Bateria
Remoção de contaminação na produção de células de bateria
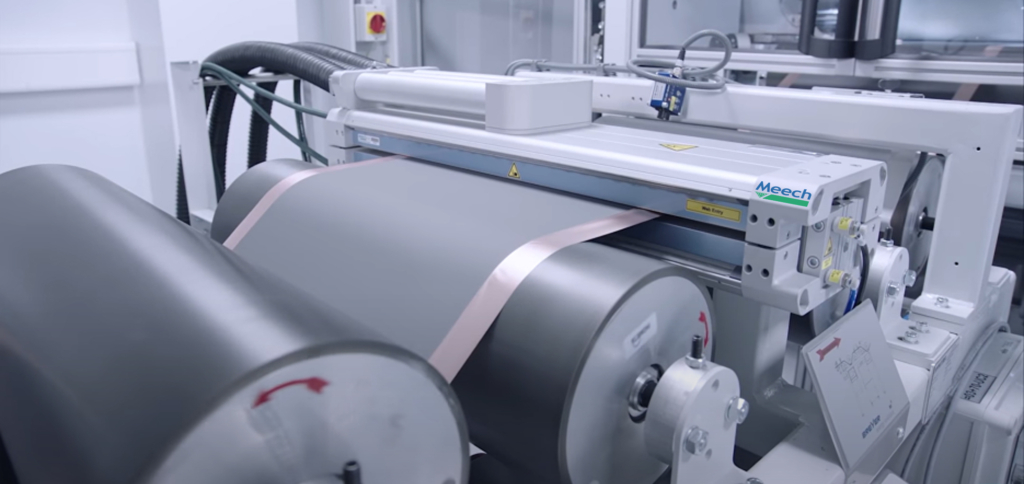
A ascensão do mercado de EV nos últimos anos levou os fabricantes a desenvolver e fabricar rapidamente baterias de íons de lítio para alimentar o boom nas vendas. Com a abertura de gigafábricas em todo o mundo para satisfazer a procura, a concorrência está a crescer e a qualidade é fundamental.
Com as tecnologias a desenvolverem-se a um ritmo acelerado, os fabricantes de baterias procuram criar uma bateria que rivalize com os veículos alimentados a gasolina ou diesel, a fim de proporcionar uma autonomia e um desempenho impressionantes.
Para isso, todas as etapas do processo de fabricação da bateria devem ser analisadas meticulosamente para produzir os melhores resultados.
Operando no ambiente de fabricação de baterias de lítio:
Uma das áreas de foco crítico para a produção de baterias EV são as condições do ambiente de fabricação. Desde as matérias-primas iniciais até a montagem das células, as condições de fabricação devem ser rigorosamente controladas. Isto cria desafios tanto para os fabricantes de equipamentos como para os operadores. Existem 3 áreas principais de consideração crítica:
O metal de lítio é extremamente sensível até mesmo às menores quantidades de umidade no ar e às inconsistências de temperatura na produção.
A menor exposição leva à redução do desempenho e impacta na redução da vida útil das baterias de íons de lítio.
A temperatura ambiente deve ser mantida nos níveis recomendados, em torno de 25°C (77°F), com tolerância de +/(-) 2°C (36°F), juntamente com pontos de orvalho baixos na faixa de <1%.
A taxa de troca de ar na sala de produção deve ser de 20 a 50 trocas de ar por hora, mantendo a introdução mínima de ar fresco para pressão positiva na sala e ventilação essencial para os operadores.
A contaminação de qualquer tipo nos materiais da bateria ou na célula pode levar a faltas elétricas diretas ou suaves – levando a rejeições no final da linha ou baixo desempenho da bateria.
A condição de sala limpa ISO 8 (ou superior) provavelmente tem foco principal na remoção de contaminação no ambiente, bem como no pessoal.
É claro que a contaminação nem sempre pode ser removida e por isso ainda existe um risco de contaminação e um impacto nos rendimentos da produção.
Problemas e partículas livres também podem ser criados nos processos de desenrolamento/bobinagem, trocas, revestimento, calandragem, corte, estampagem, corte a laser e muito mais.
Todos estes têm potencial para entrar nas camadas do filme ânodo/cátodo/separador.
Algumas contaminações serão partículas secas, livres e não ligadas, enquanto outras serão contaminações úmidas ou ligadas, que são mais difíceis de remover.
Outra área de risco é a contaminação tóxica dos materiais de revestimento à medida que são transferidos sobre rolos, cortados, enrolados e enrolados – isto pode dissipar-se no ar e tornar-se num risco respiratório para o operador.
Cargas estáticas no ambiente de fabricação podem levar a vários problemas:
Os componentes da bateria EV são muito sensíveis a cargas estáticas – os componentes devem ser descarregados durante o processo.
Cargas estáticas não controladas também afetarão o fluxo do material e causarão mau comportamento ou falha do material.
Se não forem controladas, as descargas estáticas (faíscas) criarão queimaduras dendríticas na superfície, afetando as propriedades dielétricas do filme separador – levando a comportamentos inconsistentes de carga e descarga e falha do produto.
Cargas estáticas geradas em materiais isolantes, como o filme separador, também atraem partículas, aumentando os problemas de risco de contaminação.
Nossa abordagem futura de zero falhas
Identificamos vários estágios durante o processo de fabricação da bateria que estão sujeitos à contaminação na linha. Ao aplicar as soluções certas nesses pontos, você garante que não haja elos fracos em sua cadeia produtiva. Exploramos isso abaixo e demonstramos nossas soluções…
Antes da etapa de revestimento da manta de cobre/alumínio, recomendamos o uso de um limpador de manta no substrato para remover qualquer contaminação superficial que possa afetar a espessura e a qualidade da manta revestida. Ao remover a contaminação nesta fase, garante que nenhuma partícula indesejada fique presa nas camadas, afetando o desempenho da bateria no futuro.
Para evitar a impressão de qualquer contaminação do próprio rolo no revestimento do substrato, sugerimos o uso do nosso CyClean-R, ideal para uso em rolo, ou do nosso RoClean de contato. Isto limpará efetivamente o rolo de qualquer contaminação para garantir que não haja transmissão para a banda.
Durante esta etapa, as camadas de teia e de revestimento são comprimidas juntas até a espessura correta, ativando o revestimento na própria teia. A limpeza da teia antes desta fase crítica evita que a contaminação fique presa entre as próprias camadas.
O processo de corte pode causar muitos detritos que podem contaminar o substrato da teia revestida. A utilização de um limpador de teia nesta fase garante que as partículas sejam removidas da superfície da teia e filtradas para longe da atmosfera operacional para evitar a recontaminação. Com um risco tão elevado de contaminação nesta fase, a limpeza é imperativa para evitar o risco de futuras faltas eléctricas e rejeições dispendiosas.
Semelhante ao estágio pós-corte, durante o corte do eletrodo, partículas e detritos podem contaminar a teia. Para evitar isto, a limpeza da teia nesta fase irá limpar a superfície do substrato, levando a camadas de separação limpas e claras.
No processo de bobinagem sugerimos uma série de soluções para obter os melhores resultados. Antes do enrolamento, recomenda-se a limpeza da superfície do substrato para não reter contaminação no vento do filme da bateria. Para superar problemas estáticos, que podem ser perigosos e extremamente prejudiciais ao desempenho da bateria, também deve ser introduzido um controle estático eficaz. Isto neutralizará quaisquer cargas estáticas causadas pelo processo de enrolamento.
*Todos os desenhos mostram um perfil CyClean-R. Isto é apenas para fins ilustrativos. O limpador de banda e a posição mais adequada para o seu processo dependerão de determinados fatores da sua aplicação.
Soluções de limpeza da web
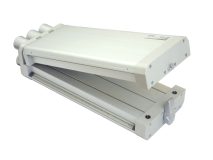
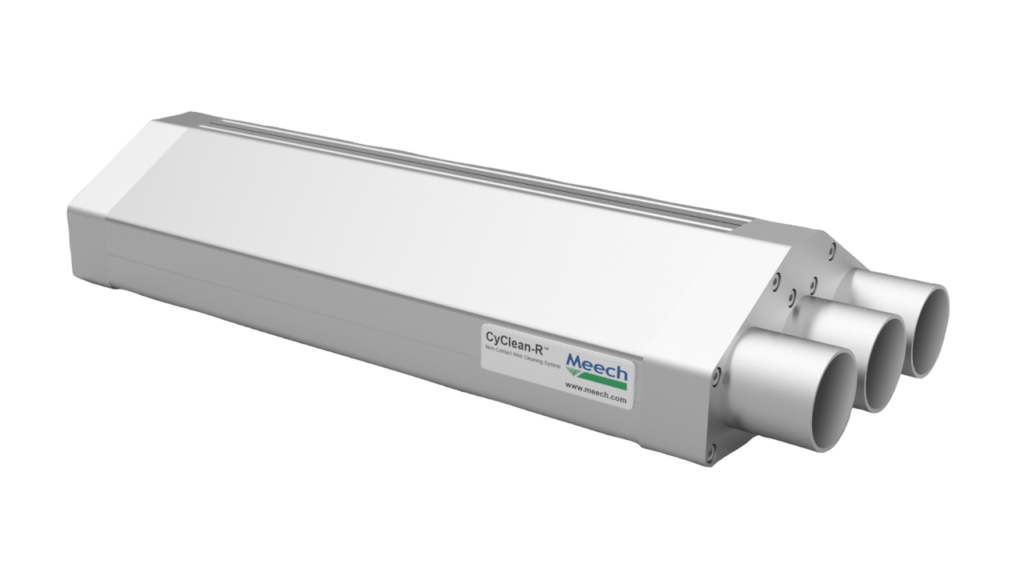
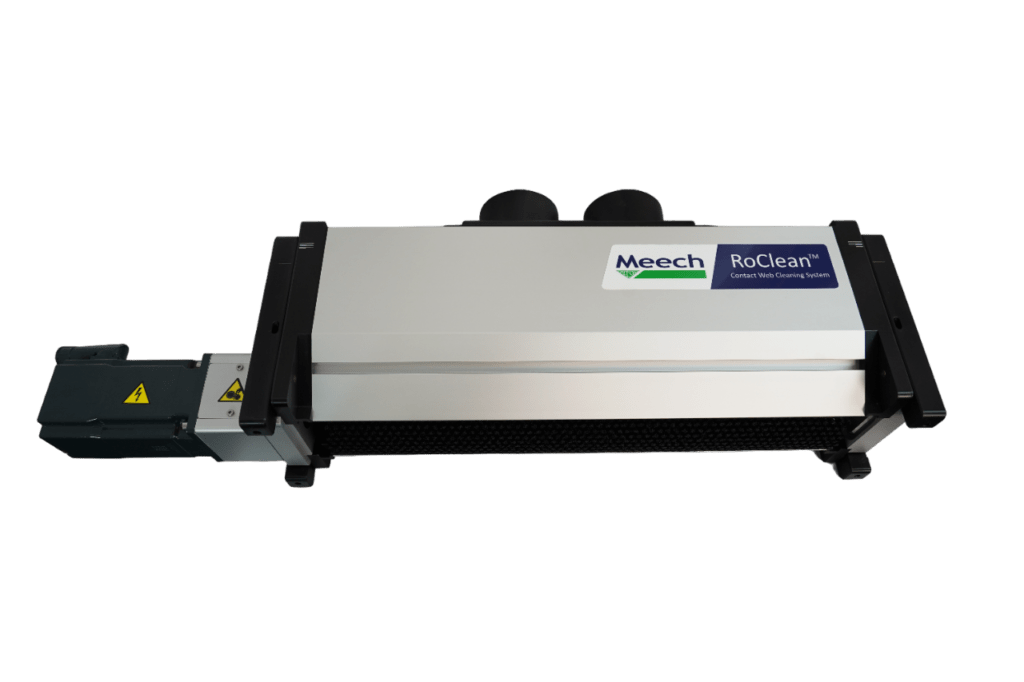
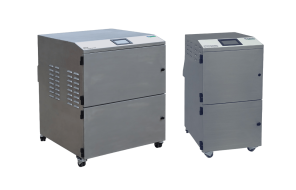
Meech CyClean™ foi projetado em resposta à demanda por um limpador de banda compacto, de alto desempenho e sem contato.
Através da aplicação de dinâmica de fluidos computacional avançada, o CyClean remove e extrai contaminação abaixo de 1 mícron.
O CyClean-R oferece uma solução especializada para limpeza de bandas de baixa tensão.
O CyClean-R foi projetado para ser posicionado no rolo, onde a tensão da banda é mais alta, evitando assim os problemas de baixa tensão e ainda proporcionando excelente limpeza superficial.
RoClean é o mais recente limpador de tela de contato, que oferece excelentes resultados de limpeza de superfícies para a indústria de fabricação de filmes de bateria.
RoClean limpa eficazmente a superfície da banda através do uso de controle estático e de uma escova giratória de cerdas eficiente.
Os limpadores de teia Meech são fornecidos com unidades de tratamento de ar (AHUs) Meech para garantir que o equilíbrio do ar seja mantido para controlar perfeitamente a precisão da pressão do ar e do vácuo. Estas são unidades compactas de especificação industrial e também podem ter desempenho monitorado via controle PLC.
Para o ambiente da bateria, foi desenvolvida uma nova opção de AHU para melhorar a retenção de resíduos de contaminação tóxica e a remoção segura do filtro pelo operador.
Soluções de controle estático
Alimentada por 24 Vcc, a Hyperion 924IPS é a barra CC pulsada mais compacta disponível no mercado.
O 924IPS possui a tecnologia Ion Current Monitoring (ICM) da Meech, que garante que o desempenho seja mantido com alertas locais e remotos quando a barra precisar de limpeza.
Nosso sistema de feedback de circuito fechado aproveita o equilíbrio ajustável dos sistemas ionizantes CC pulsados.
O sistema compreende um Hyperion SmartControl e até 5 produtos ionizantes Hyperion para feedback de circuito fechado. Uma vez conectado ao sensor SmartControl, mede a tensão na rede a jusante da barra ionizante.
Esta medição pode ser realimentada para o produto ionizante, que ajusta automaticamente o equilíbrio da saída para obter uma rede completamente neutra. Este é um processo contínuo que mede e ajusta constantemente para alcançar o melhor controle estático em todos os momentos.
O Localizador Estático Modelo 983v2 fornece uma indicação clara de cargas eletrostáticas nos materiais. Destina-se ao uso industrial geral e possui uma ampla faixa de medição de +/-200kV, medida a uma distância de 150mm.
O 983v2 pode operar no modo “Contínuo” ou “Peak Hold” para registrar alterações no nível de carga ou na carga mais alta detectada, respectivamente. É adequado para fornecer uma boa indicação do nível de carga estática para uso por engenheiros de produção, manutenção, inspeção e qualidade. O 983v2 pode ser usado em qualquer material onde a carga estática possa ser um problema.
SmartControl Touch é a mais recente inovação da Meech projetada para atender às necessidades das indústrias automatizadas modernas e ao crescimento da Indústria 4.0 para alcançar a máxima produtividade e qualidade de produção.
O SmartControl Touch permite ao usuário monitorar, controlar e ajustar o desempenho de múltiplas barras ionizantes e sensores Hyperion conectados por meio da tela sensível ao toque integrada ou remotamente.
Podemos ajudar a melhorar seu processo de fabricação de baterias?
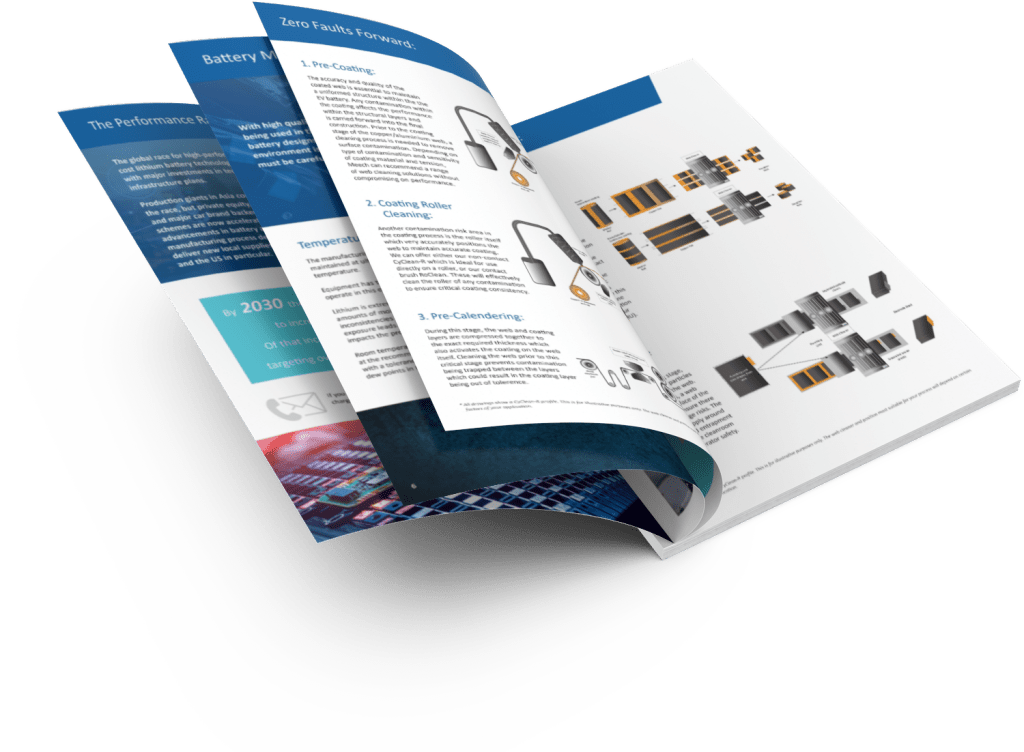