Pharmaceutical
Contamination removal in Pharmaceutical supply production
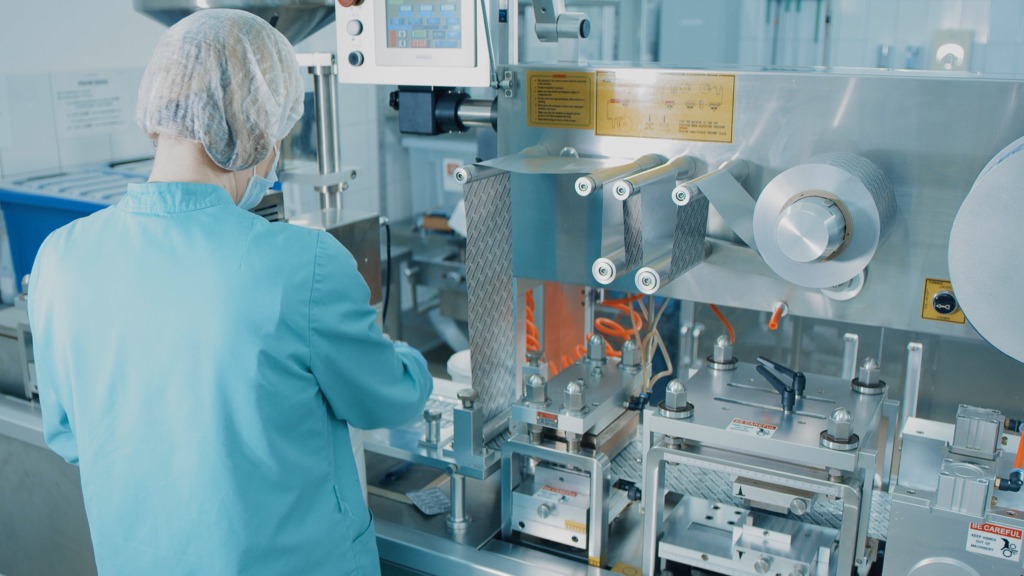
During the production of pharmaceutical supplies, high levels of static charge can lead to issues including production jams, inaccurate weighing, contamination, poor blister pack sealing and even repulsion of the tablets or capsules (leading to empty punnets).
Static charges can cause dust and other airborne contaminants to be attracted to the surface of a moving web, which could lead to costly rejections if untreated.
For instance, static can cause weighing equipment to show inaccurate results, which is significant where exact measurements in dosages are paramount. Therefore, static control is needed to balance the static charges, ensuring that all weighing (down to the milligram) is accurate.
Implementing the correct Static control and web cleaning solution can eliminate static charges, resulting in clean, accurate and contamination free production.
Our Zero Faults Forward Approach
We have identified a number of applications within medical supply manufacturing that are prone to contamination on the line. By applying the right solutions at these points, you make sure there are no weak links to your production chain. We explore these below and demonstrate our solutions…
Medical supply applications
It is critical that static electricity is controlled during the manufacturing of pharmaceutical supplies. Below are some of the main areas affected by static charges during production, and our solutions to remove static charges and other contaminants:
Bowl feeders for tablet or capsules
Tablets being oriented into the right position by bowl feeders for transportation on single line delivery systems can generate charges that cause static attraction or repulsion of those parts.
Solution – The correct positioning of a Pulsed DC ionising bar will ensure effective ionisation and the neutralisation of target area.
Static issues effecting electronic weighing scales
Highly accurate balances are affected by static charges which alter the weight of the sample being weighed causing weighing inaccuracy and risk of contamination of the products being weighed.
Solution – The correct positioning of a Pulsed DC ionising bar will ensure effective ionisation and the neutralisation of target area.
Tablet blister packing
Static charges generated in the thermoformed blister pack filling process can lead to the repulsion of tablets or capsules, product jams, attraction of contaminants and poor blister pack sealing.
Solution – Positioning of a Pulsed DC ionising bar will ensure effective ionisation and the neutralisation of target area.
Powder filling stations
Static charges are generated on the powder as it is delivered into the filling head, which causes the powder to be attracted to the rim of the bottle and the dust is repelled back onto the auger spout.
Solution – By removing the static charges from the container, using an ionising nozzle, the attraction of powder onto the neck of the container is greatly reduced. This also effectively reduces the dust which is repelled back onto the Auger spout.
Bag sealing problems in vertical form fill & seal machines
High static charges are generated when packaging film is fed from a wind off roll. The static charge attracts powder and lightweight dust from the filling products on to the internal film surface. In particular, contaminants get into the seal which prevents effective sealing and is not cosmetically acceptable to the end user/shopper. This prevents proper sealing of the film, resulting in expensive machine down time and scrap product.
Solution – An ionising bar can be positioned prior to the forming tube to eliminate static charges on the film that will become the inside of the tube. Further ionising bars are positioned just before sealing so that any residual static charge on the film is neutralised, preventing dust attraction and allowing full sealing.
* All drawings are for illustrative purposes only. The position of the static control and web cleaning solutions most suitable for your process will depend on certain factors of your application.
Web Cleaning Solutions
Meech is a leading Web Cleaning manufacturer with a comprehensive range of four systems. Each system is based on a different cleaning principle, this uniquely allows us to provide our customers with a system best suited for their application. All Meech systems incorporate the latest shockless AC static control bars as standard which is crucial for comprehensive contamination removal. Meech has more than 200 successful web cleaning installations in a range of industries including Packaging, Printing and Converting.
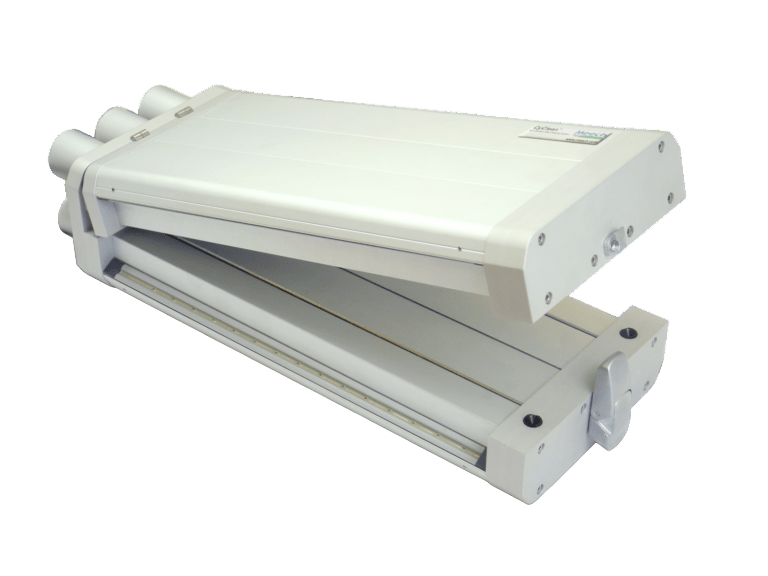
Meech CyClean™ has been designed in response to demand for a compact, high performance, non-contact web cleaner.
Through the application of advanced computational fluid dynamics, CyClean removes and extracts contamination below 1 micron.
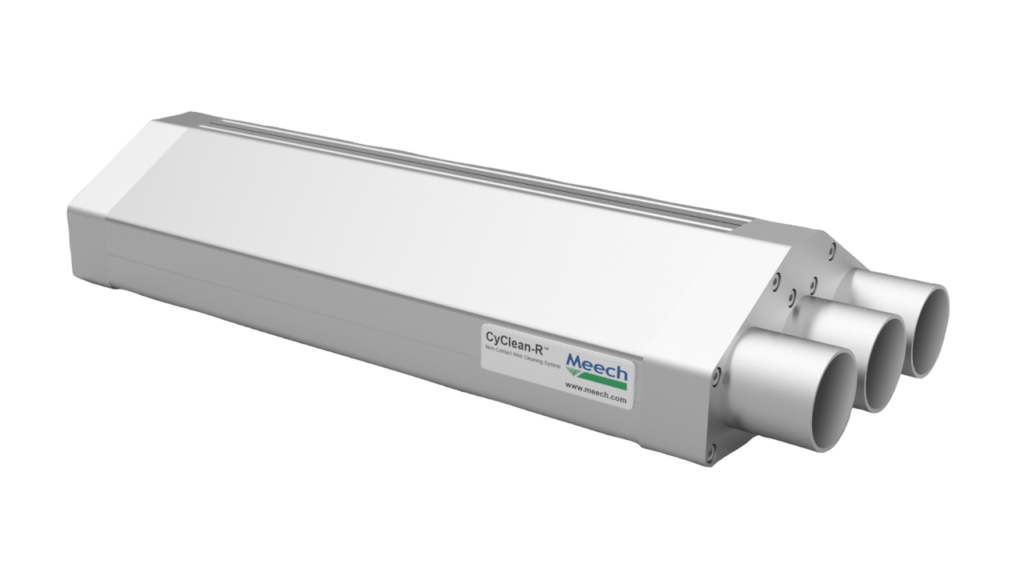
The CyClean-R provides a specialised solution for low-tension web cleaning.
The CyClean-R is designed to be positioned on the roller, where the web tension is at its highest, therefore bypassing the issues of low tension and still delivering excellent surface cleaning.
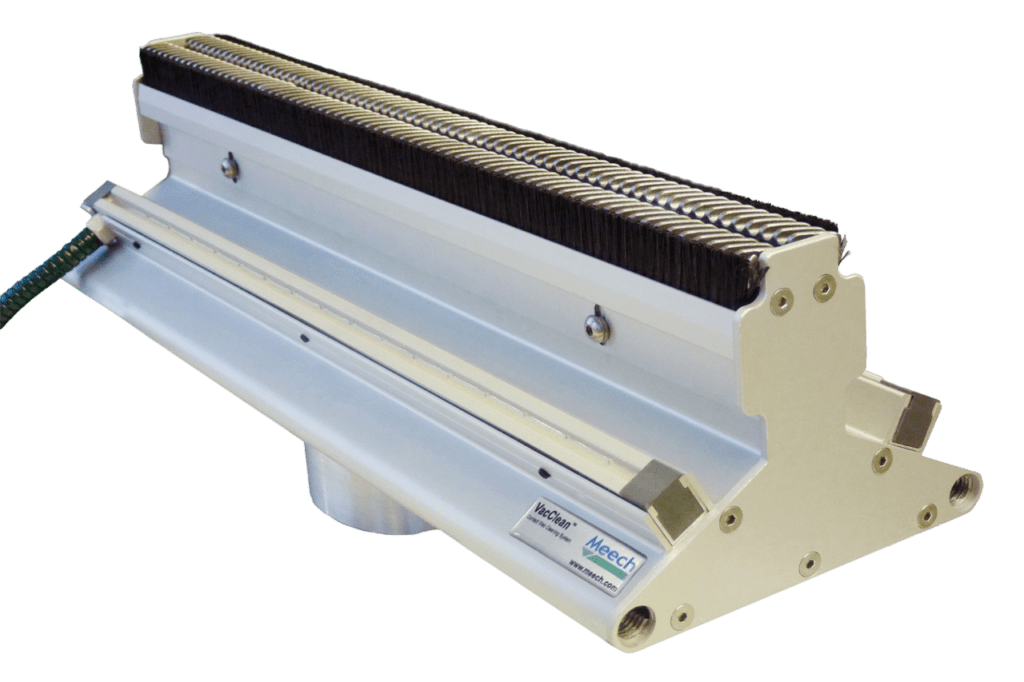
The Meech VacClean™ contact web cleaning system for removal of high levels of unbonded, dry contamination.
Static Control Solutions
Meech is a market leader in manufacturing and supplying static control products since the 1960’s; offering a wide range of electrostatic products that provide anti-static and ESD protection and measurement, static generation, electrostatic control and elimination.
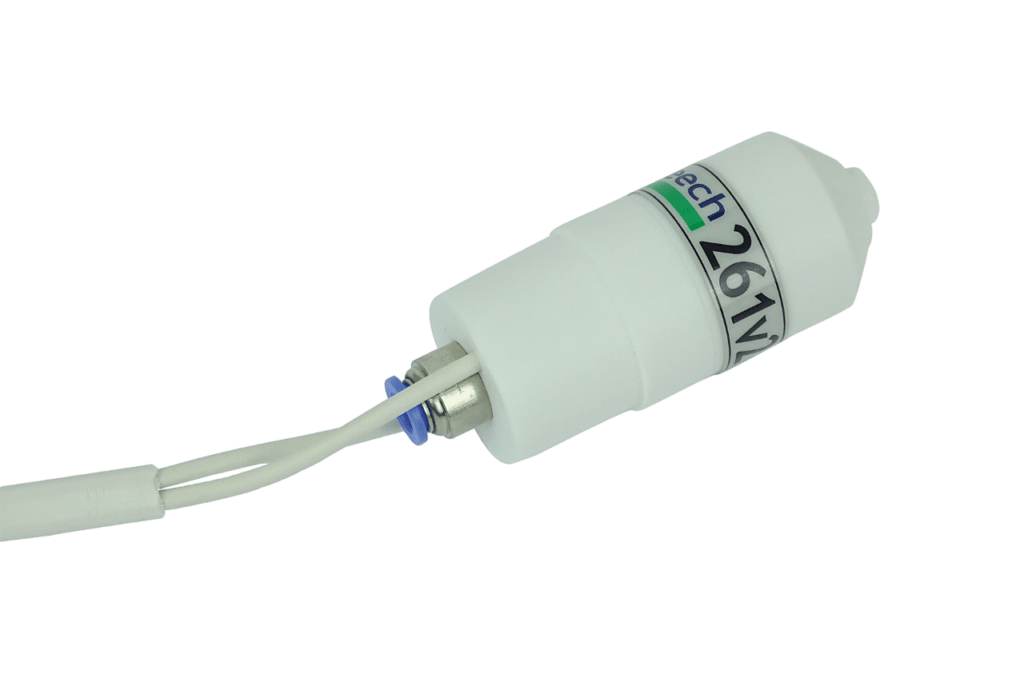
The Model 261v2 Ion Nozzle is a small, robust ionising nozzle and provides an ionised airflow for cleaning and neutralising static charges. It is powered by a Meech Model 233v4 and is suitable for industrial, electronic and cleanroom environments and is quick to install and easy to use.
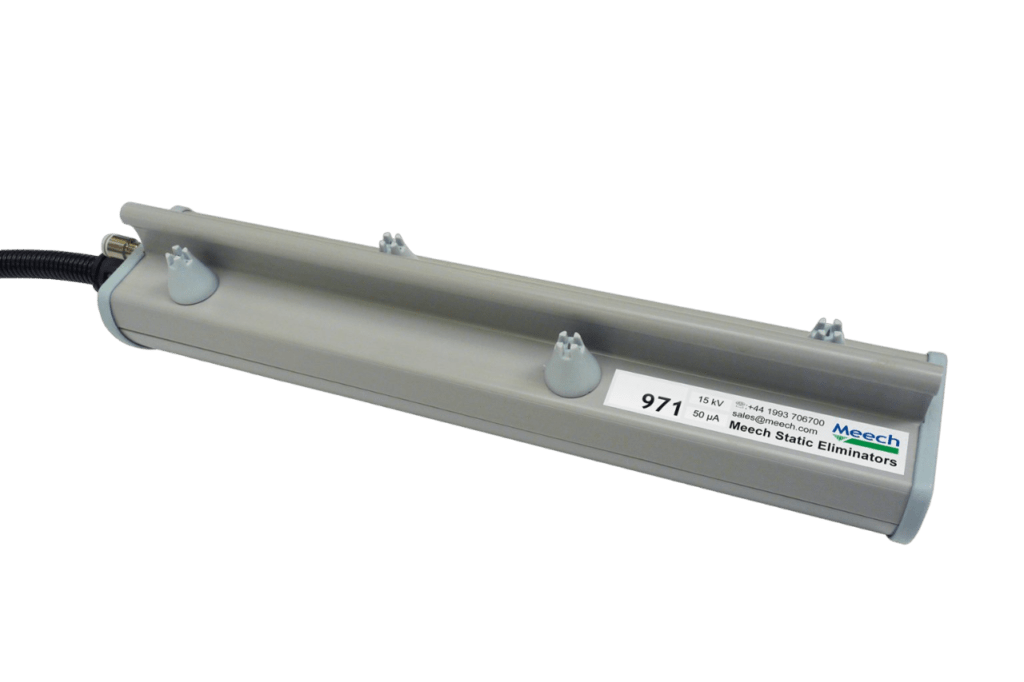
The 971 Pulsed DC bar delivers powerful, long range ionisation to control static electricity on a wide range of printing, converting and process machinery.
Using reliable Pulsed DC technology, the 971 delivers industry leading ionisation performance. For more demanding applications, the integrated air-boost can be used to increase its capability at distance. Meech’s ever reliable titanium emitter system gives extra-long service life. Resistive coupling makes the bar shockless to touch and safe for operators to handle.
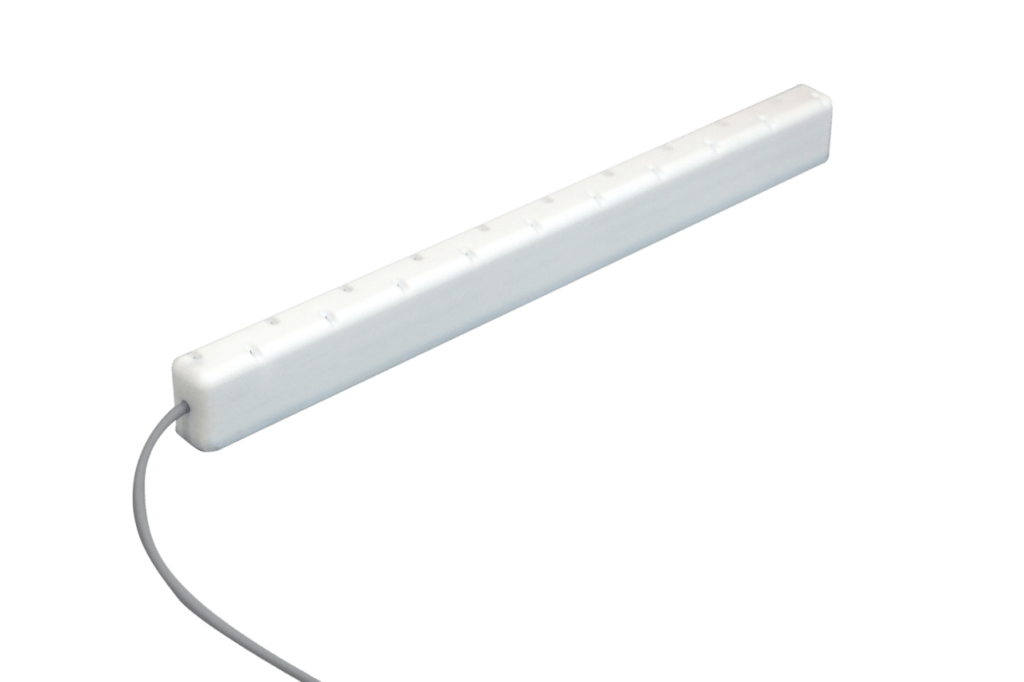
The 314IPS is a short range compact pulsed DC ionising bar specifically designed for use in hygienic applications.
Its PTFE construction is ideally suited to use on Hygienic food and pharmaceutical machinery.
Could we help improve your pharmaceutical manufacturing process?
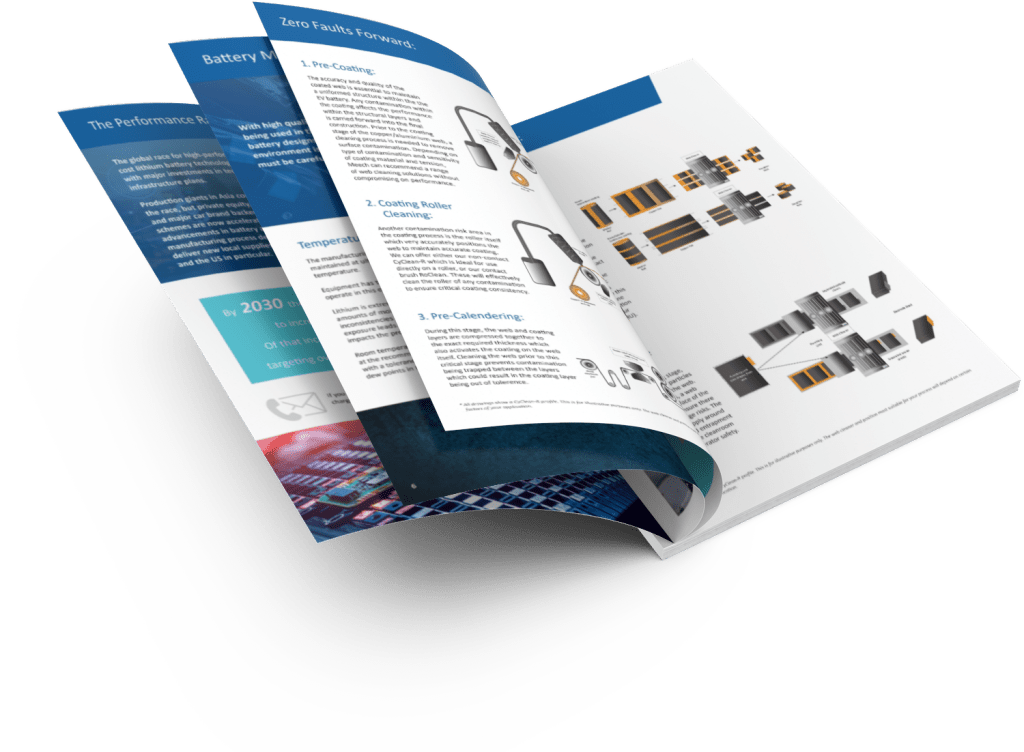