Hydrogen Fuel Cells
Contamination removal in hydrogen fuel cell production
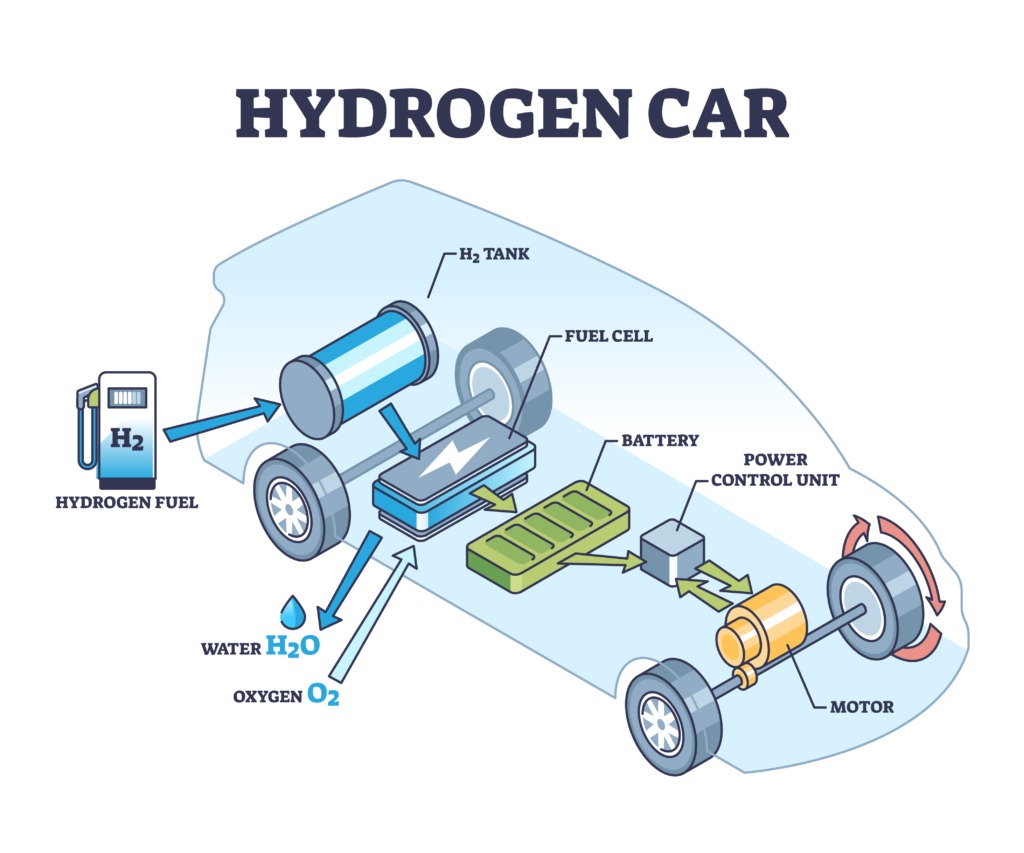
HFC technology will be an essential part of zero carbon emissions solutions. It is very clean compared to internal combustion engines with the output by-product being H2O. HFCs are likely to be paired with battery technology but are forecast to be supplied in smaller volumes into passenger automotive sector and more significantly into heavy goods vehicles, buses, shipping, material handling and even aircrafts and drones.
While it has been slower to evolve and scale-up than battery technology, it is now being actively industrialised with a focus on improved automation of key process stages.
Meech has been engaging with scale-up partners in industrialising the production processes of PEM fuel cells (proton exchange membrane) which is most commonly being adopted in the automotive sector. It is essential to avoid embedded contamination and high static charge in the cell components and Meech will work with our partners to determine the optimise solution based on available space on machine, type and characteristics of contamination and process environment. By avoiding these risks, production speeds can be optimised, yields can be maximised, and latent defects can be avoided.
Our Zero Faults Forward Approach
We have identified a number of processes within hydrogen fuel cell manufacturing that are prone to contamination on the line. By applying the right solutions at these points, you make sure there are no weak links to your production chain. We explore these below and demonstrate our solutions…
What is a Hydrogen fuel cell?
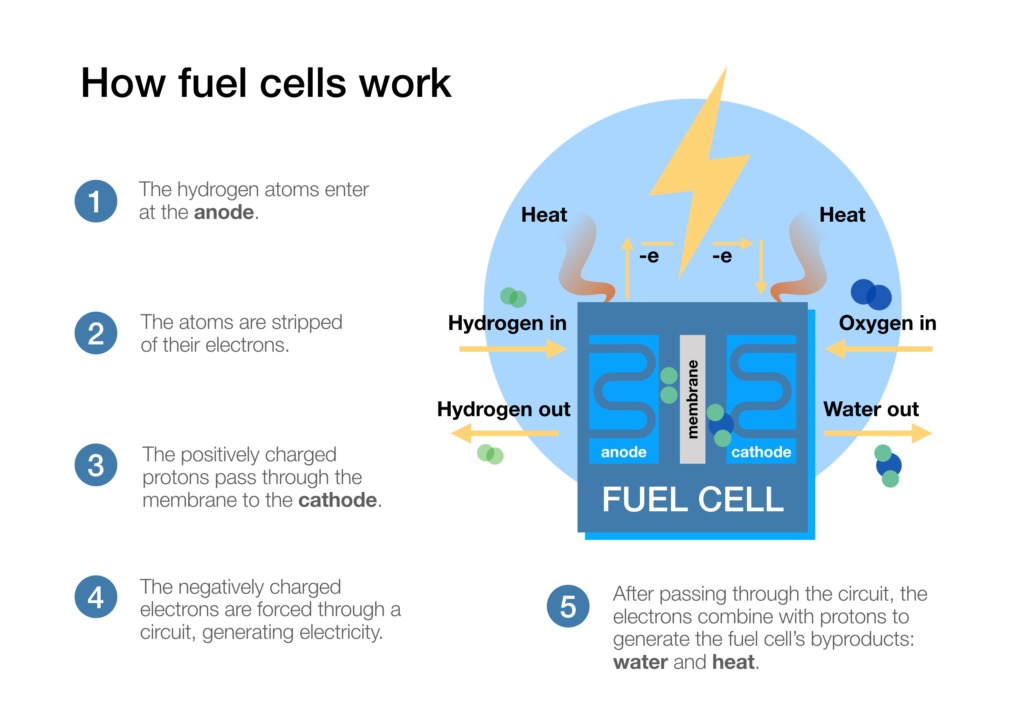
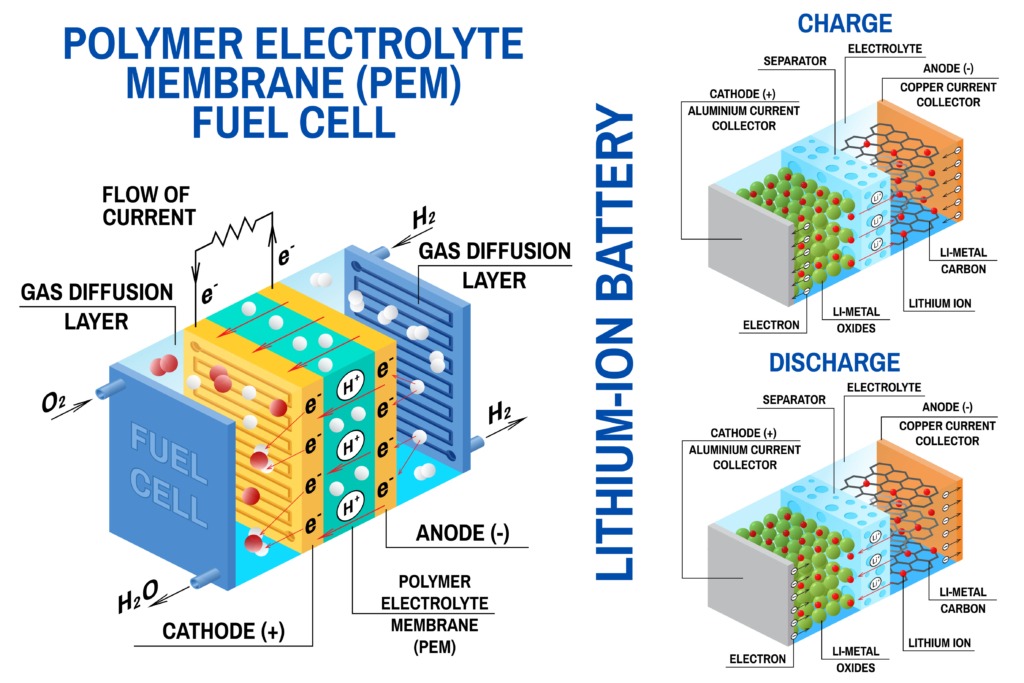
Fuel cells are devices that generate electricity through “electrochemical redox reactions” (not combustion – they don’t burn anything).
In short, they convert chemical energy of fuels (hydrogen or methane) directly into electrical energy (by combining them with oxygen). As the chemical conversion does not need thermal and mechanical energy first fuel cells are (by comparison) extremely efficient. Besides minimizing energy losses, fuel cells are also far less polluting than classic combustion engines with carbon emissions being much lower and non-toxic.
If “green” hydrogen (hydrogen created using renewable energy sources) is fuelling the cell, they only emit water vapour and warm air! Delivering overall a very clean power solution.
Complementary technologies
Fuel cells and batteries are two viable solutions to create electric powertrains and thus address the clean energy challenge. Both technologies will also have their place as a hybrid solution (combined). Depending on the application, either can be the best answer.. (we will also see them in combination)
Main differences
The single most essential difference between fuel cells and batteries is simple: a battery stores energy which it then uses, whereas a fuel cell generates energy by converting available fuel. As long as you have access to the fuel, you have access to electricity – anytime, anywhere. Interestingly, a fuel cell can also have a battery component to store the energy it is generating.
Meech has been engaging with scale-up partners in industrialising the production processes of battery cells and PEM fuel cells (proton exchange membrane) which is most commonly being adopted in the automotive sector. It is essential to avoid embedded contamination and high static charge in the cell components and Meech will work with our partners to determine the optimise solution based on available space on machine, type and characteristics of contamination and process environment. By avoiding these risks, production speeds can be optimised, yields can be maximised, and latent defects can be avoided.
primary components of the hydrogen fuel cell
Bi-Polar Plates
Bi-polar plates are designed to channel hydrogen, conduct electrons and dissipate heat from the cell:
Micro Porous Carbon Paper or Non-Woven Material
Micro porous carbon paper or non-woven material is designed to ensure there is a consistent flow and transfer of active media across the membrane:
Catalyst Coated Membrane (CCM)
A critical part of PEM fuel cell membrane is the CCM (catalyst coated membrane). This is a polymer membrane coated with anode and cathode on either side. When automating key production stages of this component in a roll-to-roll converting format, it is critical to eliminate static charges and avoid embedded contamination so the final CCM component is fully optimised and not rejected or carried forwards with a latent defects.
Primary applications: Catalyst coated membrane production
Dry Coating Stage on to Carrier Film
In the first stage, the Anode and Cathode coating material is separately coated onto a ‘carrier’ PTFE or PE carrier film (before being dried and then transferred on to each side of a single moisture sensitive polymer membrane).
Anode and Cathode carrier rolls are produced separately.
Referring to the image above, prior to coating, the carrier film must be free of contamination and neutralised of static charge (created upstream and during unwind process) – ensuring coating accuracy and stability is maintained and materials flow through converting process without difficulties.
It may also be required to clean the coating roller to help maintain a consistent calliper of coating.
As the coating layer is dried, heat related crystals can be generated from the carrier film (on underside) and this requires a specialist contact type removal process to prevent membrane damage or cross-contamination to other components.
The anode or cathode roll is then transferred to the next production stage (with zero faults carried forwards).
A combination of non-contact and contact type web cleaners are recommended – all Meech web cleaners include static ionisation bars to neutralise materials.
Several essential cleaning and static control processes are required to avoid embedded contamination and high static charge build up as shown in the above diagram.
Other critical processes exist which are being investigated as the industry increasingly adopts automation techniques.
It is also possible that live performance monitoring and date logging is needed for more critical static control solutions.
If you are designing a pilot or scaled up battery production line or have existing contamination or static charge related challenges, please get in touch with one of our Meech industry experts.
(See bottom of page for frequently required solutions).
Coating Transfer Stage onto Polymer Membrane
In the next stage, separate rolls of cathode coated and anode coated carrier films are unwound with the dry anode and cathode catalyst coatings facing towards polymer membrane.
Through a combination of compression and heat the “decal” anode and cathode coating is transferred onto each side of the polymer membrane.
The catalyst coated membrane (CCM) is then wound into a roll for next process stage.
Several essential cleaning and static control processes are required to avoid embedded contamination and high static charge build up as shown in the above diagram.
Other critical processes exist which are being investigated as the industry increasingly adopts automation techniques.
It is also possible that live performance monitoring and date logging is needed for more critical static control solutions.
If you are designing a pilot or scaled up battery production line or have existing contamination or static charge related challenges, please get in touch with one of our Meech industry experts.
(See bottom of page for frequently required solutions).
* All drawings are for illustrative purposes only. The position of the static control and web cleaning solutions most suitable for your process will depend on certain factors of your application.
Web Cleaning Solutions
Meech is a leading Web Cleaning manufacturer with a comprehensive range of four systems. Each system is based on a different cleaning principle, this uniquely allows us to provide our customers with a system best suited for their application. All Meech systems incorporate the latest shockless AC static control bars as standard which is crucial for comprehensive contamination removal. Meech has more than 200 successful web cleaning installations in a range of industries including Packaging, Printing and Converting.
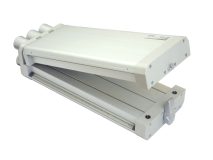
cyclean™
non-contact web cleaner
Meech CyClean™ has been designed in response to demand for a compact, high performance, non-contact web cleaner.
Through the application of advanced computational fluid dynamics, CyClean removes and extracts contamination below 1 micron.
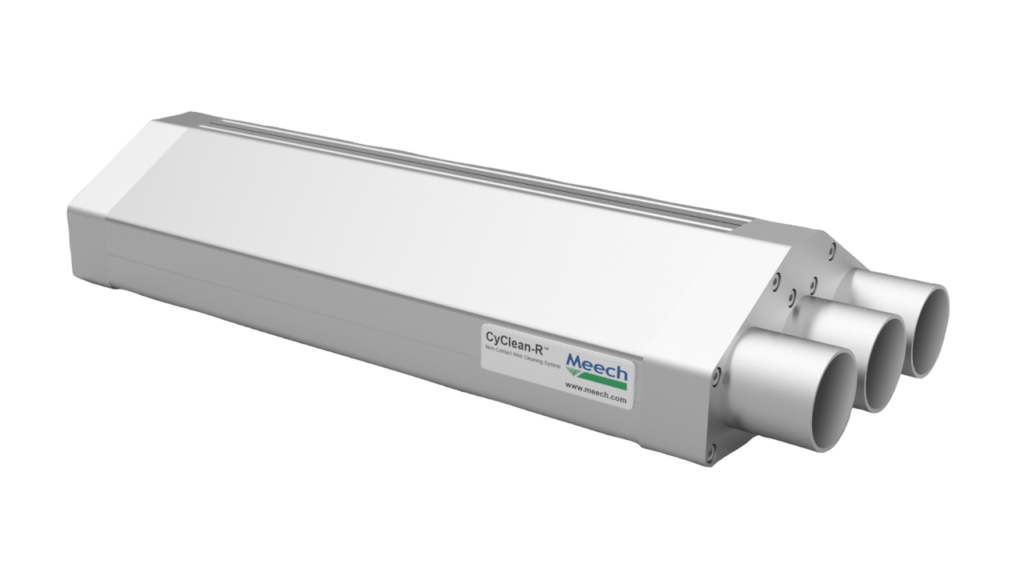
cyclean-R™
non-contact web cleaner
The CyClean-R provides a specialised solution for low-tension web cleaning.
The CyClean-R is designed to be positioned on the roller, where the web tension is at its highest, therefore bypassing the issues of low tension and still delivering excellent surface cleaning.
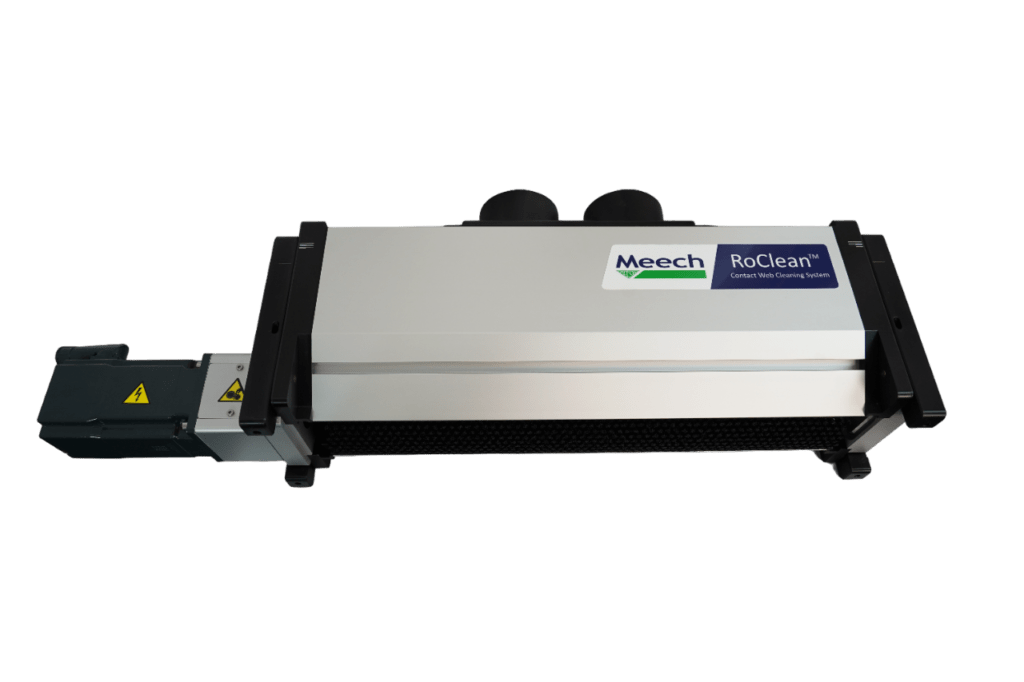
RoClean™
Contact Web Cleaner
RoClean is the latest contact web cleaner, delivering excellent surface cleaning results for the battery film manufacturing industry.
RoClean effectively cleans the web surface through the use of both static control and an efficient bristle roller brush.
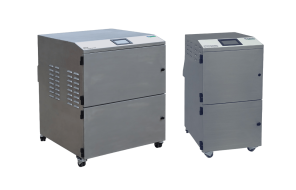
Air Handling Units
Meech web cleaners are supplied with Meech Air Handling Units (AHUs) to ensure air balance is maintained to perfectly control accuracy of air pressure and vacuum. These are compact, industrial specification units and can also be performance monitored via PLC control.
For the battery environment a new AHU option has been developed to enhance toxic contamination waste entrapment and safe filter removal by the operator.
Static Control Solutions
Meech is a market leader in manufacturing and supplying static control products since the 1960’s; offering a wide range of electrostatic products that provide anti-static and ESD protection and measurement, static generation, electrostatic control and elimination.
Hyperion™
924IPS ionising Bar
Powered by 24V DC the Hyperion 924IPS is the most compact pulsed DC bar available on the market.
The 924IPS features Meech’s Ion Current Monitoring (ICM) technology, this ensures performance is maintained with local and remote alerts when the bar needs cleaning.
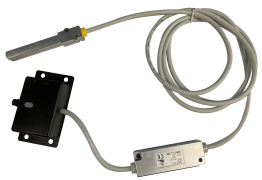
Hyperion™
Feedback Sensor
Our closed-loop feedback system takes advantage of the adjustable balance of pulsed DC ionising systems.
The system comprises a Hyperion SmartControl and up to 5 Hyperion ionising products for closed-loop feedback. Once connected to the SmartControl sensor, measures the voltage on the web downstream of the ionising bar.
This measurement can be fed back to the ionising product which automatically adjusts the balance of the output to achieve a completely neutral web. This is a continuous process that constantly measures and adjusts to achieve the very best static control at all times.
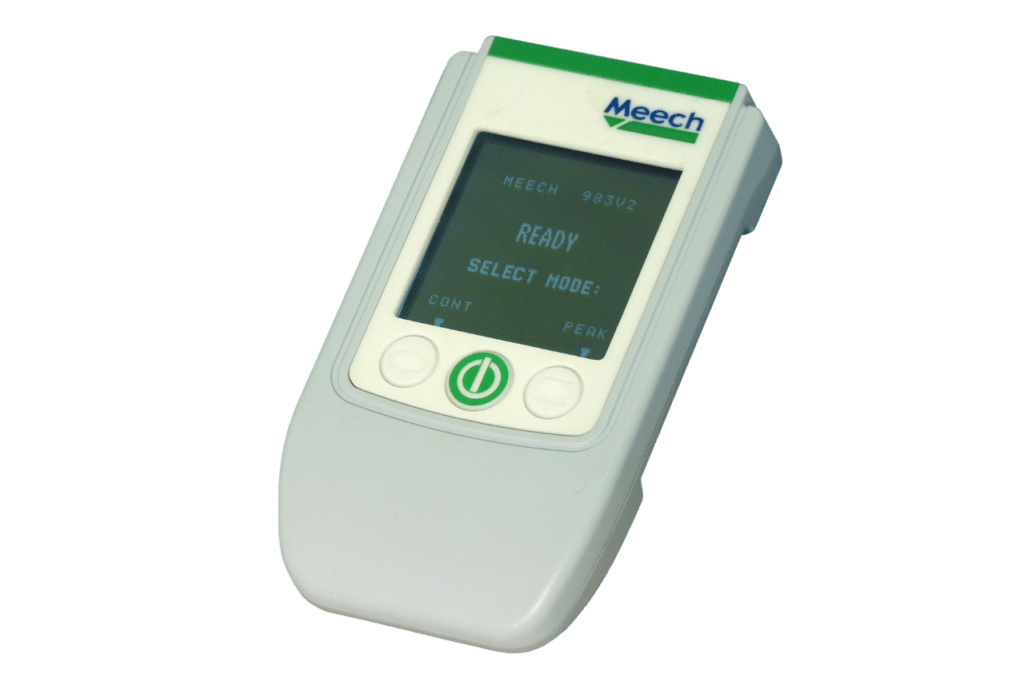
983v2 Static Locator
The Model 983v2 Static Locator provides a clear indication of electrostatic charges on materials. It is intended for general industrial use and has a wide measuring range of +/-200kV, measured at 150mm distance.
The 983v2 can operate in “Continuous” or “Peak Hold” mode to record changes in the level of charge or the highest charge detected respectively. It is suitable for providing a good indication of the level of static charge for use by production, maintenance, inspection and quality engineers. The 983v2 can be used on any material where static charge may be an issue.
HYPERION™
SMARTCONTROL TOUCH
SmartControl Touch is the latest innovation from Meech designed to meet the needs of modern automated industries and the growth of Industry 4.0 to achieve maximum productivity and output quality.
SmartControl Touch allows the user to monitor, control and adjust the performance of multiple connected Hyperion ionising bars and sensors via the integrated touch-screen or remotely.
Could we help improve your hydrogen fuel cell manufacturing process?
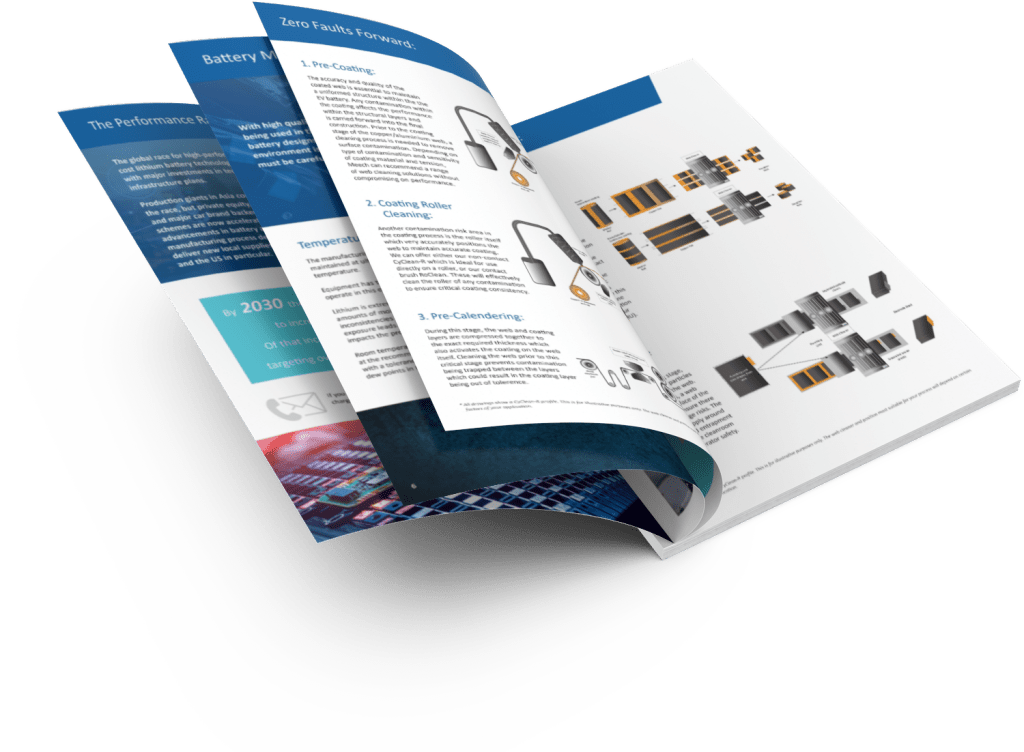