Battery
Contamination removal in battery cell production
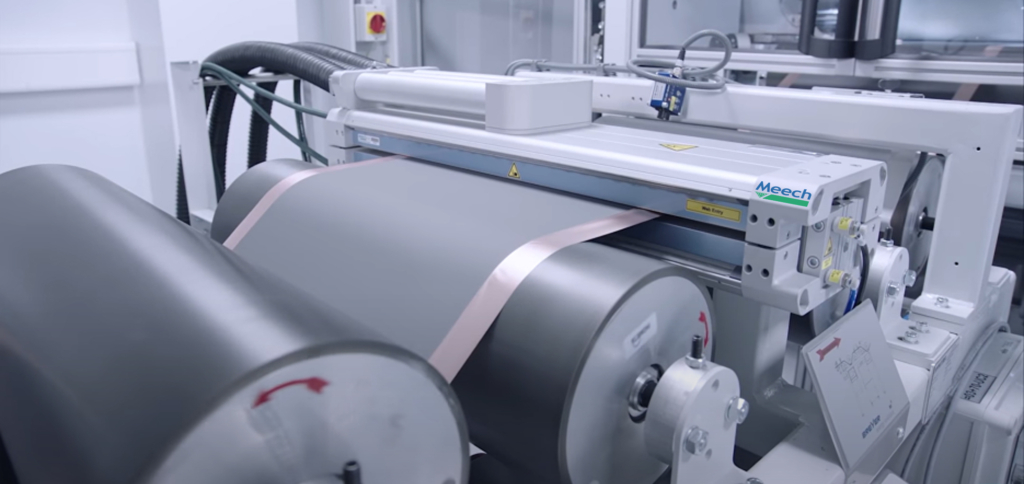
The rise of the EV market in recent years has led manufacturers to rapidly develop and manufacture lithium-ion batteries to fuel the boom in sales. With giga-factories opening across the globe to meet the demand, competition is growing and quality is paramount.
With technologies developing at speed, battery manufacturers are looking to create a battery which rivals petrol or diesel-fed vehicles, in order to deliver impressive mileage range and performance.
In order to achieve this, every stage of the battery manufacturing process must be meticulously analysed in order to produce the best results.
Operating in the lithium battery manufacturing environment:
One of the critical focus areas for EV battery production is the manufacturing environment conditions. From initial raw materials to cell assembly the manufacturing conditions must be tightly controlled. This creates challenges for equipment manufacturers and operators alike. There are 3 main areas of critical consideration:
Lithium metal is extremely sensitive to even the smallest amounts of moisture in air and temperature inconsistencies in production.
The slightest exposure leads to reduced performance and impacts on reduced product life of Lithium-ion batteries.
Room temperature should be maintained at recommended levels, around 25°C (77°F), with tolerance of +/(-) 2°C (36°F) along with low dew points in the range of <1%.
The air change rate in the production room should be 20 to 50 air changes per hour while maintaining minimum fresh air introduction for positive room pressure and essential ventilation for operators.
Contamination of any type into the battery materials or wound into the cell can lead to direct or soft electrical shortages – leading to end of line rejects or low battery range performance.
ISO 8 cleanroom condition (or higher) is likely with major focus on contamination removal in the environment as well as on personnel.
Of course, contamination cannot always be removed and so there is still a risk of contamination and an impact on production yields.
Problems and free particles can also be created within the processes of unwinding/winding, changeovers, coating, calendaring, slitting, stamping, laser cutting and more.
All of these have potential to find their way into the anode/cathode/separator film layers.
Some contamination will be dry, free, unbound particles, while others will be moist, or bound contamination which is more difficult to remove.
Another risk area is toxic contamination from the coating materials as they are transferred over rollers, cut, wound and rolled – this can dissipate into the air and become a breathing hazard for the operator.
Static charges within the manufacturing environment can lead to a number of problems:
EV battery components are very sensitive to static charges – components must be uncharged within the process.
Uncontrolled static charges will also affect the material flow and will cause material misbehaviour or failure.
If uncontrolled, static discharges (sparks) will create surface dendritic burns affecting the dielectric properties of the separator film – leading to inconsistent charge and discharge behaviours and product failure.
Static charges generated on insulative materials such as the separator film also attract particles adding to contamination risk problems.
Our Zero Faults Forward Approach
We have identified a number of stages during the battery manufacturing process that are prone to contamination on the line. By applying the right solutions at these points, you make sure there are no weak links to your production chain. We explore these below and demonstrate our solutions…
Prior to the coating stage of the copper/aluminium web, we recommend the use of a web cleaner on the substrate to remove any surface contamination that may impact the thickness and quality of the coated web. By removing the contamination at this stage, it ensure no unwanted particles are trapped within the layers, affecting the battery performance down the line.
To avoid the imprinting of any contamination from the roller itself to the substrate coating we suggest the use of either our CyClean-R which is ideal for use on a roller, or our contact RoClean. This will effectively clean the roller of any contamination to ensure there is no transmission to the web.
During this stage, the web and coating layers are compressed together to the correct thickness, activating the coating on the web itself. Cleaning the web prior to this critical stage prevents contamination being trapped between the layers themselves.
The slitting process can cause a lot of debris which can contaminate the coated web substrate. The use of a web cleaner at this stage ensures that the particles are removed from the surface of the web and filtered away from the operating atmosphere to avoid re-contamination. With such a high risk of contamination at this stage, cleaning is imperative to avoid the risk of future electrical shortages and expensive rejects.
Similar to the post-slitting stage, during electrode cutting, particles and debris can contaminate the web. In order to avoid this, web cleaning at this stage will clean the surface of the substrate, leading to clean and clear separation layers.
At the winding process we suggest a number of solutions for the best results. Prior to winding, surface cleaning of the substrate is recommended to not trap contamination within the battery film wind. To overcome static issues, which can be both dangerous and extremely detrimental to the battery performance, effective static control should also be introduced. This will neutralise any static charges caused by the winding process.
* All drawings show a CyClean-R profile. This is for illustrative purposes only. The web cleaner and position most suitable for your process will depend on certain factors of your application.
Web Cleaning Solutions
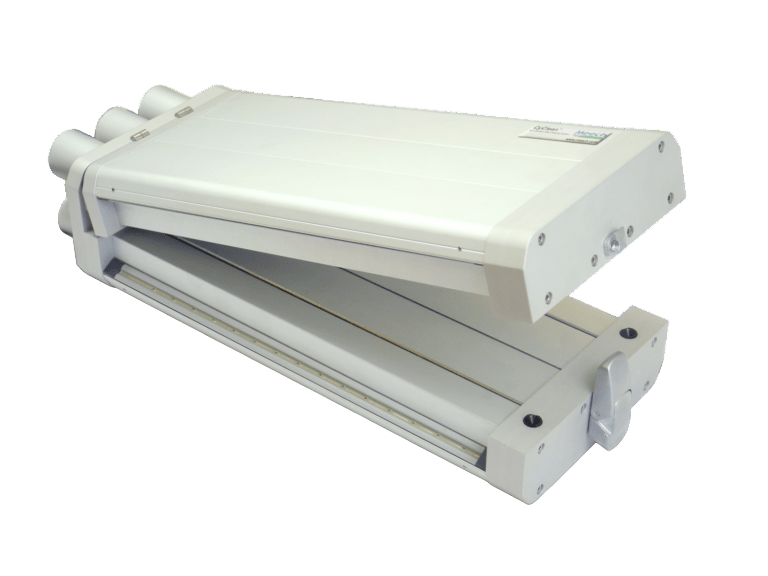
Meech CyClean™ has been designed in response to demand for a compact, high performance, non-contact web cleaner.
Through the application of advanced computational fluid dynamics, CyClean removes and extracts contamination below 1 micron.
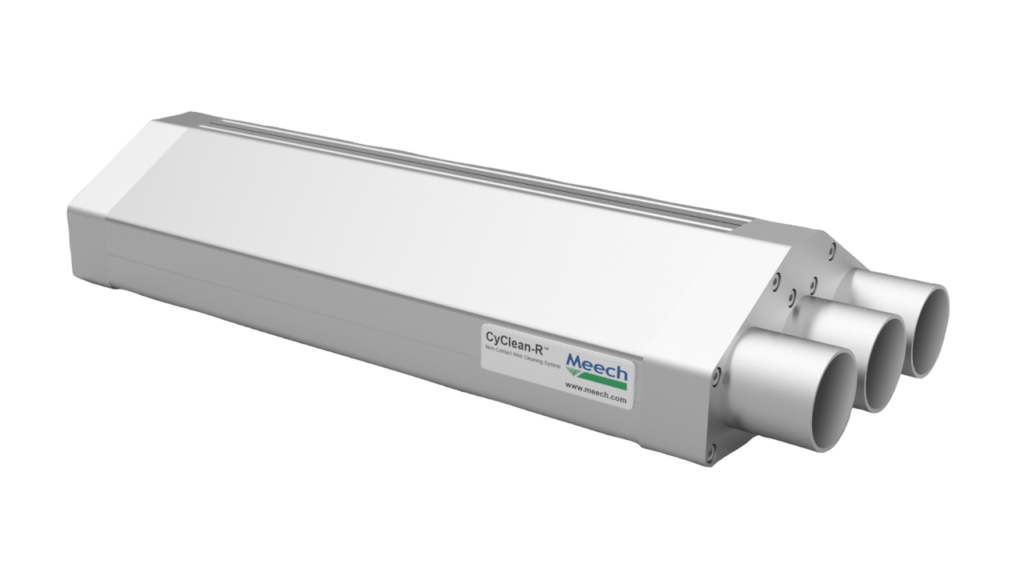
The CyClean-R provides a specialised solution for low-tension web cleaning.
The CyClean-R is designed to be positioned on the roller, where the web tension is at its highest, therefore bypassing the issues of low tension and still delivering excellent surface cleaning.
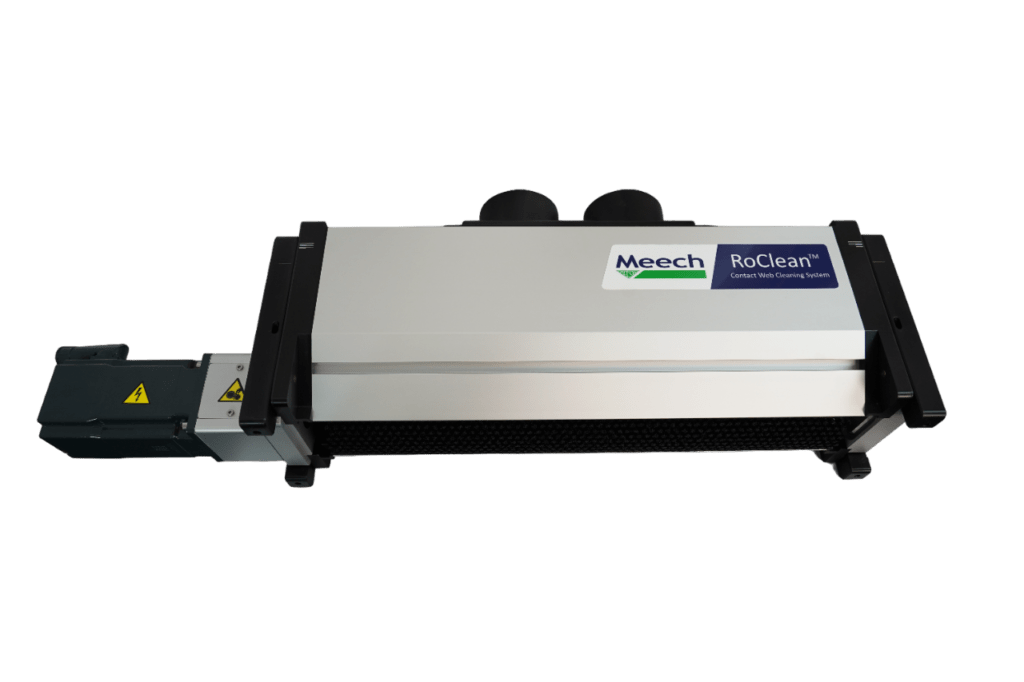
RoClean is the latest contact web cleaner, delivering excellent surface cleaning results for the battery film manufacturing industry.
RoClean effectively cleans the web surface through the use of both static control and an efficient bristle roller brush.
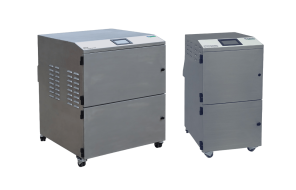
Meech web cleaners are supplied with Meech Air Handling Units (AHUs) to ensure air balance is maintained to perfectly control accuracy of air pressure and vacuum. These are compact, industrial specification units and can also be performance monitored via PLC control.
For the battery environment a new AHU option has been developed to enhance toxic contamination waste entrapment and safe filter removal by the operator.
Static Control Solutions
Powered by 24V DC the Hyperion 924IPS is the most compact pulsed DC bar available on the market.
The 924IPS features Meech’s Ion Current Monitoring (ICM) technology, this ensures performance is maintained with local and remote alerts when the bar needs cleaning.
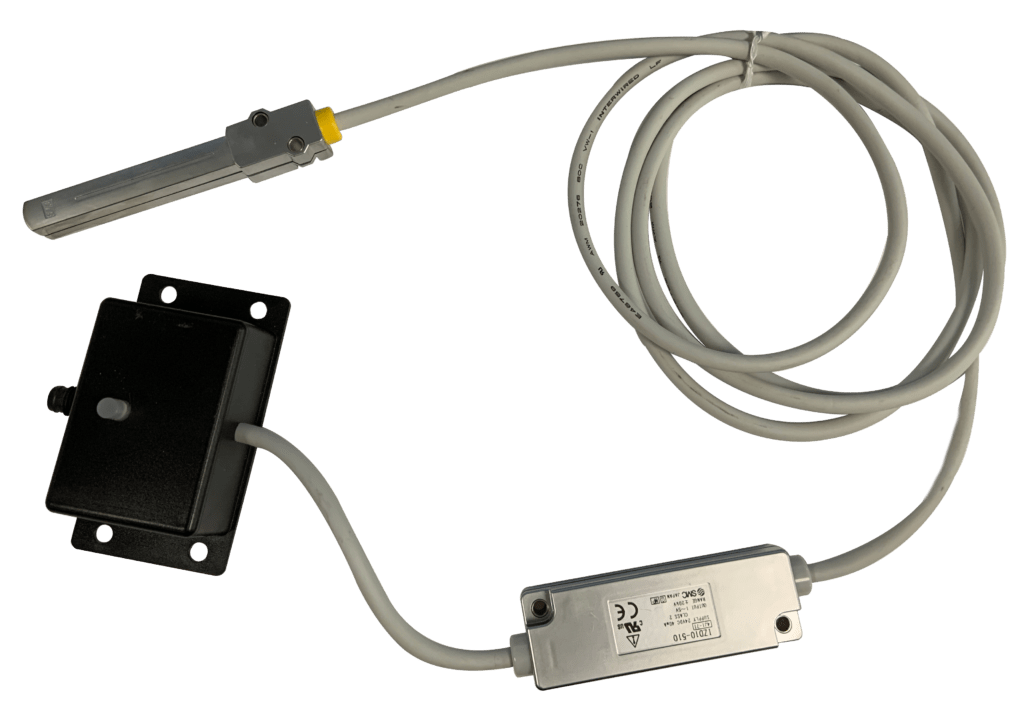
Our closed-loop feedback system takes advantage of the adjustable balance of pulsed DC ionising systems.
The system comprises a Hyperion SmartControl and up to 5 Hyperion ionising products for closed-loop feedback. Once connected to the SmartControl sensor, measures the voltage on the web downstream of the ionising bar.
This measurement can be fed back to the ionising product which automatically adjusts the balance of the output to achieve a completely neutral web. This is a continuous process that constantly measures and adjusts to achieve the very best static control at all times.
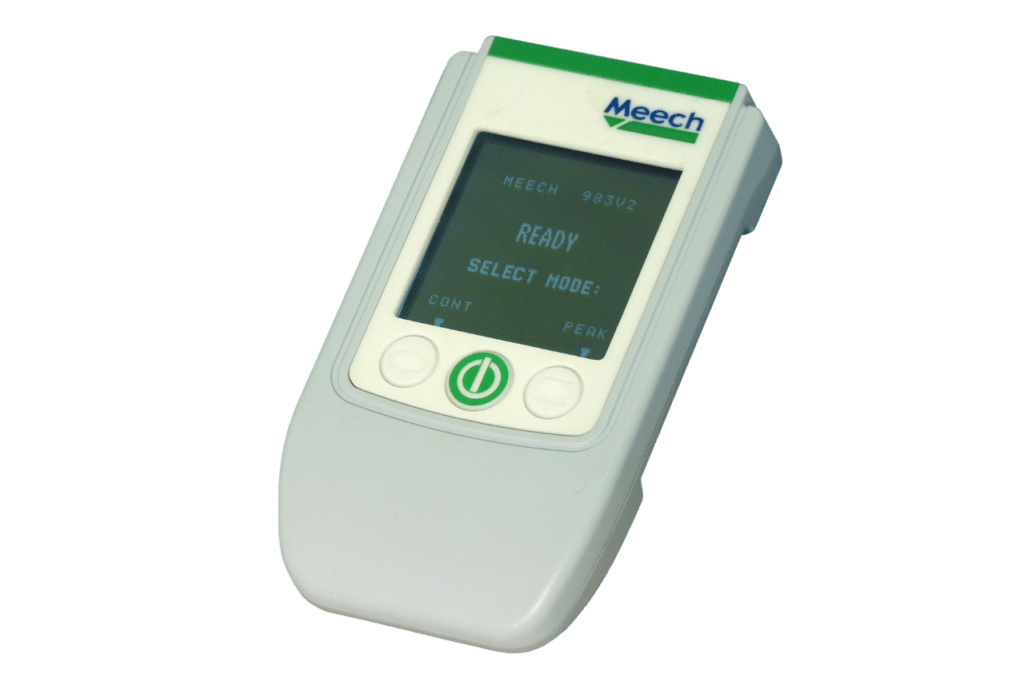
The Model 983v2 Static Locator provides a clear indication of electrostatic charges on materials. It is intended for general industrial use and has a wide measuring range of +/-200kV, measured at 150mm distance.
The 983v2 can operate in “Continuous” or “Peak Hold” mode to record changes in the level of charge or the highest charge detected respectively. It is suitable for providing a good indication of the level of static charge for use by production, maintenance, inspection and quality engineers. The 983v2 can be used on any material where static charge may be an issue.
SmartControl Touch is the latest innovation from Meech designed to meet the needs of modern automated industries and the growth of Industry 4.0 to achieve maximum productivity and output quality.
SmartControl Touch allows the user to monitor, control and adjust the performance of multiple connected Hyperion ionising bars and sensors via the integrated touch-screen or remotely.
Could we help improve your battery manufacturing process?
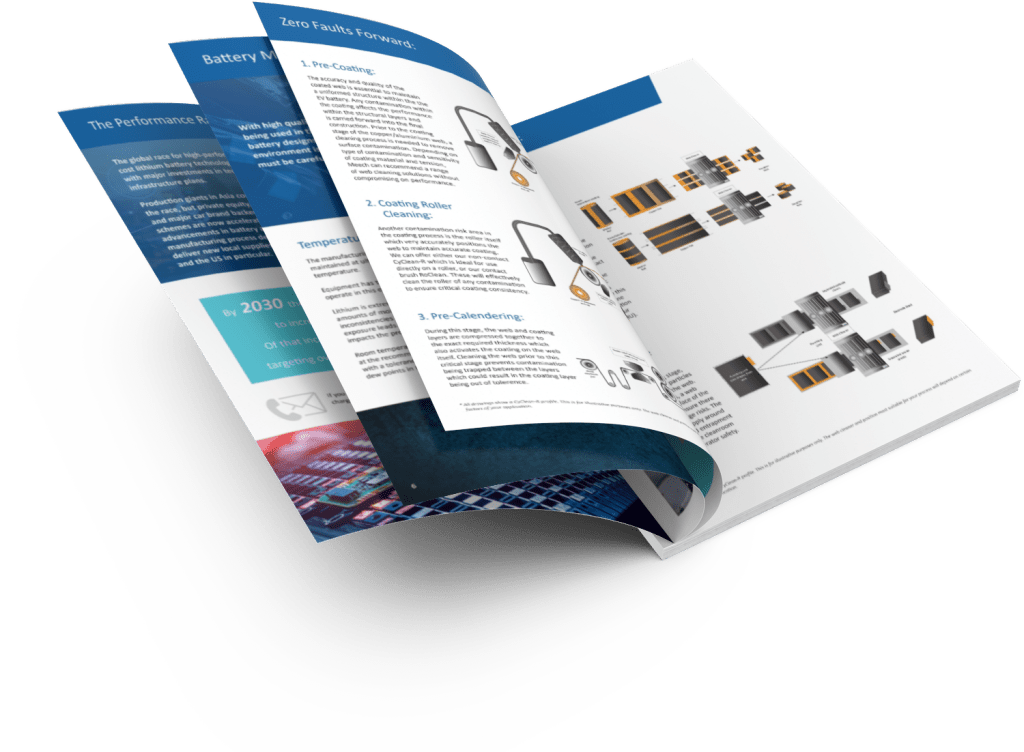