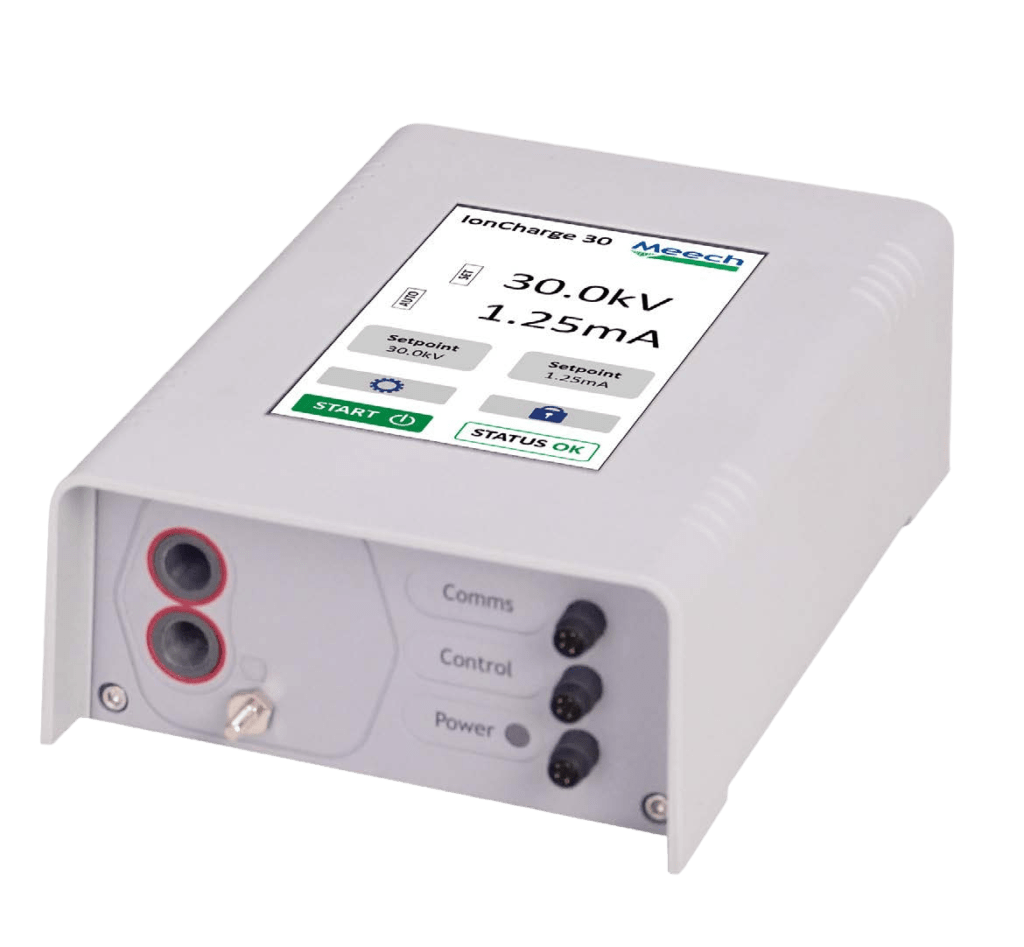
IonCharge30 has 15 watt power output and provides a 0-30kV voltage range. It uses advanced high voltage technology and software for a controlled static charge via our range of static generator bars and pinning heads.
The static charge can be either positive or negative (model dependant) and is used to impart temporary bonding between materials, at least one of which is insulative.
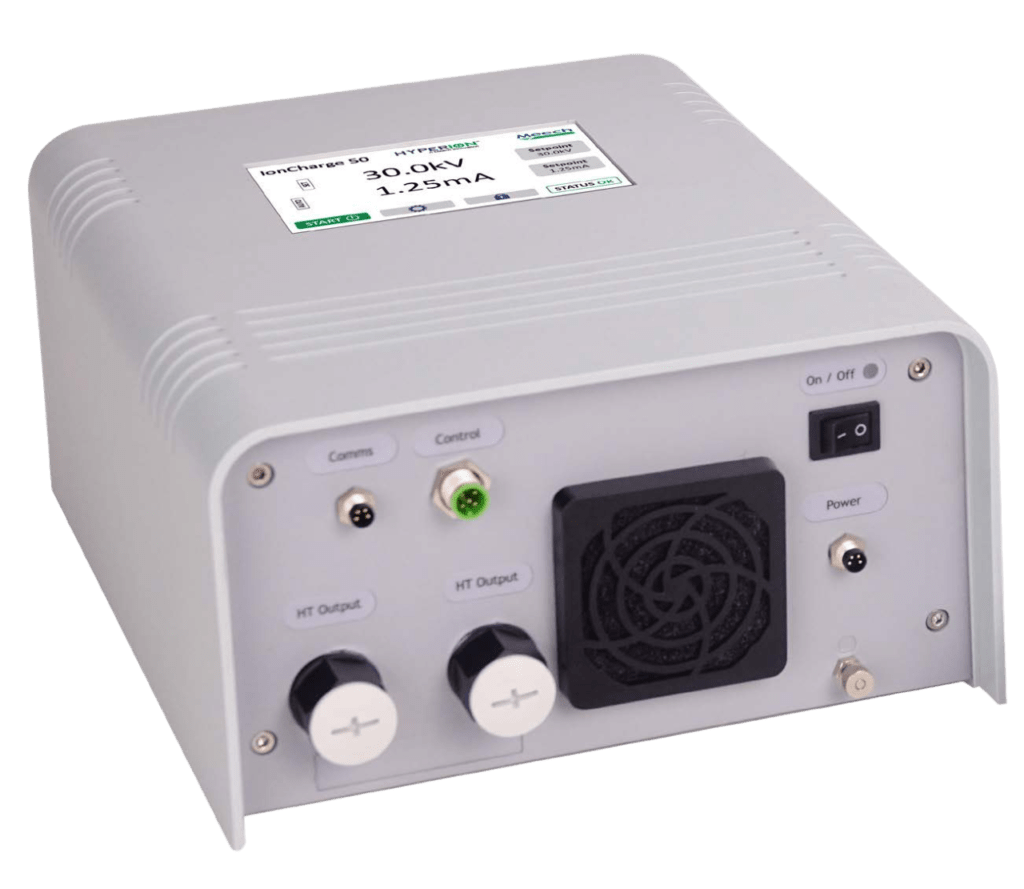
IonCharge50 has a 75W power output and provides a 0-50kV voltage range. It uses advanced high voltage technology and software for a controlled static charge via our range of static generator bars and pinning heads.
The static charge can be either positive or negative (model dependant) and is used to impart temporary bonding between materials, at least one of which is insulative.
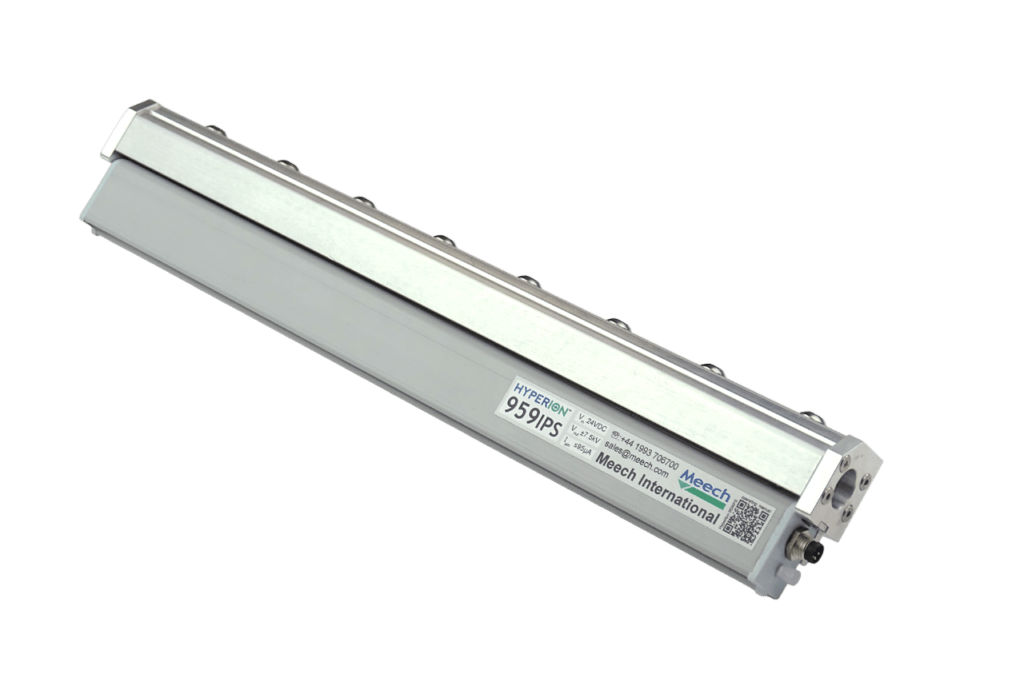
The Hyperion 959IPS ionising air curtain is an extremely versatile product that provides effective static neutralisation and dust removal.
Comprised of a Hyperion 924IPS mounted on a Meech energy saving air curtain it provides a high speed laminar sheet of ionised air.
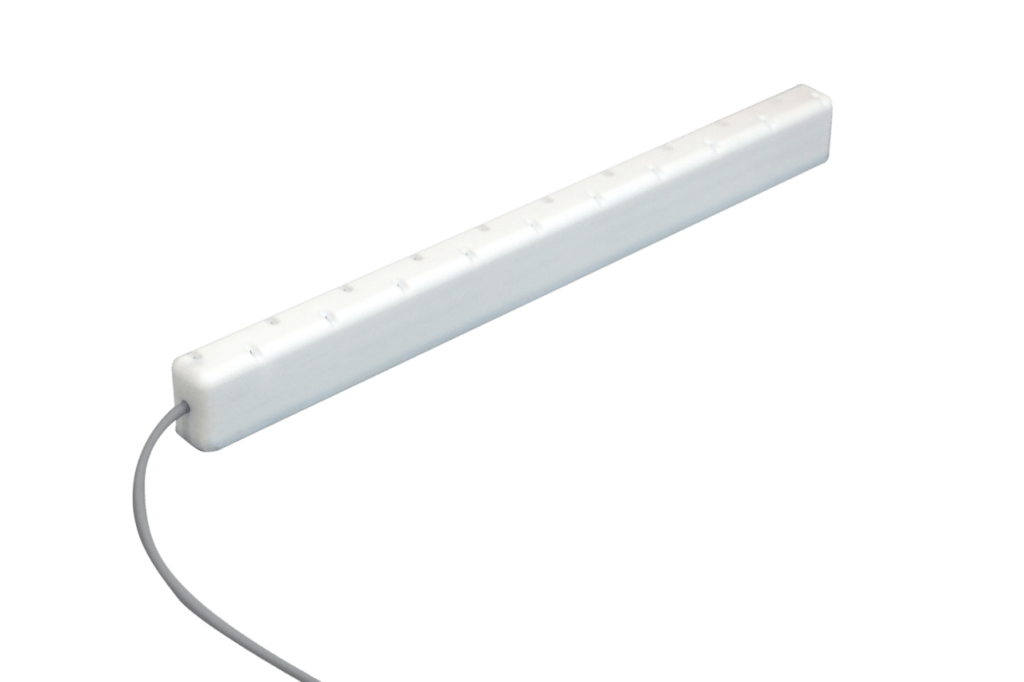
The 314IPS is a short range compact pulsed DC ionising bar specifically designed for use in hygienic applications.
Its PTFE construction is ideally suited to use on Hygienic food and pharmaceutical machinery.
Could we help improve your automotive manufacturing process?
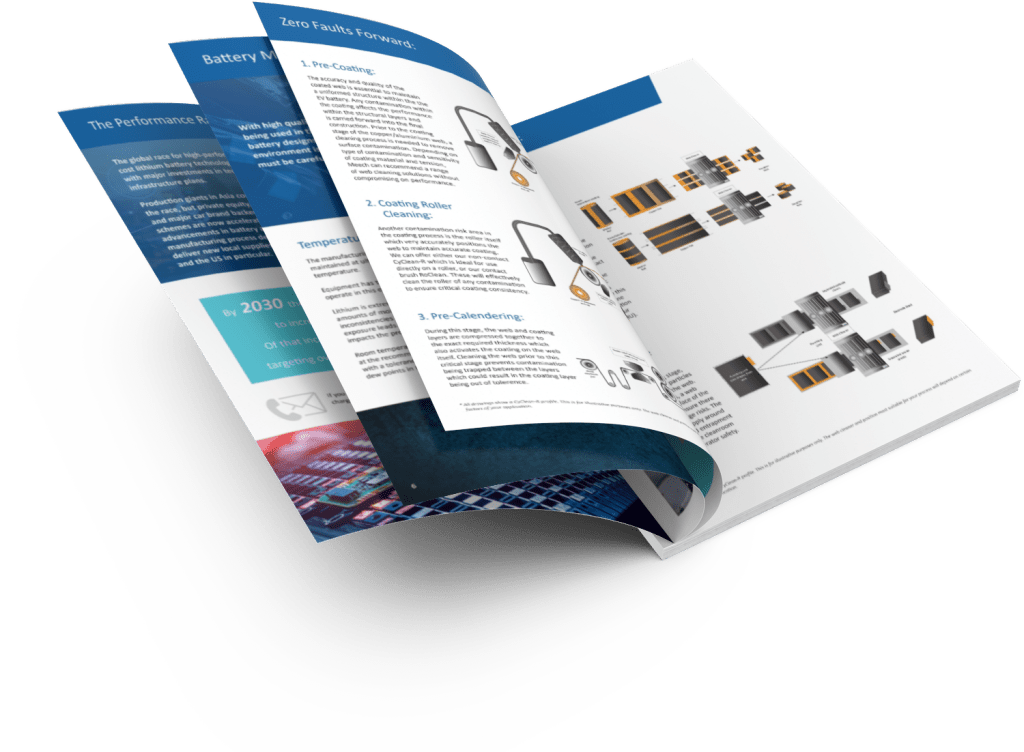