Medical
Contamination removal in medical supply production
During the production of medical devices and other medical supplies, high levels of static charge result in issues with contamination, and difficulties with packing.
Static charges can cause dust and other airborne contaminants to be attracted to the surface of a moving web (typically plastic and silicone products and packaging), which could lead to costly rejections if untreated.
However, implementing the correct Static control and web cleaning solution can eliminate these charges, resulting in clean, contamination free production.
Our Zero Faults Forward Approach
We have identified a number of applications within medical supply manufacturing that are prone to contamination on the line. By applying the right solutions at these points, you make sure there are no weak links to your production chain. We explore these below and demonstrate our solutions…
Medical supply applications
It is critical that static electricity is controlled during the manufacturing of medical supplies. Below are some of the main areas affected by static charges during production, and our solutions to remove static charges and other contaminants:
Contamination & ESD Control during Conveying & Collection of Injection Moulded Parts
Static charges on mouldings may cause them to stick to the conveyor. As mouldings fall into the collection bin the “battery effect” can result in a huge charge being accumulated. This causes a high level of dust attraction and operator shocks. Solution : An ionising bar positioned over the conveyor and collection bin will neutralise the static charges. Mouldings release readily from the conveyor into the collection bin without further dust contamination. Productivity is improved and operator shocks eliminated.
Static Pinning of Non-woven Materials (e.g. Face masks)
Face masks have always been an important piece of PPE equipment, especially in the medical sector.
Face masks are made from multiple layers of material that are charged and pinned together using static generation products. The performance of the face mask filtration is also aided by the static charge used as the higher the charge retention in the material, the greater the filtration potential.
For more information, view our Face Mask Manufacture: Industry Guide HERE.
Contact Lens Manufacture
Static charges throughout the manufacturing process of contact lenses results in several issues that affect the production process. This includes product and packaging contamination and product handling.
Medical Device Blister Packaging
Problem:
Friction generated during the unwinding of the roll of thick plastic film used for blister packing creates static charges that attract contamination from the surrounding area onto the film. During the heating and forming of the film to produce the blisters, the contamination bonds to the plastic film, creating permanent inclusions and potential scrap. The warm plastic generates even more static charges as it cools. This will result in further contamination being attracted such as operator hair or skin.
Static charges on the blister pack can also cause repelling or misalignment of the medical device as it is inserted into the blister packaging.
Solution:
A non contact web cleaner mounted prior to thermoforming is ideal for removing and capturing contamination from the roll of material.
Controlling static charges during product packing will allow the product and clean blister packaging material to come together, preventing product misbehaviour and inclusion of contamination. This can be done using a ionising bar.
Web Cleaning Medical Bandage
Cleaning of the web material prior to adhesive coating is an important part of the production process.
Depending on the contamination to be removed a contact or non-contact web cleaner can be used.
Web Cleaning Medical Blood Bags
Problem:
During the production of blood bags the unwinding of the plastic web will generate static electricity which attracts dust and other airborne contaminants to the film. If the two layers of film are then sealed to make the blood bag the blood bags will be unusable.
Solution:
Use of a non-contact web cleaning system to remove the static charge and remove the contamination prior to the two layers being sealed.
Vibration Bowl Feeders
Problem:
Used to feed individual components/parts for assembly on industrial production lines such as for medical devices. They are used when a randomly sorted bulk package of small components must be fed (in a particular direction) into another machine one-by-one.
Problems are caused by static charges generated on the parts caused by friction. This can result in static attraction and repulsion of parts that will cause the parts to misalign and potentially blockages.
Solution:
Use of ionising nozzles to neutralise the parts in the vibration bowl feeder.
Pill Packing
Problem:
Cleaning of the web material and ionisation prior to thermoforming is an important step to prevent contamination and product misbehaviour.
Solution:
Use of a non-contact web cleaner to clean and neutralise the web material prior to thermoforming and ionising bars to prevent product misbehaviour during the packaging process.
* All drawings are for illustrative purposes only. The position of the static control and web cleaning solutions most suitable for your process will depend on certain factors of your application.
Web Cleaning Solutions
Meech is a leading Web Cleaning manufacturer with a comprehensive range of four systems. Each system is based on a different cleaning principle, this uniquely allows us to provide our customers with a system best suited for their application. All Meech systems incorporate the latest shockless AC static control bars as standard which is crucial for comprehensive contamination removal. Meech has more than 200 successful web cleaning installations in a range of industries including Packaging, Printing and Converting.
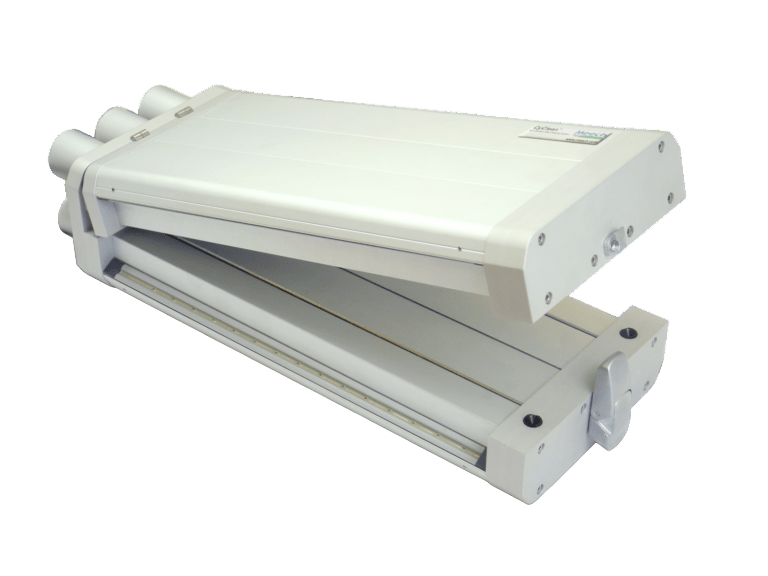
Meech CyClean™ has been designed in response to demand for a compact, high performance, non-contact web cleaner.
Through the application of advanced computational fluid dynamics, CyClean removes and extracts contamination below 1 micron.
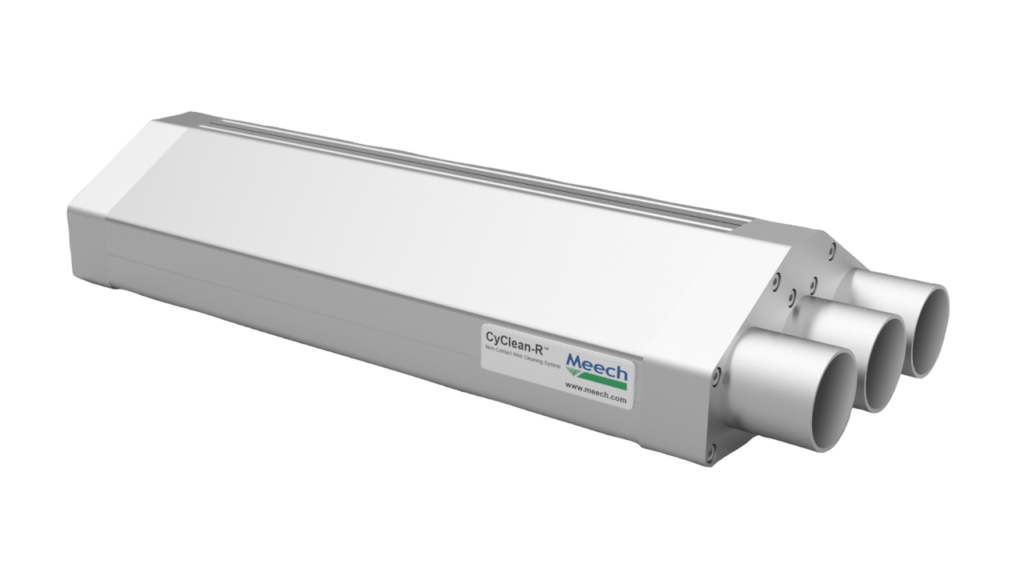
The CyClean-R provides a specialised solution for low-tension web cleaning.
The CyClean-R is designed to be positioned on the roller, where the web tension is at its highest, therefore bypassing the issues of low tension and still delivering excellent surface cleaning.
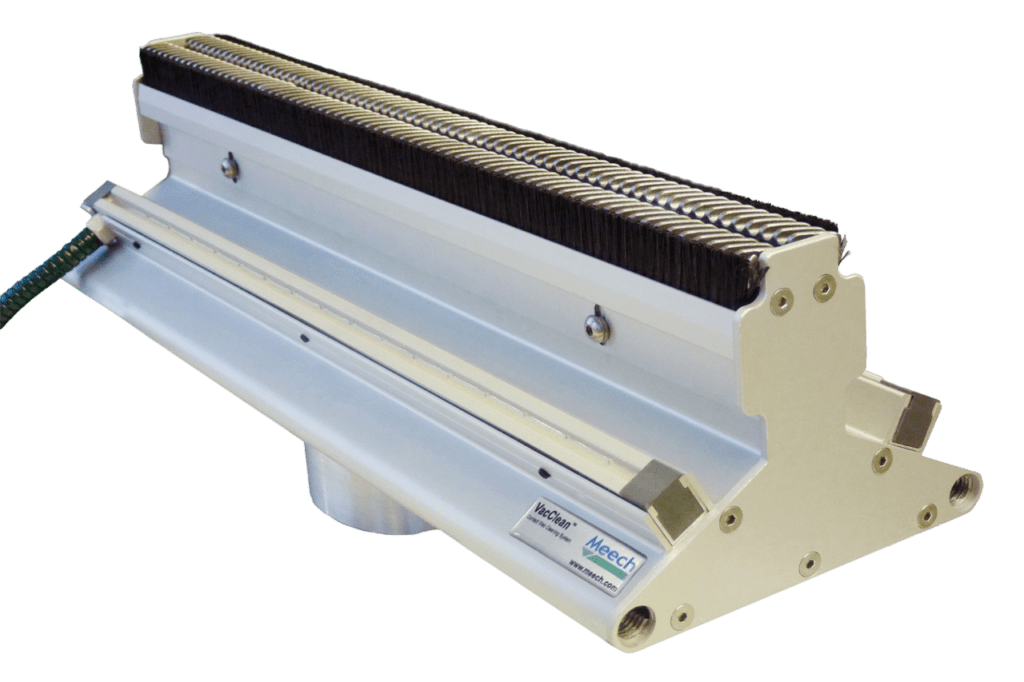
The Meech VacClean™ contact web cleaning system is an evolution of Meech’s successful Tornado system, of which there are hundreds of installations globally. VacClean systems incorporate an enhanced contact cleaning manifold with either an Air Handling Unit (AHU) or vacuum fan unit, depending on the installation environment and web width.
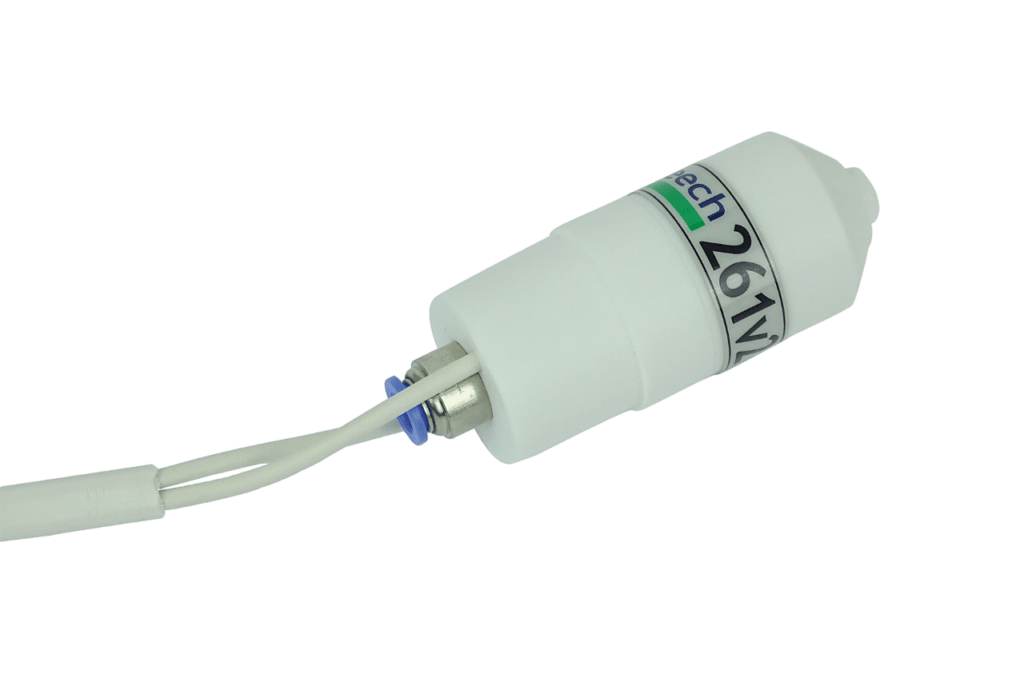
The Model 261v2 Ion Nozzle is a small, robust ionising nozzle and provides an ionised airflow for cleaning and neutralising static charges. It is powered by a Meech Model 233v4 and is suitable for industrial, electronic and cleanroom environments and is quick to install and easy to use.
Static Control Solutions
Meech is a market leader in manufacturing and supplying static control products since the 1960’s; offering a wide range of electrostatic products that provide anti-static and ESD protection and measurement, static generation, electrostatic control and elimination.
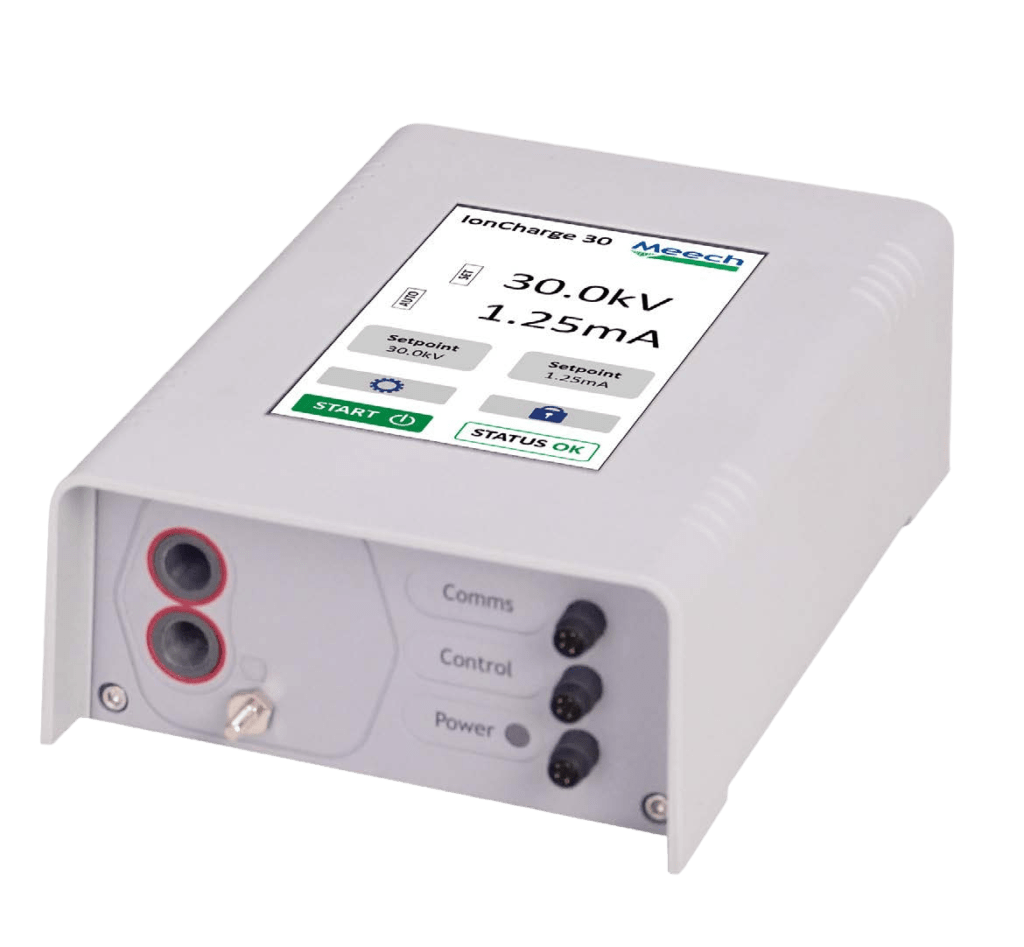
IonCharge30 has 15 watt power output and provides a 0-30kV voltage range. It uses advanced high voltage technology and software for a controlled static charge via our range of static generator bars and pinning heads.
The static charge can be either positive or negative (model dependant) and is used to impart temporary bonding between materials, at least one of which is insulative.
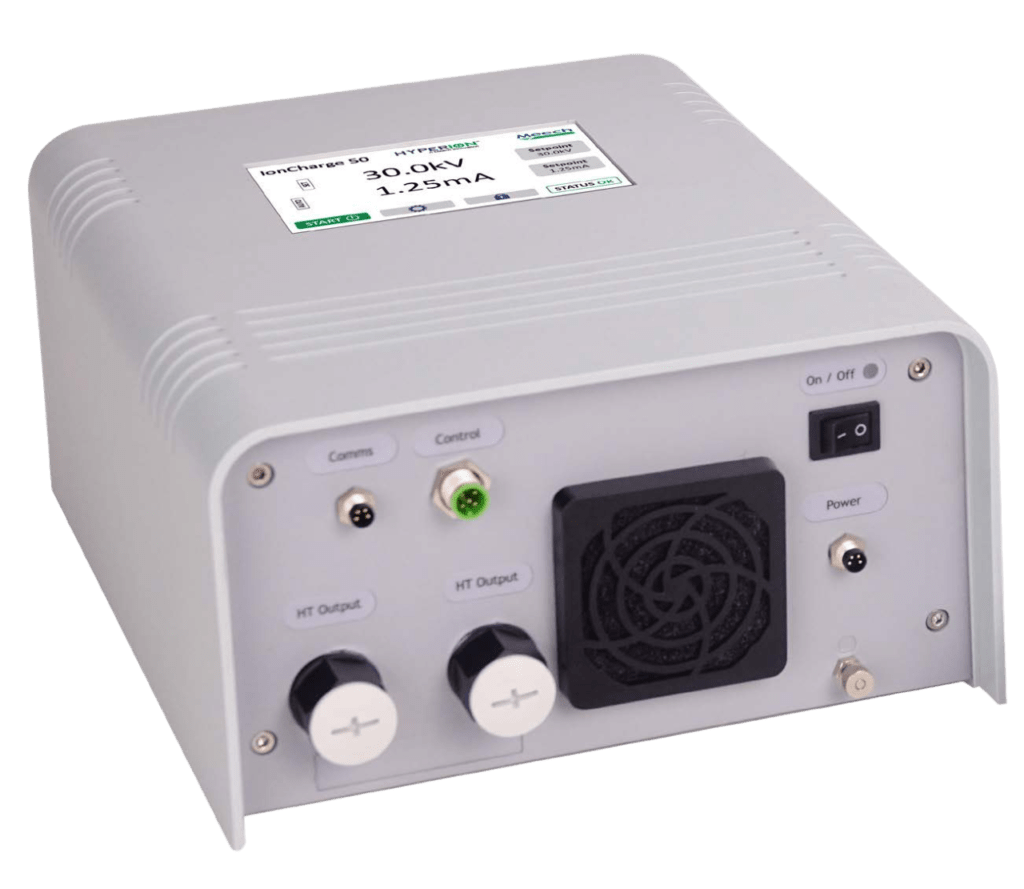
IonCharge50 has a 75W power output and provides a 0-50kV voltage range. It uses advanced high voltage technology and software for a controlled static charge via our range of static generator bars and pinning heads.
The static charge can be either positive or negative (model dependant) and is used to impart temporary bonding between materials, at least one of which is insulative.
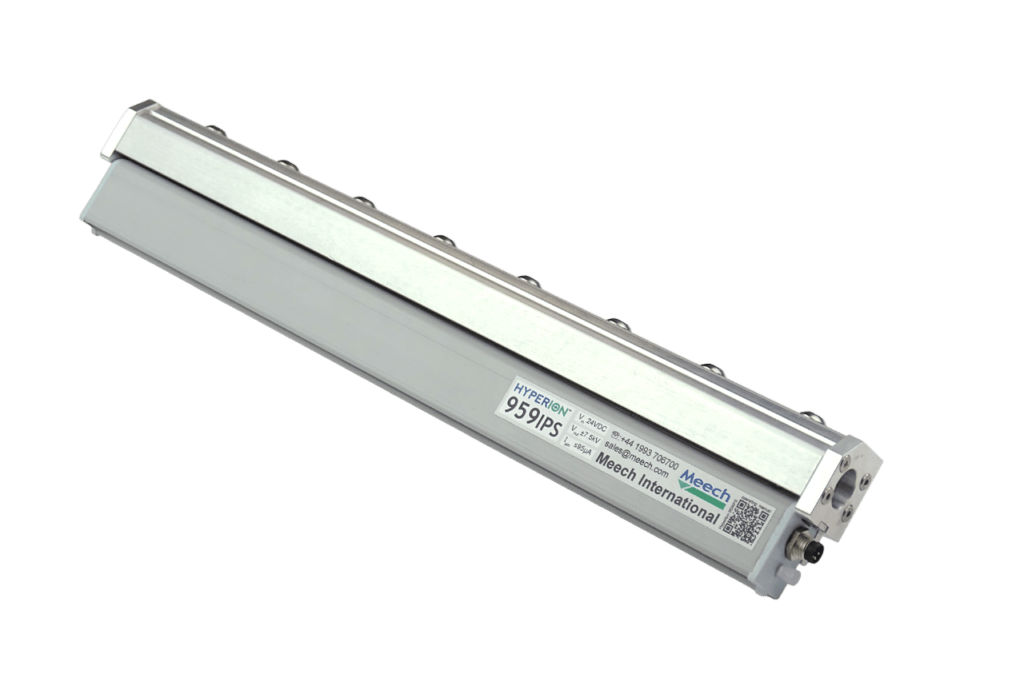
The Hyperion 959IPS ionising air curtain is an extremely versatile product that provides effective static neutralisation and dust removal.
Comprised of a Hyperion 924IPS mounted on a Meech energy saving air curtain it provides a high speed laminar sheet of ionised air.
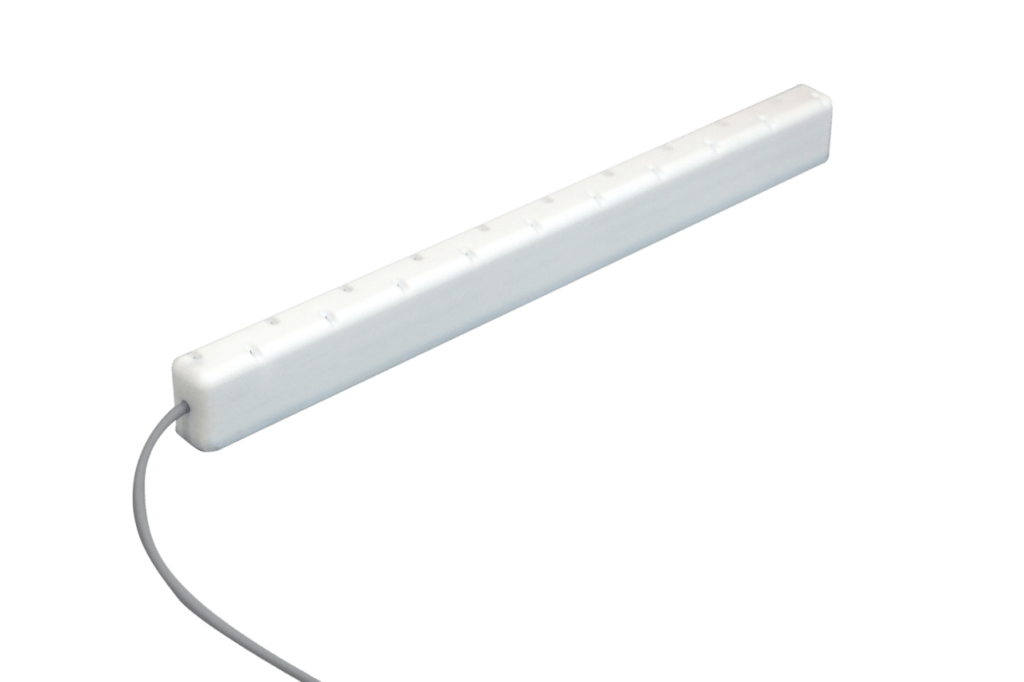
The 314IPS is a short range compact pulsed DC ionising bar specifically designed for use in hygienic applications.
Its PTFE construction is ideally suited to use on Hygienic food and pharmaceutical machinery.
Could we help improve your medical manufacturing process?
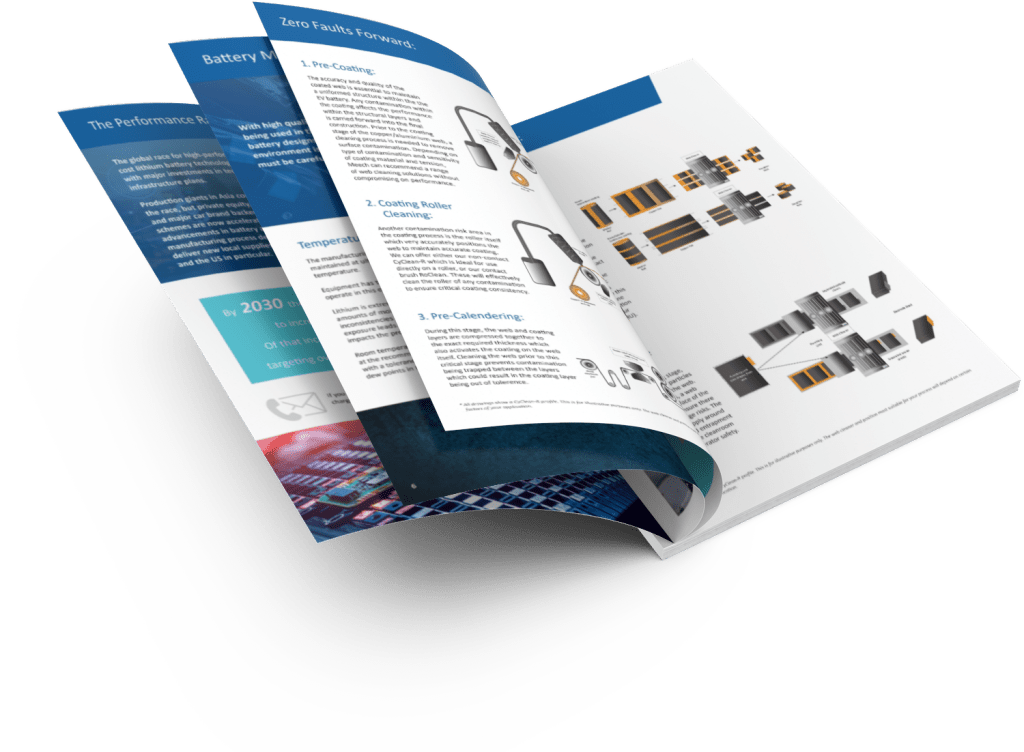