bateria
Usuwanie zanieczyszczeń przy produkcji ogniw akumulatorowych
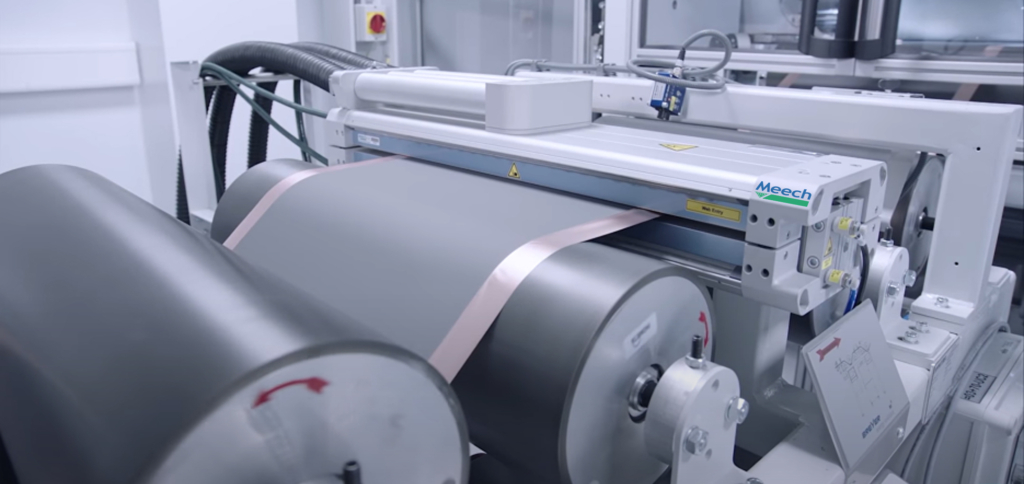
Rozwój rynku pojazdów elektrycznych w ostatnich latach skłonił producentów do szybkiego opracowywania i produkcji akumulatorów litowo-jonowych, aby napędzać wzrost sprzedaży. Wraz z otwieraniem gigafabryk na całym świecie, aby zaspokoić popyt, rośnie konkurencja, a jakość jest najważniejsza.
W obliczu szybkiego rozwoju technologii producenci akumulatorów pragną stworzyć akumulator, który mógłby konkurować z pojazdami napędzanymi benzyną lub olejem napędowym, aby zapewnić imponujący zasięg i osiągi.
Aby to osiągnąć, każdy etap procesu produkcji baterii musi zostać szczegółowo przeanalizowany, aby uzyskać najlepsze wyniki.
Działanie w środowisku produkcyjnym baterii litowych:
Jednym z kluczowych obszarów zainteresowania przy produkcji akumulatorów do pojazdów elektrycznych są warunki środowiska produkcyjnego. Od surowców początkowych po montaż ogniw, warunki produkcji muszą być ściśle kontrolowane. Stwarza to wyzwania zarówno dla producentów sprzętu, jak i operatorów. Istnieją 3 główne obszary wymagające krytycznego rozważenia:
Lit metaliczny jest niezwykle wrażliwy na nawet najmniejsze ilości wilgoci w powietrzu i wahania temperatury podczas produkcji.
Najmniejsze narażenie prowadzi do zmniejszenia wydajności i wpływa na skrócenie żywotności akumulatorów litowo-jonowych.
Temperaturę w pomieszczeniu należy utrzymywać na zalecanym poziomie, około 25°C (77°F), z tolerancją +/(-) 2°C (36°F) wraz z niskimi punktami rosy w zakresie <1%.
Szybkość wymiany powietrza w pomieszczeniu produkcyjnym powinna wynosić od 20 do 50 wymian powietrza na godzinę, przy jednoczesnym zachowaniu minimalnego dopływu świeżego powietrza w celu zapewnienia dodatniego ciśnienia w pomieszczeniu i niezbędnej wentylacji dla operatorów.
Zanieczyszczenia dowolnego rodzaju materiałów akumulatora lub uzwojenia ogniwa mogą prowadzić do bezpośrednich lub łagodnych niedoborów prądu – prowadzących do odrzutów na końcu linii lub niskiego zasięgu akumulatora.
Prawdopodobnie warunki pomieszczenia czystego spełniające normę ISO 8 (lub wyższą) ze szczególnym naciskiem na usuwanie zanieczyszczeń ze środowiska i personelu.
Oczywiście zanieczyszczenia nie zawsze można usunąć, dlatego nadal istnieje ryzyko zanieczyszczenia i wpływu na wydajność produkcji.
Problemy i wolne cząstki mogą również powstawać w procesach odwijania/nawijania, przezbrojeń, powlekania, kalandrowania, cięcia wzdłużnego, tłoczenia, cięcia laserowego i innych.
Wszystkie one mogą przedostać się do warstw folii anoda/katoda/separator.
Niektóre zanieczyszczenia będą suchymi, wolnymi i niezwiązanymi cząstkami, podczas gdy inne będą wilgotnymi lub związanymi zanieczyszczeniami, które są trudniejsze do usunięcia.
Innym obszarem ryzyka są toksyczne zanieczyszczenia z materiałów powłokowych przenoszonych na walce, ciętych, nawijanych i walcowanych – mogą one przedostać się do powietrza i stanowić zagrożenie dla dróg oddechowych operatora.
Ładunki statyczne w środowisku produkcyjnym mogą prowadzić do szeregu problemów:
Elementy akumulatorów pojazdów elektrycznych są bardzo wrażliwe na ładunki statyczne – w trakcie procesu elementy muszą być rozładowywane.
Niekontrolowane ładunki statyczne będą również wpływać na przepływ materiału i powodować nieprawidłowe zachowanie lub awarię materiału.
W przypadku niekontrolowanego wyładowania statycznego (iskry) spowodują powierzchniowe oparzenia dendrytyczne, wpływające na właściwości dielektryczne folii separatora – prowadząc do niespójnego ładowania i rozładowania oraz awarii produktu.
Ładunki statyczne generowane na materiałach izolacyjnych, takich jak folia oddzielająca, również przyciągają cząstki, zwiększając ryzyko zanieczyszczenia.
Nasze podejście do przyszłości bez usterek
Zidentyfikowaliśmy kilka etapów procesu produkcji akumulatorów, które są podatne na zanieczyszczenie na linii. Stosując odpowiednie rozwiązania w tych punktach, masz pewność, że nie ma słabych ogniw w Twoim łańcuchu produkcyjnym. Omówimy je poniżej i zademonstrujemy nasze rozwiązania…
Przed etapem powlekania wstęgi miedziano-aluminiowej zalecamy użycie środka do czyszczenia wstęgi na podłożu w celu usunięcia wszelkich zanieczyszczeń powierzchniowych, które mogą mieć wpływ na grubość i jakość powlekanej wstęgi. Usuwając zanieczyszczenia na tym etapie, można mieć pewność, że w warstwach nie zostaną uwięzione żadne niepożądane cząstki, co nie będzie miało wpływu na wydajność akumulatora w przyszłości.
Aby uniknąć odciskania jakichkolwiek zanieczyszczeń z samego wałka na powłoce podłoża, sugerujemy użycie naszego CyClean-R, który idealnie nadaje się do stosowania na wałku, lub naszego kontaktowego RoClean. To skutecznie oczyści wałek z wszelkich zanieczyszczeń, aby zapobiec przedostawaniu się materiału do wstęgi.
Na tym etapie wstęga i warstwy powłoki są ściskane razem do odpowiedniej grubości, aktywując powłokę na samej wstędze. Czyszczenie wstęgi przed tym krytycznym etapem zapobiega uwięzieniu zanieczyszczeń pomiędzy samymi warstwami.
Proces cięcia może spowodować powstanie dużej ilości zanieczyszczeń, które mogą zanieczyścić powlekane podłoże wstęgowe. Zastosowanie na tym etapie środka czyszczącego wstęgę gwarantuje, że cząstki zostaną usunięte z powierzchni wstęgi i odfiltrowane z atmosfery roboczej, aby uniknąć ponownego zanieczyszczenia. Przy tak wysokim ryzyku zanieczyszczenia na tym etapie, czyszczenie jest koniecznością, aby uniknąć ryzyka przyszłych niedoborów prądu i kosztownych odrzutów.
Podobnie jak w przypadku etapu po rozcinaniu, podczas cięcia elektrodą cząstki i zanieczyszczenia mogą zanieczyścić wstęgę. Aby tego uniknąć, czyszczenie wstęgi na tym etapie oczyści powierzchnię podłoża, prowadząc do czystych i przejrzystych warstw oddzielających.
W procesie nawijania proponujemy szereg rozwiązań zapewniających najlepsze rezultaty. Przed nawinięciem zaleca się oczyszczenie powierzchni podłoża, aby nie dopuścić do zatrzymania zanieczyszczeń w zwoju folii akumulatora. Aby przezwyciężyć problemy statyczne, które mogą być zarówno niebezpieczne, jak i wyjątkowo szkodliwe dla wydajności akumulatora, należy również wprowadzić skuteczną kontrolę statyczną. Zneutralizuje to wszelkie ładunki elektrostatyczne powstałe w wyniku procesu nawijania.
* Wszystkie rysunki przedstawiają profil CyClean-R. Służy to wyłącznie celom ilustracyjnym. Wybór środka czyszczącego wstęgę i jego pozycja najbardziej odpowiednia dla danego procesu będzie zależeć od pewnych czynników związanych z aplikacją.
Rozwiązania do czyszczenia sieci
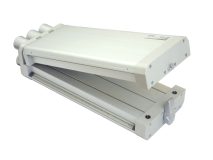
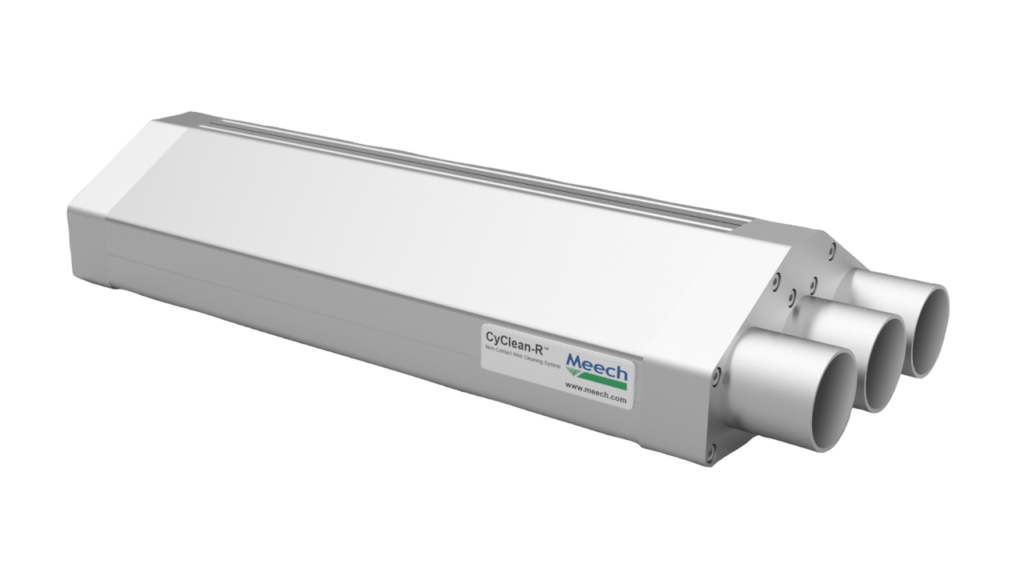
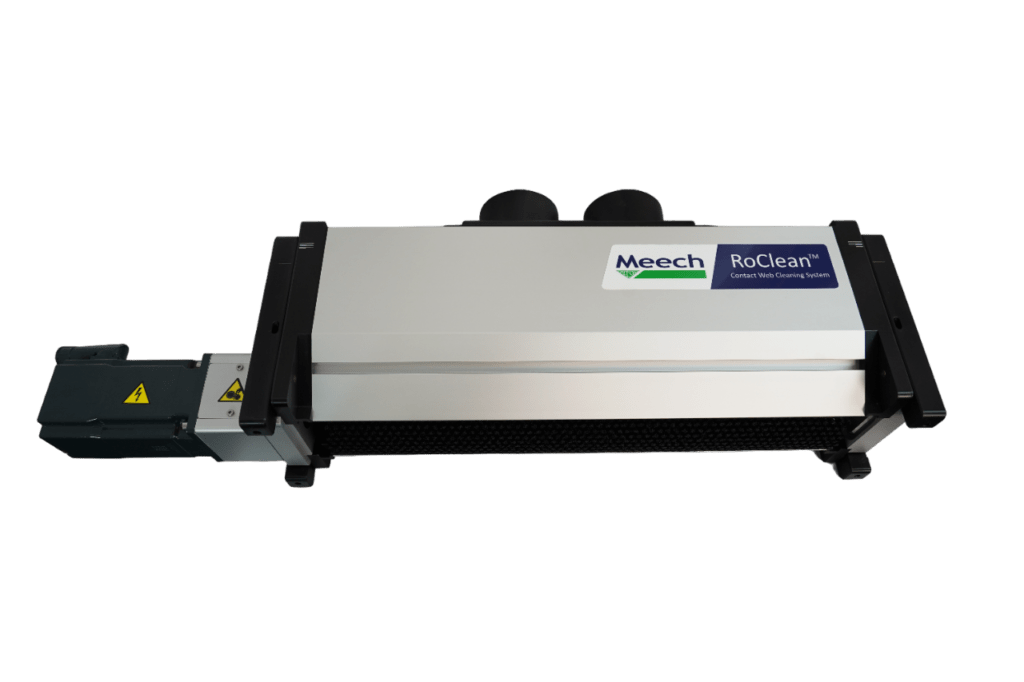
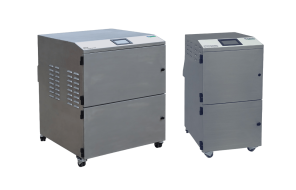
Meech CyClean™ został zaprojektowany w odpowiedzi na zapotrzebowanie na kompaktowy, wydajny, bezdotykowy środek czyszczący do sieci.
Dzięki zastosowaniu zaawansowanej obliczeniowej dynamiki płynów CyClean usuwa i ekstrahuje zanieczyszczenia poniżej 1 mikrona.
CyClean-R to specjalistyczne rozwiązanie do czyszczenia wstęgi przy niskim napięciu.
Urządzenie CyClean-R zaprojektowano tak, aby można je było umieścić na wałku, gdzie napięcie wstęgi jest największe, co pozwala uniknąć problemów związanych z niskim napięciem i nadal zapewnia doskonałe czyszczenie powierzchni.
RoClean to najnowszy środek do czyszczenia wstęgi kontaktowej, zapewniający doskonałe rezultaty czyszczenia powierzchni dla przemysłu produkującego folię akumulatorową.
RoClean skutecznie czyści powierzchnię wstęgi dzięki zastosowaniu zarówno kontroli statycznej, jak i wydajnej szczotki walcowej z włosiem.
Urządzenia czyszczące Meech są dostarczane z centralami wentylacyjnymi Meech (AHU), które zapewniają utrzymanie równowagi powietrza i doskonałą kontrolę dokładności ciśnienia i podciśnienia powietrza. Są to kompaktowe jednostki o specyfikacji przemysłowej, które można również monitorować za pomocą sterownika PLC.
Dla środowiska akumulatorowego opracowano nową opcję centrali, aby usprawnić wychwytywanie toksycznych zanieczyszczeń i bezpieczne usuwanie filtra przez operatora.
Rozwiązania kontroli statycznej
Zasilany napięciem 24 V DC Hyperion 924IPS jest najbardziej kompaktową listwą impulsową DC dostępną na rynku.
Model 924IPS jest wyposażony w technologię monitorowania prądu jonowego (ICM) firmy Meech, która zapewnia utrzymanie wydajności dzięki lokalnym i zdalnym alertom, gdy listwa wymaga czyszczenia.
Nasz system sprzężenia zwrotnego w zamkniętej pętli wykorzystuje regulowaną równowagę impulsowych systemów jonizujących DC.
System składa się z Hyperion SmartControl i maksymalnie 5 produktów jonizujących Hyperion zapewniających sprzężenie zwrotne w zamkniętej pętli. Po podłączeniu do czujnika SmartControl mierzy napięcie w sieci za listwą jonizującą.
Pomiar ten może zostać przekazany z powrotem do produktu jonizującego, który automatycznie dostosowuje równowagę mocy wyjściowej, aby uzyskać całkowicie neutralną wstęgę. Jest to proces ciągły, w ramach którego stale dokonuje się pomiarów i regulacji, aby w każdym momencie uzyskać najlepszą kontrolę statyczną.
Lokalizator statyczny model 983v2 zapewnia wyraźne wskazanie ładunków elektrostatycznych na materiałach. Jest przeznaczony do ogólnego użytku przemysłowego i posiada szeroki zakres pomiarowy +/-200kV, mierzony w odległości 150mm.
Urządzenie 983v2 może pracować w trybie „Ciągły” lub „Zatrzymanie wartości szczytowej”, aby rejestrować odpowiednio zmiany poziomu naładowania lub najwyższy wykryty ładunek. Nadaje się do zapewnienia dobrego wskazania poziomu ładunku statycznego do użytku przez inżynierów zajmujących się produkcją, konserwacją, inspekcją i jakością. Model 983v2 można stosować na każdym materiale, gdzie ładunki statyczne mogą stanowić problem.
SmartControl Touch to najnowsza innowacja firmy Meech zaprojektowana w celu zaspokojenia potrzeb nowoczesnych, zautomatyzowanych gałęzi przemysłu i rozwoju Przemysłu 4.0 w celu osiągnięcia maksymalnej produktywności i jakości wydruku.
SmartControl Touch pozwala użytkownikowi monitorować, kontrolować i regulować wydajność wielu podłączonych prętów jonizujących i czujników Hyperion za pomocą zintegrowanego ekranu dotykowego lub zdalnie.
Czy możemy pomóc ulepszyć proces produkcji baterii w Twojej firmie?
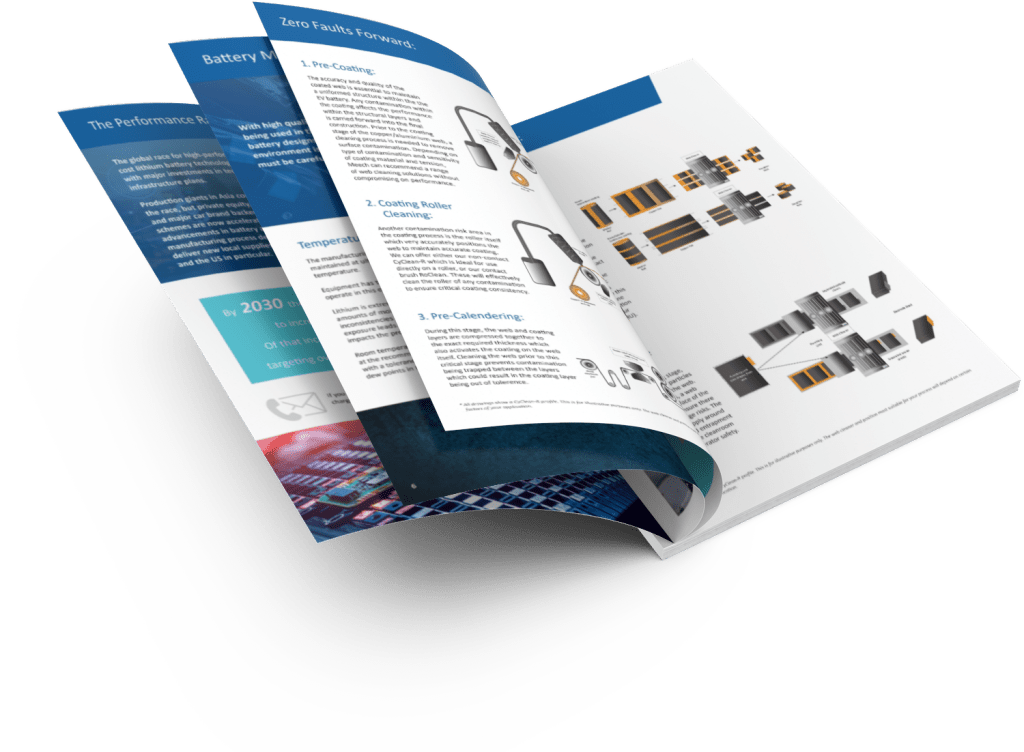