Electronics
Contamination removal in electronic manufacturing
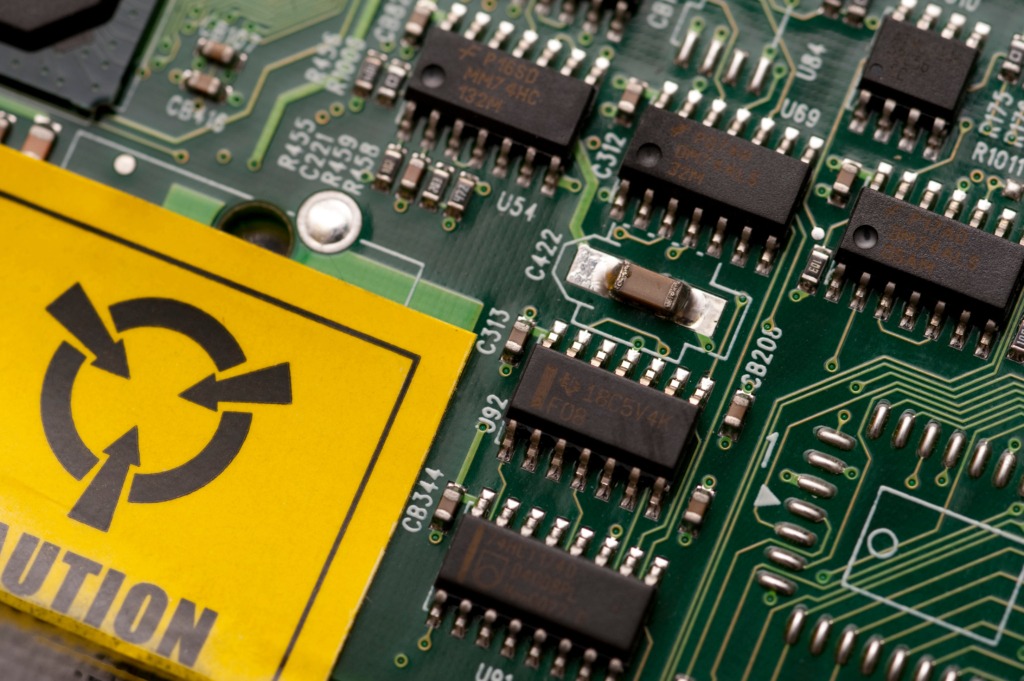
Electrostatic discharge (ESD) is a common and significant problem within the electronics industry.
If two items are at different levels of Electrostatic charge (i.e. one is positively and the other one negatively charged), they will want to come into balance. If they are in close enough proximity, there will be a rapid, spontaneous transfer of electrostatic charge. ESD damage can be either immediate and catastrophic meaning the device or components stops functioning immediately and is detected during production inspections.
Sensitive components such as integrated circuits and diodes are particularly susceptive to ESD. Therefore, managing the risks posed by ESD is critical in electronics manufacturing.
Here at Meech Static Eliminators Ltd, we offer an advanced range of industrial static control solutions that are designed to neutralise the static charges on materials and avoid ESD related issues.
Operating in the electronic manufacturing environment:
One of the critical focus areas for electronic production is the manufacturing environment conditions. During production, there are several risks arising from static electricity:
Controlling contamination resulting from Electrostatic discharge is crucial in all electronic manufacturing processes.
This is because dust and other small particles can lead to a range of costly and even dangerous issues; from product performance degradation and catastrophic failure, to causing fires and even explosions within flammable environments.
Dust gets into and clogs small spaces, subsequently restricting air flow and trapping heat, leading to component degradation.
Repeated friction and separation (from feeder bowl vibrations) charges Electronic components with static electricity. As a result, the charged components then cannot be transferred properly due to the components clinging to the bowl or chute.
A static charge is an electrical charge at rest on an object. As it builds, it looks for somewhere to discharge, which can result in two types of failure:
1. Catastrophic failure: This occurs when an ESD event immediately renders the part or component useless. A catastrophic failure requires complete replacement of the damaged component before further work can be carried out.
2. Upset failure: This occurs when an ESD has caused a current flow that is not powerful enough to cause complete failure, but strong enough to cause intermittent gate leakage, resulting in malfunction and degrading performance.
Sensitive electronic components (such as integrated circuits and diodes) are particularly susceptible to static electricity, but as electronic technology advances and the components get progressively smaller in size, the circuitry within them gets smaller too, which increases their sensitivity to ESD.
Shocks from Induced Charge:
If the operator is handling materials that are charged, the charge will build up in the body because of their insulative shoes. This build up stays in the body until the operator touches an earthed part of the machinery, when the charge will instantly transfer to the earth and result in a shock.
Shocks from the Product:
Metal objects within an electrical field that are not connected to earth can become induction charged, and as the metal part is conductive, the will be mobile and will discharge when touched by the operator.
ESD occurs when two objects with different electrical charges make contact with each other. When this happens, the charge transfers from one object to the other causing a spark, which can be powerful enough to ignite and set fire to nearby materials, and in some cases, explosions.
It is estimated that the electronics industry incurs approximately £40 billion in losses each year due to ESD damage alone.
We understand these crucial requirements and have tested our equipment in clean rooms and test chambers. Drawing from our expertise and core competencies, Meech offers a tailored range of solutions to remove static charges and contamination, in order to deliver a zero faults forward approach at each application stage.
Our Zero Faults Forward Approach
We have identified a number of stages during electronic manufacturing that are prone to contamination. By applying the right solutions at the right points, you can eliminate the risks and potential hazards associated with ESD and subsequent contamination. We explore these below and demonstrate our solutions.
Electronic Applications
It is critical that static electricity is controlled during the manufacturing of electronic components and devices. Below are some of the main areas affected by static charges during production, and our solutions to remove static charges and other contaminants:
Production lines
Production lines in the electronics industry (particularly those for flat panel screen products) are high risk environments for electrostatic discharge, due to the build-up of static during the assembly process.
Electrostatic discharge (ESD) can destroy sensitive electronic components or cause damage that may not become evident for weeks or even months later. Products that don’t pass quality checks are often marked for immediate disposal, while latent defects, identified later in the product’s life, can cause deterioration in performance. Without reliable static control measures in place, electronics manufacturers risk incurring increased costs due to avoidable product failure, while also suffering consumer dissatisfaction and a potentially damaged reputation.
However, installing the appropriate Ionising equipment will neutralize static charge and prevent damage to electronic devices and products.
Ionising Nozzles and Ionising guns can also be used in confined areas or to target treatment areas in order to reduce and prevent static build up.
Cleanrooms
Electronic cleanrooms are strictly controlled spaces designed to keep out air contaminants of a certain level and ensure sterility of the electronics manufacturing environment. This is why cleanrooms are used during the most critical stages of the electronics manufacturing process.
Therefore, installing the correct ESD control equipment is crucial in order to maintain the correct environment.
Ionisation bars provide a non-contact solution and are an ideal as part of an integrated electrostatic control system, helping to eliminate dust and other foreign particles.
DC Ionising Nozzles are also used to remove both static charges and dust. Our range allows for the delivery of ionised air with accuracy into areas that are difficult to reach, where conventional systems would otherwise be ineffective or impossible to install.
* All drawings are for illustrative purposes only. The position of the static control and web cleaning solutions most suitable for your process will depend on certain factors of your application.
Web Cleaning Solutions
Meech is a leading Web Cleaning manufacturer with a comprehensive range of four systems. Each system is based on a different cleaning principle, this uniquely allows us to provide our customers with a system best suited for their application. All Meech systems incorporate the latest shockless AC static control bars as standard which is crucial for comprehensive contamination removal. Meech has more than 200 successful web cleaning installations in a range of industries including Packaging, Printing and Converting.
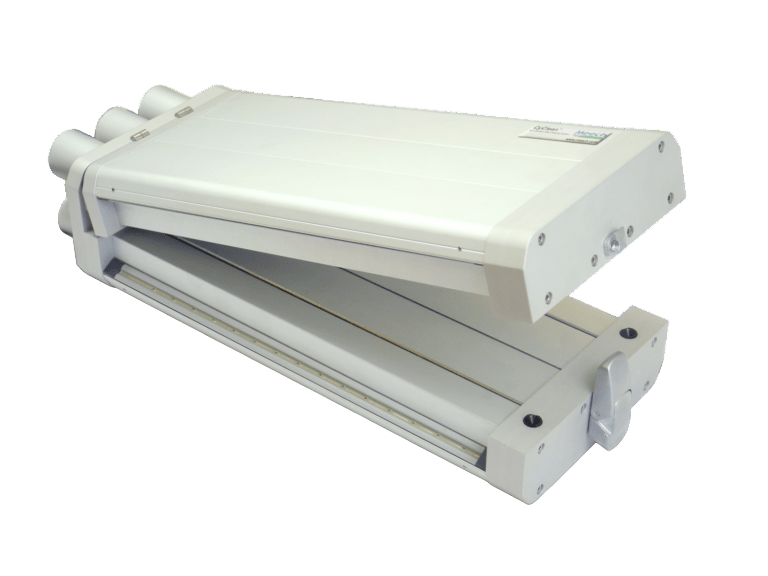
Meech CyClean™ has been designed in response to demand for a compact, high performance, non-contact web cleaner.
Through the application of advanced computational fluid dynamics, CyClean removes and extracts contamination below 1 micron.
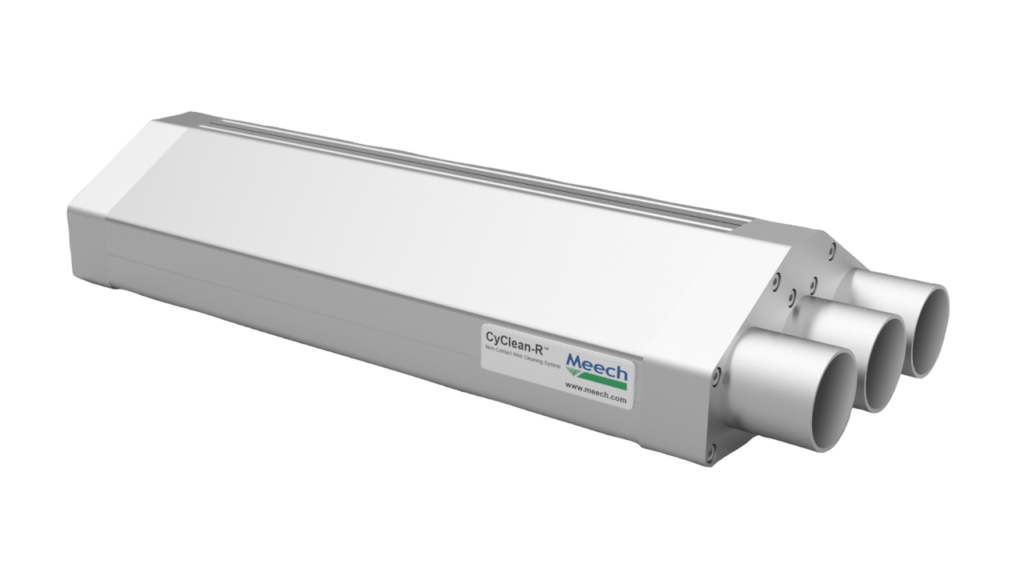
The CyClean-R provides a specialised solution for low-tension web cleaning.
The CyClean-R is designed to be positioned on the roller, where the web tension is at its highest, therefore bypassing the issues of low tension and still delivering excellent surface cleaning.
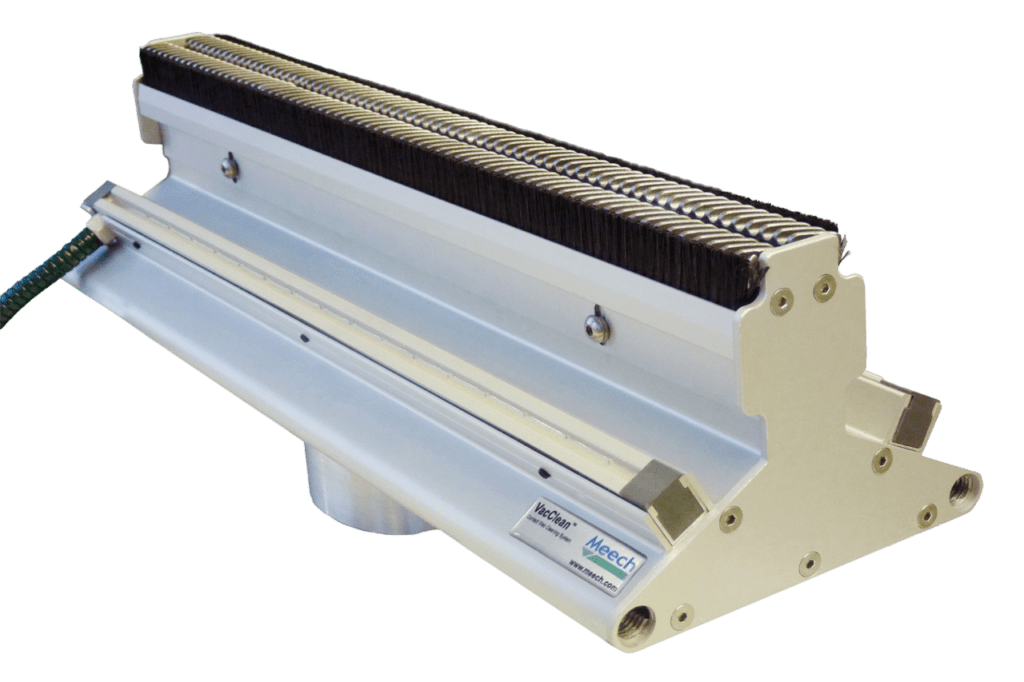
The Meech VacClean™ contact web cleaning system is an evolution of Meech’s successful Tornado system, of which there are hundreds of installations globally. VacClean systems incorporate an enhanced contact cleaning manifold with either an Air Handling Unit (AHU) or vacuum fan unit, depending on the installation environment and web width.
Static Control Solutions
Meech is a market leader in manufacturing and supplying static control products since the 1960’s; offering a wide range of electrostatic products that provide anti-static and ESD protection and measurement, static generation, electrostatic control and elimination.
The Meech 971IPS-30 Extra Long-Range Pulsed DC Ionising Bar is the latest addition to the Meech Hyperion Range.
The 971IPS-30 is powered by an integrated +/- 30kV 24V DC power supply, making it the most powerful ionising bar in Meech’s range.
The 971IPS-30 is suitable for ultra-long range applications from 450 to 1500mm.
Equipped with Meech’s Ion Current Monitoring (ICM) technology, beam performance is maintained with local and remote alarms indicating when the beam needs cleaning. The Hyperion BarMaster remote programmer can also be used to adjust the frequency and balance of the bar, optimizing it for each application.
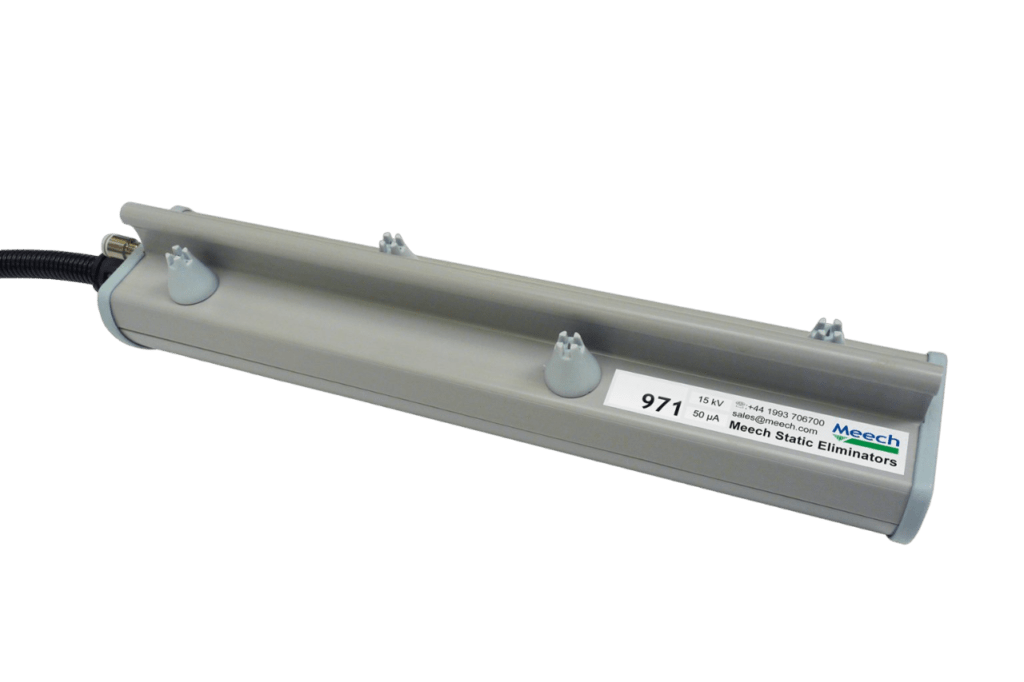
The Meech 971IPS-30 Extra Long-Range Pulsed DC Ionising Bar is suitable for ultra-long range applications from 450 to 1500mm.
Equipped with Meech’s Ion Current Monitoring (ICM) technology, performance is maintained with local and remote alarms indicating when the bar needs cleaning. The Hyperion BarMaster remote programmer can also be used to adjust the frequency and balance of the bar, optimizing it for each application.
The 650QAC ionising bar from Meech is the latest addition to the Hyperion range. It’s advanced design features new technology to achieve a very low and stable offset voltage. This level of ionisation performance is often required in the electronics industry where ESD (electrostatic discharge) control standards requires ionising devices with offset voltages of less than +/- 35V.
To optimise performance, the bar also has the unique ability to enable bar mounting distance presets via the 650QAC integrated touchpad. Further adjustments can be made to settings if necessary, offering users peace of mind that the bar is optimised for the application, therefore reducing staff downtime and saving time and costs. These innovative features set it apart from alternative products on the market.
Could we help improve your battery manufacturing process?
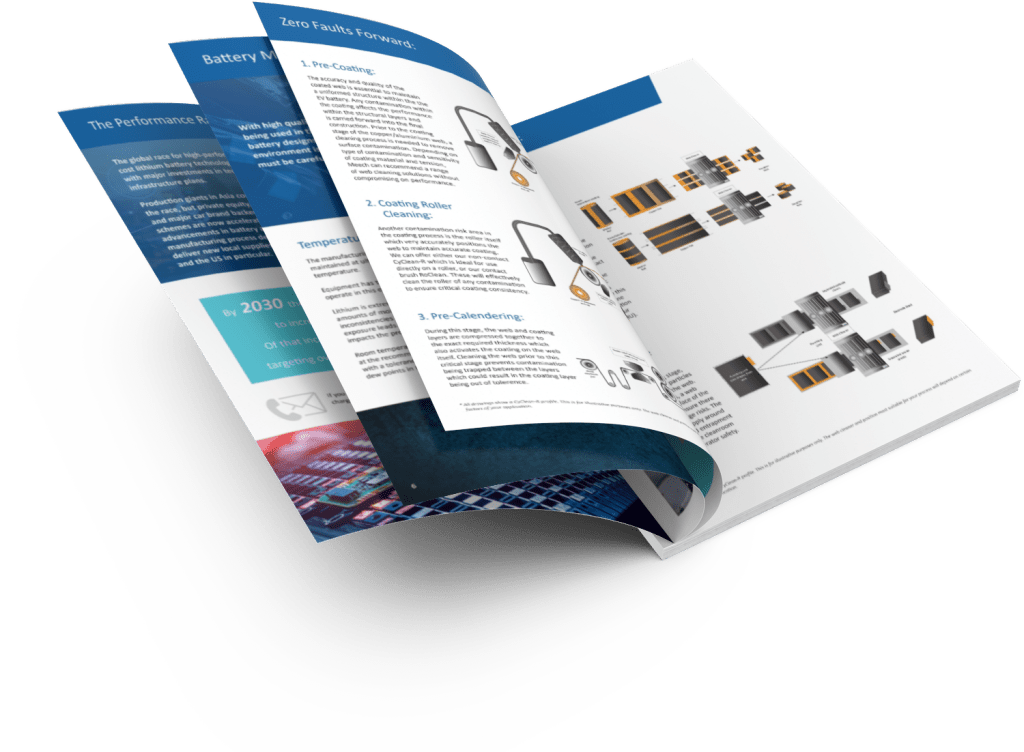