Converting
Contamination removal in converting industry

The converting process industry covers a wide range of applications, materials, and product widths. Predominantly handling thin calliper materials in roll-to-roll, or sheet-to-sheet formats, the converting process covers unwinding, sheeting, extruding, coating, drying, calendaring, laminating, delaminating, die cutting, laser cutting, slitting, printing, packaging, winding, and many more.
Frequently used web materials are papers, foils, plastic films woven and non-woven textiles. Process speeds can be slow for very intricate conversion processes but are frequently at high speeds to maximise productivity and profitability.
Processes can be on a large industrial scale, or small scale at a single end user but in both cases a large amount of power and control is needed to drive the machinery and process performance.
From its raw material form the different processes convert and add value to an enhanced product in roll or sheet form (to pass onto another production stage), or to the final product at the end of the line.
High speed material transfers often lead to static charge build up resulting in material misbehaviour on machine, ink laydown problems, and contamination attraction (from processes or environment). If not controlled process speeds become limited or changes in conditions require speeds and productivity to be reduced.
Surface contamination can become embedded affecting coating and print quality resulting in down stream product performance or poor presentation.
The high level of automation and control equipment requires high power draw and significant amounts of cooling solutions for standard operating or high seasonal peak temperatures.
With an unrivalled range of static control, static generation, sensors and datalogging, non-contact and contact type web cleaning, air-efficiency and air-cooling systems, Meech delivers a suite of cost saving solutions into the converting industry which enhances productivity, maximises yields and supports customers with the latest industry offerings to get the work done.
Our Zero Faults Forward Approach
We have identified a number of applications within the converting industry that are prone to contamination on the line. By applying the right solutions at these points, you make sure there are no weak links to your production chain. We explore these below and demonstrate our solutions…
Converting supply applications
It is critical that static electricity is controlled during converting applications. Below are some of the main areas affected by static charges during production, and our solutions to remove static charges and other contaminants:
ESD & Contamination Control On Re-winders with Lay-On Rollers
Problem:
Very high static charges are generated on the plastic web during the unwinding and rewinding process. This can cause various problems for converters and their customers, such as:
- Unpleasant shocks to operators
- Dust attraction, leading to contaminated stock
- Poor quality wound reels which can be difficult to fit onto machines and may cause feed problems
- Structural damage to coatings
- Exposing edges to damage – incorrect tension causing core crushing or core drop out
Solution:
The most effective solution to overcome these issues would be through the use of the Meech 924IPS bar, situated in the position shown.
The positioning of a Model 924IPS bar at the unwind will provide control of static charges.
However, depending on the direction of the wind, clockwise will neutralize both sides of the material. When rewinding anti-clockwise the bar will only be facing one side of the material. Due to the constant 30mm distance, combined with the powerful ionization produced by the 924IPS bar, any residual charges will be minimal on the rewound roll.
Static Control During Film Rewinding
Problem:
Winding up film on extruded or blown film lines produces high levels of static electricity, often in excess of 200 kV. This can lead to a number of major problems:
- Operators can receive painful and unpleasant shocks
- High levels of static in the reel can cause production problems for the customer
- Dust can be attracted from up to 1 metre away, leading to contamination of the film.
Solution:
The correct selection of equipment will be driven by the design of machine, space constraints etc. The model 935 fan driven ionised air blower delivers a high volume of concentrated ionised air to the wind on. The gentle flow of ionised air spreads from the blower head to give wide coverage as well as long range neutralisation. Long range ionisation ensures neutralisation of the entire film roll. Fan filters are available to ensure that only clean air is projected at the film.
To avoid the imprinting of any contamination from the roller itself to the substrate coating we suggest the use of either our CyClean-R which is ideal for use on a roller, or our contact RoClean. This will effectively clean the roller of any contamination to ensure there is no transmission to the web.
Static Control During Ink Jet Printing Preventing Misting, Dripping & Print Head Blockages
Problem:
Wide format digital printing has problems when printing onto insulative materials, resulting in poor print quality, print head blockages, ink drips (tagging) misting and poorly defined print edges. Electrostatic charges generated by the removal of protective films, and drying of the ink between passes repels the ink, preventing laydown. Small atomised ink particles are repelled by the electrostatic charges on substrate causing an ink cloud. This ink will collect and build up on the print head or will settle on the substrate in the incorrect position as a mist producing poor print clarity.
The ink which collects on the print head will pool before dripping into the substrate, resulting in the print being rejected. A worse problem will be the ink drying onto the print head blocking the jets. This can and does result in replacement of the print heads.
Solution:
The installation of a Meech 976 Mini Pulsed DC system will provide the ultimate solution to all of these problems. As a light weight compact electrostatic control system, it; –
- Limits the additional weight on the print carriage, when compared to an AC system.
- Enables higher print quality when compared to a comparative AC system.
- Reduces the press down time for head maintenance.
- Prevents scrapping product due to ink drips.
- Reduces the risk of expensive head replacements.
During this stage, the web and coating layers are compressed together to the correct thickness, activating the coating on the web itself. Cleaning the web prior to this critical stage prevents contamination being trapped between the layers themselves.
Preventing Damage Or Weakening Of RFID Tags Due To ESD
Problem:
The application of RFID tags to an adhesive web prior to laminating can result in the generation of electrostatic charges high enough to destroy or weaken the chip in the tag. Failure to control these charges can result in field failures and loss of product and production.
Solution:
The adhesive web needs to be kept free of electrostatic charge during the transfer of the tag. The removal of the tag from the paper carrier will generate high levels of electrostatic charge. Installing a Meech 261 flexi nozzle to trickle feed air over the RFID tag as it separates from the paper carrier can allow the air flow to be utilised to produce a down force, helping adhere the label in place while neutralising the electrostatic charges. Mounting a Meech 971 bar (1) under the web path can control the electrostatic charge on the web during transfer and rewinding, while a second 971 bar (2) will be required to neutralise the lamination prior to being applied to the RFID tags and web.
ESD Damage Or Weakening Of RFID Tags During Die Cutting
Problem:
RFID tags are received on a reel, unwound and guillotined prior to application on to the product. The tags are easily spoilt by static discharges and require good static control during processing
Static charges generated through the un-wind can exceed the tolerance levels on RFID or security tags and can cause the following associated problems:
- Static charges blowing the RFID chip and rendering it useless
- Operators receiving unpleasant shocks
- Attraction of dust and other airborne contaminants.
Solution:
A model 971 and 977CM aimed at the nip of the unwind and rewind rolls will bathe the reel in ionised air, neutralising any static charge on the reels will prevent electrostatic discharges resulting in EMP and damage to the chip. Further neutralisation will be required during the separation of the guillotine. This needs to be implemented by using Meech 261 flexi nozzles to blow ionised air into the die to neutralise it.
Narrow Web Label Ink Jet Printing and Laser Die Cutting
Problem:
Spartanics NW140 UV InkJet Label Printing and die cutting machine.
Dust particles and static charges on the web seriously affect the overall print quality of the labels printed on the machine.
The machine has a combination of Inkjet printing and laser cutting capabilities and utilises multifarious substrates, such as Paper , Vinyl, PP, PE, Metalized films etc, dust and surface contamination creates print related defects and static charges cause poor print and register issues.
Solution:
Installation of TakClean Contact Web Cleaning System into the press after the unwind and immediately before the print section removes contamination and with the inbuilt static elimination system ensures a static free web, thus improving overall print quality.
The slitting process can cause a lot of debris which can contaminate the coated web substrate. The use of a web cleaner at this stage ensures that the particles are removed from the surface of the web and filtered away from the operating atmosphere to avoid re-contamination. With such a high risk of contamination at this stage, cleaning is imperative to avoid the risk of future electrical shortages and expensive rejects.
Static Problems Caused During Stacking Of Shingled Sheets On A Sheeting Machine
Problem:
When delivering single or shingled (overlapped) sheets onto either a conveyor or a stack, static causes the sheets to cling together resulting in collating problems. The problem is more pronounced on shingle type delivery systems. It is important that the static charges are eliminated from the individual sheets.
Solution:
Single or multiple 261 DC ionizing nozzles with a flexible air output nozzle can be positioned in such a way that the ionized air produced via the 261 flows between the sheets during the delivery process. Model 915 bars positioned as shown ensure full and effective neutralisation of static charges across the full sheet width.
The 261 flexible nozzles can be positioned either below the conveyor roller or at the side of the sheets. The flexible nozzle can easily be adjusted to suit the machine. This allows the 261 nozzle to be installed in positions that would not normally be possible with alternative types of static elimination system.
Wrapping & Contamination Problems With Bottle Overwrapper Machine
Problem:
There are 3 areas of concern with this type of packaging machine:
- Dust Attraction during unwinding web
- Electrostatic attraction of web to cutting knife and vacuum transfer belt
- Electrostatic attraction of sheet to itself during overwrapping
Solution:
- A Meech 935 ionising blower is used to control charges on both unwinding rolls
- A Meech 915 bar neautralises the charges on the web prior to entry to the sheeting knife area
- A Meech 971 bar is used to prevent electrostatic charges from causing sheets to be pulled out from under the containers being wrapped.
Static Problems With Wicketing Machine Bagging Lines
Problem:
During the bag making process, there are many problems caused by static charges, or aided by applying a static charge.
Area 1:
- Static charges generated by the unwinding material will attract contamination to the material. This has a major impact for food packaging.
- The web is then folded over the “A” frame trapping static charges inside the two layers.
Area 2:
- The addition of a gusset to the bag: the material needs to be held in place to prevent the gusset from moving out of alignment.
- Where a reinforcing strip of plastic is required to strengthen the handle section of the bag, this needs to be held in position.
- The punching of a handle through the material can cause the bag to open and stick to the punch.
Area 3:
- Static charges on the material entering the sealing and cutting process will cause the material to stick to rollers and fail to feed onto the wicketing conveyor belts.
Area 4:
- Static charges on the bags being placed onto the pegs will cause the bags to push apart and not hang vertically. This will result in the bags being pulled off the pegs by the wicketing arms.
- Not controlling the static charges through the production process, will cause customer issues as the bags will fail to open properly.
- High static charges on the single bags cause a major problem at the bag collating area, especially on high-speed machines.
Solution:
Many antistatic systems have been evaluated in this application. Although adequate for slow machines, they are not fully effective on the newer high-speed machines. To allow maximum efficiency the recommended static control system below will optimise the production process:
Area 1:
- The use of a long-range ionising bar such as the 971-30 kV Pulsed DC bar will prevent the attraction of contamination to the material.
- Using a 924IPS bar prior to folding ensures the charges are removed from the inside face of the web, reducing the impact of static on the finished product.
Area 2:
- Applying a static charge, using a 993R bar and generator, to bond only the gusset in position, will prevent material movement and alignment issues.
- Applying a static charge, using a 993R bar and generator, to the web and the reinforcing strip will temporarily lock the two layers into position prior to being heat welded together.
- Applying a static charge, using a 993R bar and generator, to the top edge of the web temporarily bonds the material together, preventing the punch from separating the layers.
Area 3:
- The compact size of the 914 AC bars allows high powered ionisation to be delivered, removing static charges that have been generated during the production process.
Area 4:
- Two Meech 971IPS bars are required during the wicketing process. The first bar removes charges from the bags as they pass on the wicketing arms. The second uses a small quantity of compressed air, blowing ionisation continuously over the bags on the pegs, preventing charges being regenerated during the application of the next bag onto the pegs.
At the winding process we suggest a number of solutions for the best results. Prior to winding, surface cleaning of the substrate is recommended to not trap contamination within the battery film wind. To overcome static issues, which can be both dangerous and extremely detrimental to the battery performance, effective static control should also be introduced. This will neutralise any static charges caused by the winding process.
* All drawings are for illustrative purposes only. The position of the static control and web cleaning solutions most suitable for your process will depend on certain factors of your application.
Web Cleaning Solutions
Meech is a leading Web Cleaning manufacturer with a comprehensive range of four systems. Each system is based on a different cleaning principle, this uniquely allows us to provide our customers with a system best suited for their application. All Meech systems incorporate the latest shockless AC static control bars as standard which is crucial for comprehensive contamination removal. Meech has more than 200 successful web cleaning installations in a range of industries including Packaging, Printing and Converting.
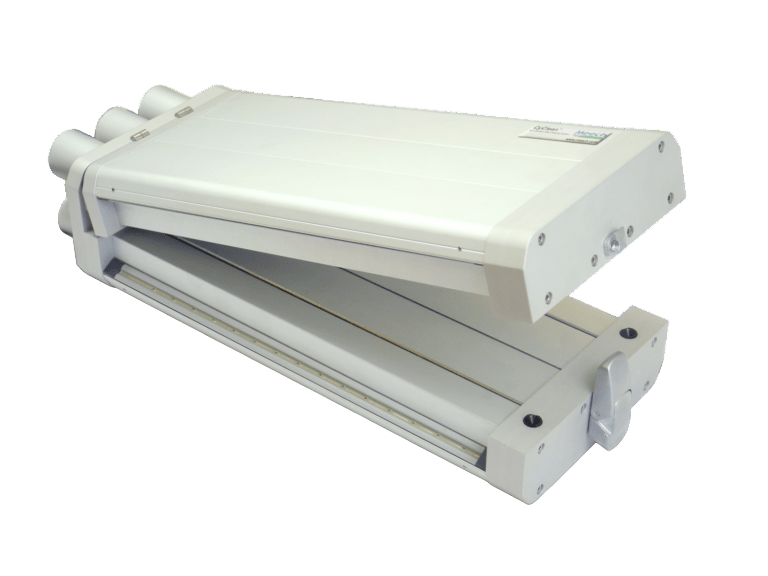
Meech CyClean™ has been designed in response to demand for a compact, high performance, non-contact web cleaner.
Through the application of advanced computational fluid dynamics, CyClean removes and extracts contamination below 1 micron.
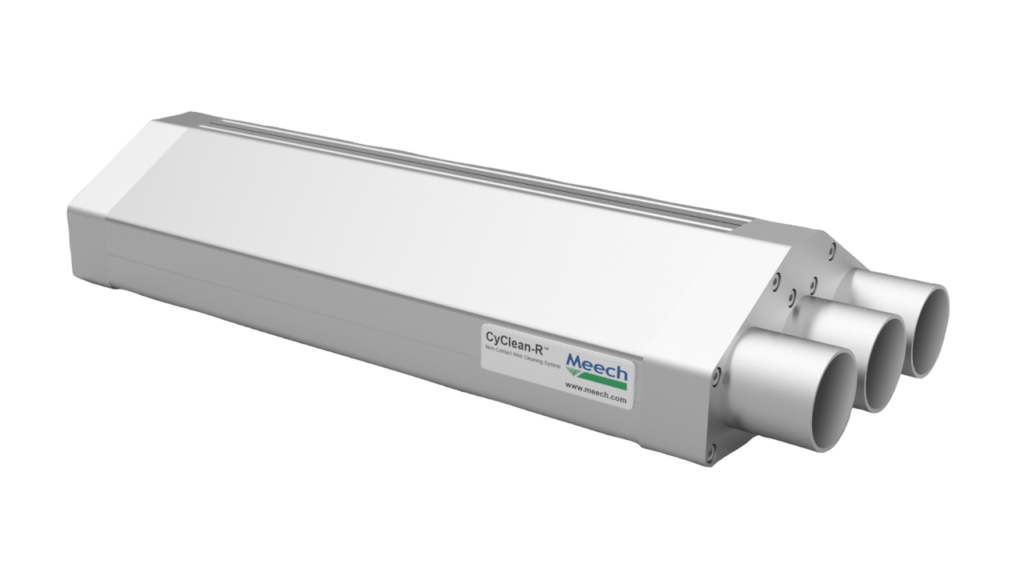
The CyClean-R provides a specialised solution for low-tension web cleaning.
The CyClean-R is designed to be positioned on the roller, where the web tension is at its highest, therefore bypassing the issues of low tension and still delivering excellent surface cleaning.
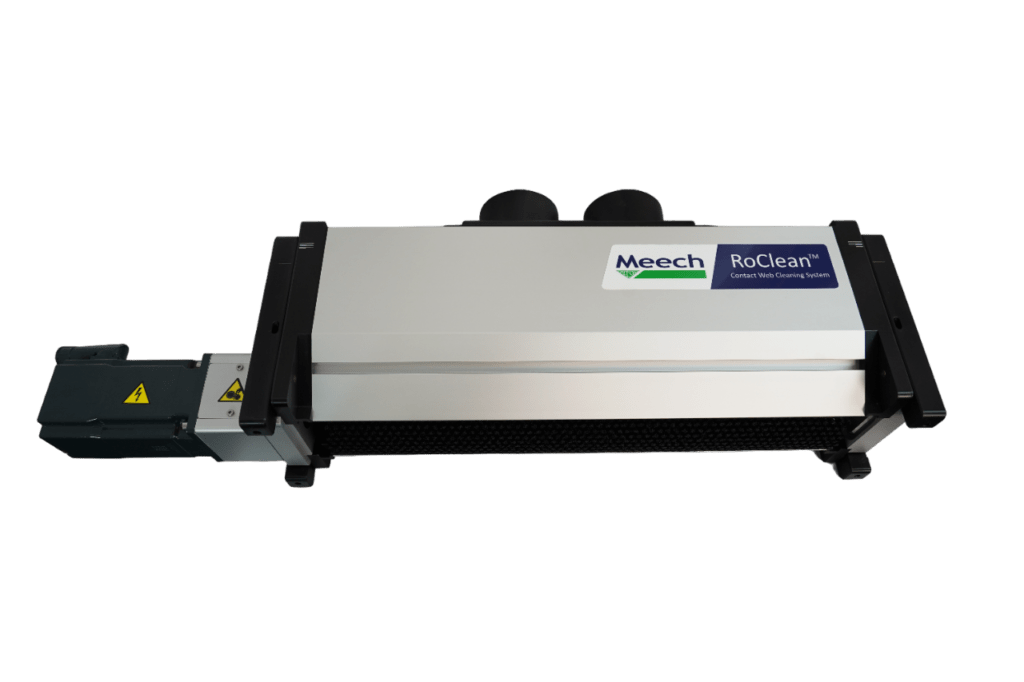
RoClean is the latest contact web cleaner, delivering excellent surface cleaning results for the battery film manufacturing industry.
RoClean effectively cleans the web surface through the use of both static control and an efficient bristle roller brush.
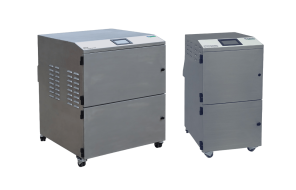
Meech web cleaners are supplied with Meech Air Handling Units (AHUs) to ensure air balance is maintained to perfectly control accuracy of air pressure and vacuum. These are compact, industrial specification units and can also be performance monitored via PLC control.
Static Control Solutions
Meech is a market leader in manufacturing and supplying static control products since the 1960’s; offering a wide range of electrostatic products that provide anti-static and ESD protection and measurement, static generation, electrostatic control and elimination.
Powered by 24V DC the Hyperion 924IPS is the most compact pulsed DC bar available on the market.
The 924IPS features Meech’s Ion Current Monitoring (ICM) technology, this ensures performance is maintained with local and remote alerts when the bar needs cleaning.
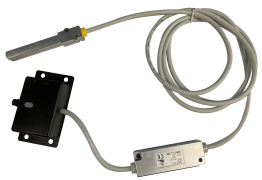
ur closed-loop feedback system takes advantage of the adjustable balance of pulsed DC ionising systems.
The system comprises a Hyperion SmartControl and up to 5 Hyperion ionising products for closed-loop feedback. Once connected to the SmartControl sensor, measures the voltage on the web downstream of the ionising bar.
This measurement can be fed back to the ionising product which automatically adjusts the balance of the output to achieve a completely neutral web. This is a continuous process that constantly measures and adjusts to achieve the very best static control at all times.
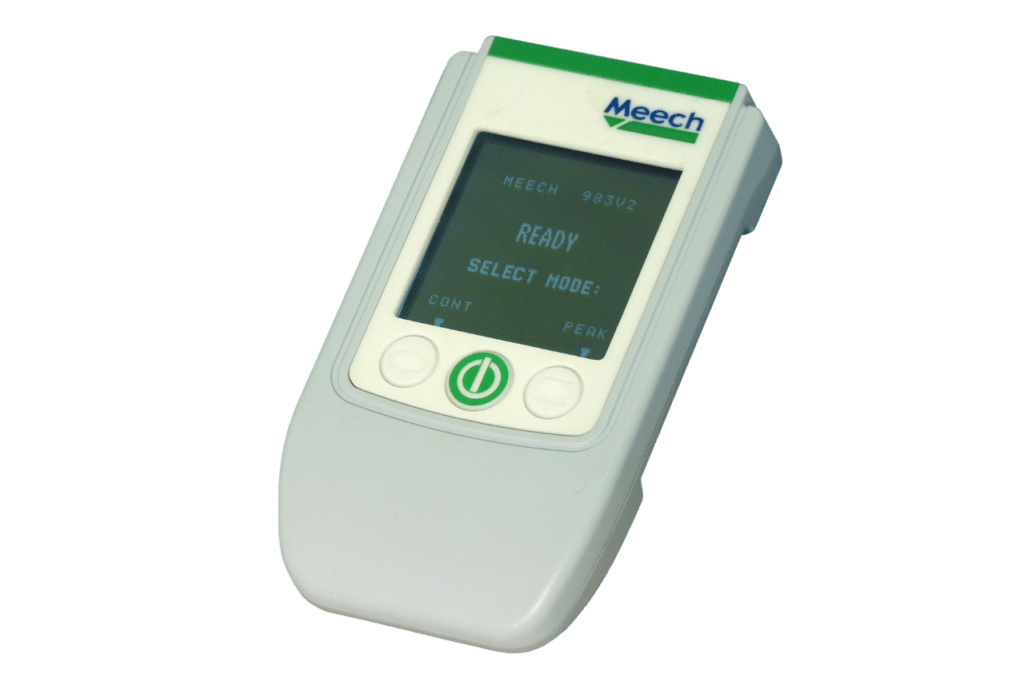
The Model 983v2 Static Locator provides a clear indication of electrostatic charges on materials. It is intended for general industrial use and has a wide measuring range of +/-200kV, measured at 150mm distance.
The 983v2 can operate in “Continuous” or “Peak Hold” mode to record changes in the level of charge or the highest charge detected respectively. It is suitable for providing a good indication of the level of static charge for use by production, maintenance, inspection and quality engineers. The 983v2 can be used on any material where static charge may be an issue.
SmartControl Touch is the latest innovation from Meech designed to meet the needs of modern automated industries and the growth of Industry 4.0 to achieve maximum productivity and output quality.
SmartControl Touch allows the user to monitor, control and adjust the performance of multiple connected Hyperion ionising bars and sensors via the integrated touch-screen or remotely.
Could we help improve your converting manufacturing process?
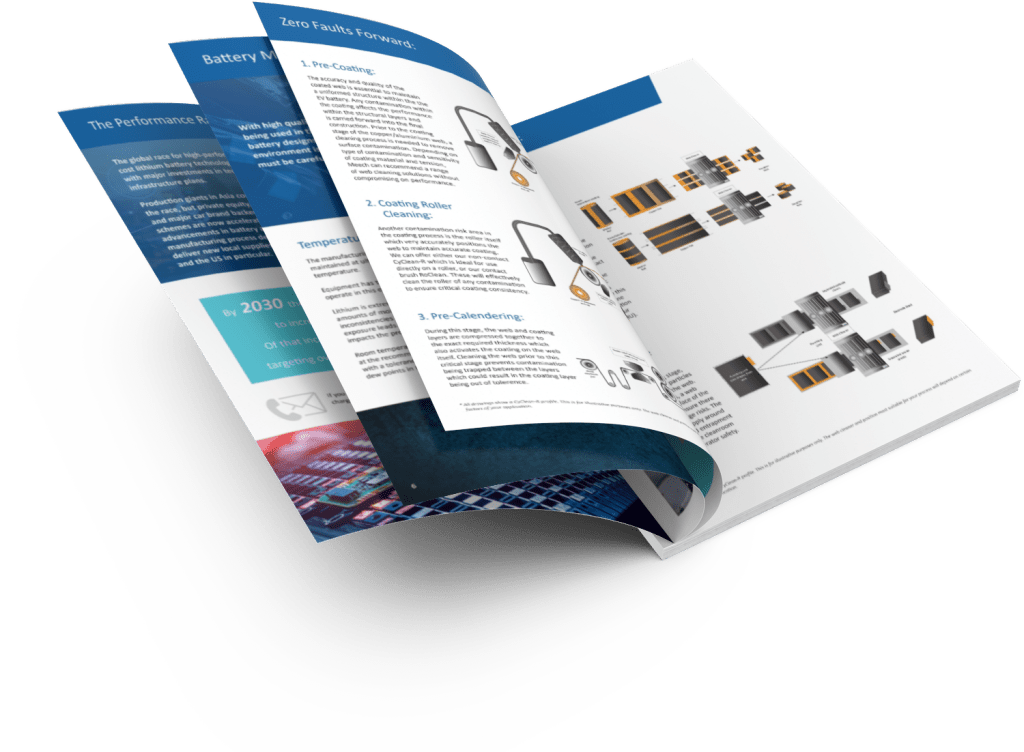