Food & Drink
Contamination removal in food & drink manufacture
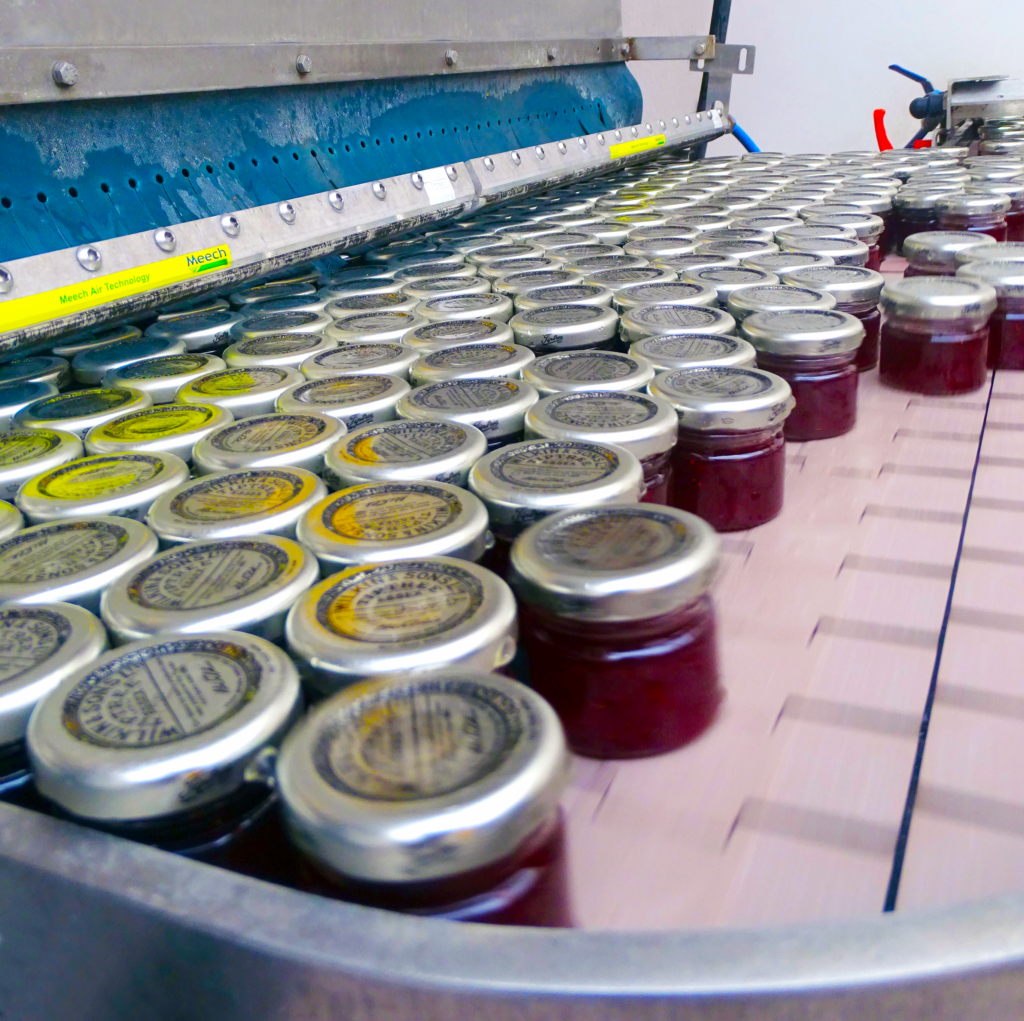
The food and drink industry consists of companies that process raw commodities into finished food and drink products. It also includes the packaging and distribution of these products for consumer consumption. It is a highly regulated industry where high-quality standards need to be maintained.
Uncontrolled static charges can become a challenge in the industry. Static attracts the airborne dust and other contaminants which will have a negative impact on the quality of the end product. In the food and drink industry, poor quality will create unnecessary waste, increase production costs, and have a possible negative effect on the reputation of the company.
The key benefits of installing an efficient cleaning or anti-static solution is a production process free of static and contaminants, and substantially improved end of line yields, with some manufacturing companies experiencing as much as a 30% decrease in waste. These solutions can also reduce wear and tear on machinery and extend the lifespan of equipment.
Meech provides solutions across the industry with static control, surface cleaning and air technology products used in the food and beverage production and packaging. Keeping high standards of safety, product quality and production yields will drive in a successful and profitable operation.
Our Zero Faults Forward Approach
We have identified a number of applications within food and drink manufacturing that are prone to contamination on the line. By applying the right solutions at these points, you make sure there are no weak links to your production chain. We explore these below and demonstrate our solutions…
Food & Drink applications
It is critical that static electricity is controlled during the manufacturing of food and drink. Below are some of the main areas affected by static charges during production, and our solutions to remove static charges and other contaminants:
Handling & Storage of Combustible Organic Ingredients
The handling and storage of combustible organic ingredients like flour or sugar, and flammable products like ethanol, generate dangerously high levels of static electricity. According to a report published by Dust Safety Science, food products made up 46% of fires and explosions recorded in 2020.
Meech static control range offers a plethora of products that will help overcome those issues. View Hyperion range of Ionising bars HERE for more information.
Filling & Packing Stages
Static is a big problem at the filling or packing stages, as whenever materials such as film or paper move over rollers, high static charges are generated. This is an obvious health and safety hazard but will also attract dust particles from any adjoining surface and from the air. This not only contaminates the packaging, but can compromise the seal if particles get trapped there. This can severely affect yields as such packaging will have to be destroyed.
Meech provides the widest range of surface cleaning solutions that will eliminate those risks. View range of web cleaning systems HERE for more information.
Cleaning Containers
Cleaning containers before filling with food or drink. Energy savings and sustainability are hot topics in all industries, not least food and beverage. Due to this, traditional pre-fill water rinse systems are becoming far less attractive. At the same time, ionised air rinsing systems are being developed further and now offer a viable alternative.
Meech has engineered an energy efficient, sustainable ionised air rinsing system that will clean the container whilst maintaining low operations costs. View our range of IonRinse and JetStream systems to find out more.
Chocolate Sticking to Moulds
Chocolate Sticking to Moulds During Chocolate Manufacture. Moulded chocolate will generate static charges. This will also transfer to the moulds. The static charges will prevent the chocolate from being de-nested from the mould adding additional manufacturing time. Neutralising the moulds between each filling cycle will prevent electrostatic charges building to a level high enough to cause problems. Our Ionising bars will support to overcome those issues.
Static Support
Static charges not always have a negative impact in the production of food and beverage. There are instances where static can actually support the process.
For example, in the stacking & pinning food sachets before wrapping. Manufactures of dried food products, which require additional sachets or cooking instructions to be wrapped inside the pack, have problems with the sachets or literature slipping or becoming separated. This failure to pack properly will cause manufacturing rejects and additional business costs. The scientific application of static electricity can produce a quick and effective solution to this package related problem.
View our range of static generation equipment HERE.
* All drawings are for illustrative purposes only. The position of the static control and web cleaning solutions most suitable for your process will depend on certain factors of your application.
IonRinse™ & JetStream Air Knives
IonRinse™
Ionised, waterless, air rinsing technology has enabled Meech to produce an air rinser that offers significant energy savings and improved sustainability over traditional industrial pre-fill water rinsing systems. Ideal for industrial perform, container and can rinsing and cleaning, the IonRinse out-performs water-based cleaning systems in many areas, not least in the energy savings and sustainability it offers customers.
JetStream Air Knives
The Meech JetStream ionising air knife system is more than just a piece of equipment, it’s a world-beating solution to contamination removal. Capable of being used in a diverse range of applications – both large and small – JetStream’s unique technology provides ultimate performance combined with outstanding energy efficiency. The two versions available are ionising and non-ionising.
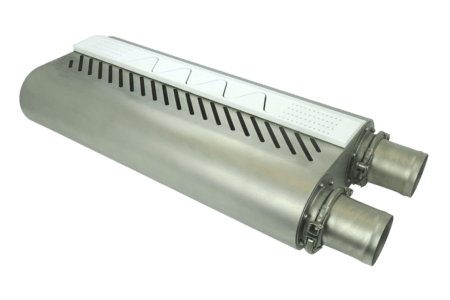
The IonRinse™ system combines powerful AC ionisation, a custom designed airflow distributor and high quality inline filtration to provide the ultimate in ionised air rinsing.
The high velocity ionised air exits the IonRinse head unit via the airflow distributor. The control of the airflow coupled with the neutralisation of static charges releases contamination from the container which is extracted to the inline filter unit. The blow and vacuum airflows are provided by the central blow, vacuum and filtration unit.
Cleaning performance is maximised with the container fully inverted (opening facing down) as it travels over the IonRinse head.
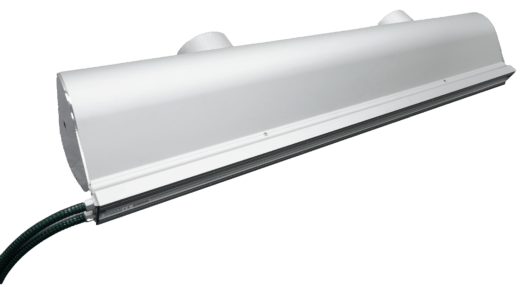
The Meech non-ionising JetStream air knife is powered by a high-pressure fan unit that provides air to the unique “Tear Drop” profile manifold/s. Capable of being used in a diverse range of applications the unique technology used in the JetStream provides ultimate performance combined with outstanding energy efficiency. This version is provided without Meech ionisation, for use in applications where static removal is not necessary.
Static Control Solutions
Meech is a market leader in manufacturing and supplying static control products since the 1960’s; offering a wide range of electrostatic products that provide anti-static and ESD protection and measurement, static generation, electrostatic control and elimination.
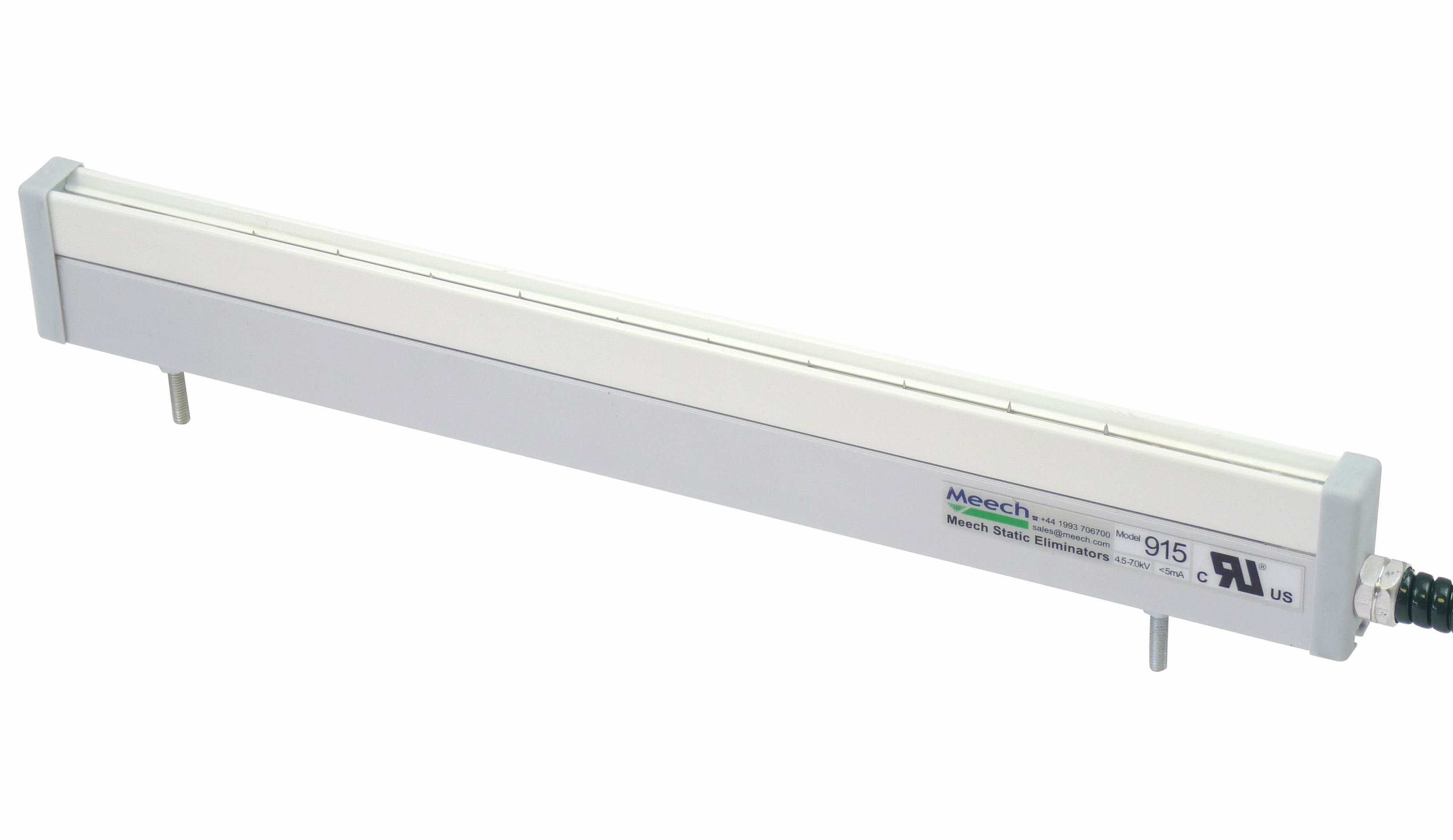
The 915 AC Anti-Static Bar offers fast and powerful static control for high speed applications.
The Meech Model 915 AC Anti-Static Bar has been designed to meet the most arduous of static elimination problems, including those encountered in high speed web applications.
The powerful performance of the Model 915 provides very fast decay times and effective ionisation up to distances of 150mm. The Model 915 bar is shockless and is easily maintained. It is powered by the Model 904.
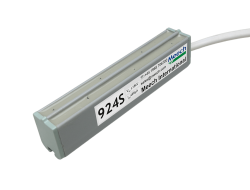
The Meech 924S ionising bar has been designed to provide highly effective short-range ionisation using Pulsed DC Technology. It is particularly suited for use on wide format digital printers. At 32mm high by 22mm wide it is extremely compact and designed specifically to provide a solution that works effectively for manufacturers of wide format inkjet printers.
The 924S DC Bar provides ionisation through alternating positive and negative emitter pins mounted in an FR ABS extrusion. The titanium emitter pins are resistively coupled to the high voltage pulsed DC source, rendering the emitters shockless to touch and offering many years of service.
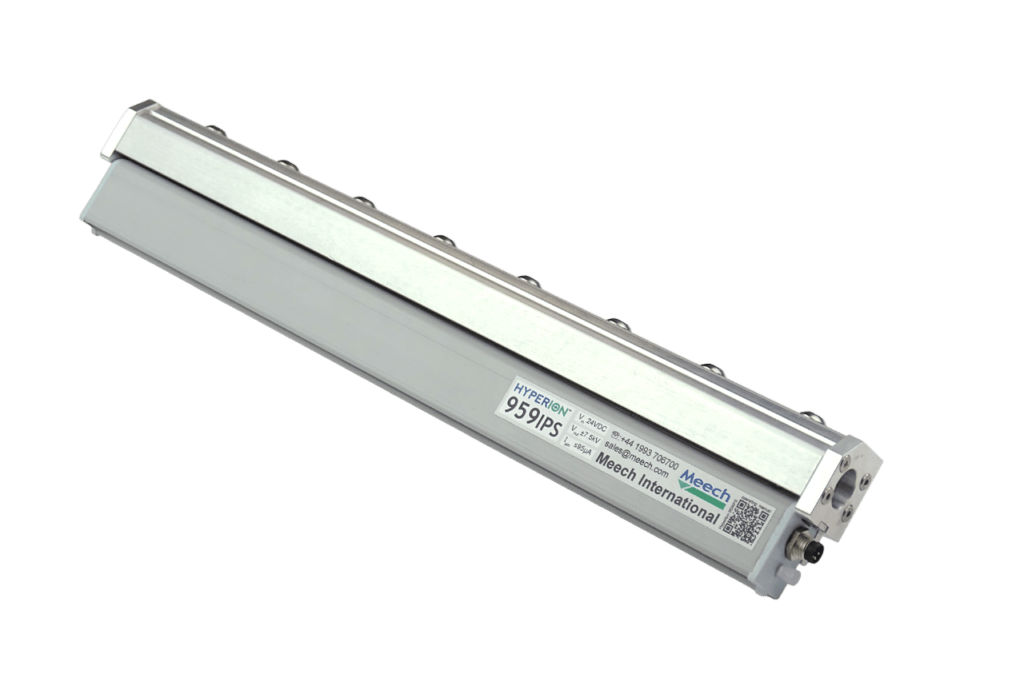
The Hyperion 959IPS ionising air curtain is an extremely versatile product that provides effective static neutralisation and dust removal.
Comprised of a Hyperion 924IPS mounted on a Meech energy saving air curtain it provides a high speed laminar sheet of ionised air.
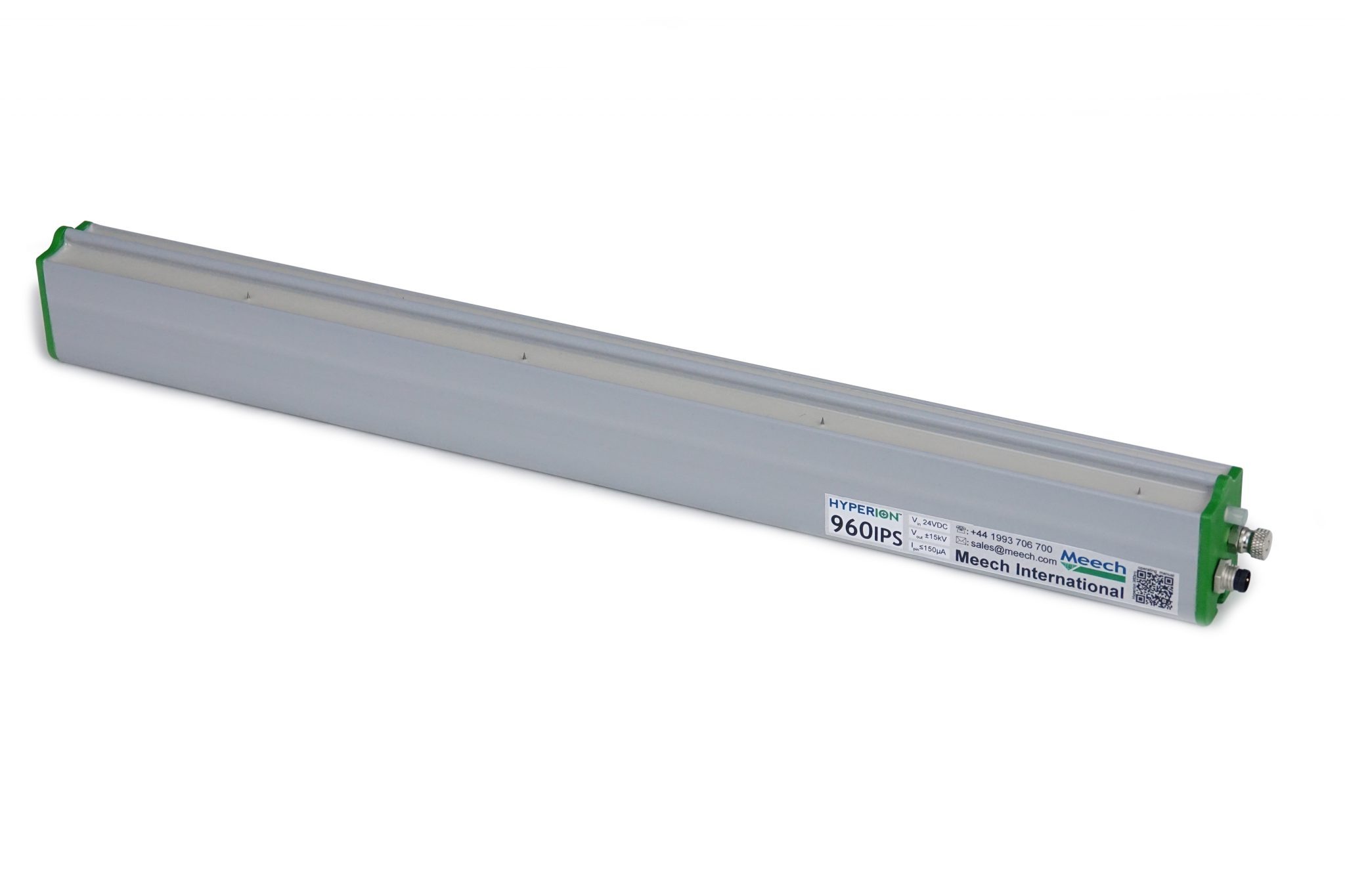
The new Hyperion 960IPS from Meech is a compact pulsed DC ionising bar with integrated high-voltage power supply (IPS). Powered by 24V DC, the 960IPS delivers powerful ionisation for mid-range applications.
The need for powerful ionisation to cope with modern fast machinery is answered by the Hyperion 960IPS. Compact dimensions of just 30mm x 45mm make it easy to install on printing and converting machinery. The 15KV pulsed DC output gives class-leading performance. The default settings will provide ideal static control on most installations with target distances from 150mm to 450 optimum performance e.g. for improving long-range performance.
Could we help improve your medical manufacturing process?
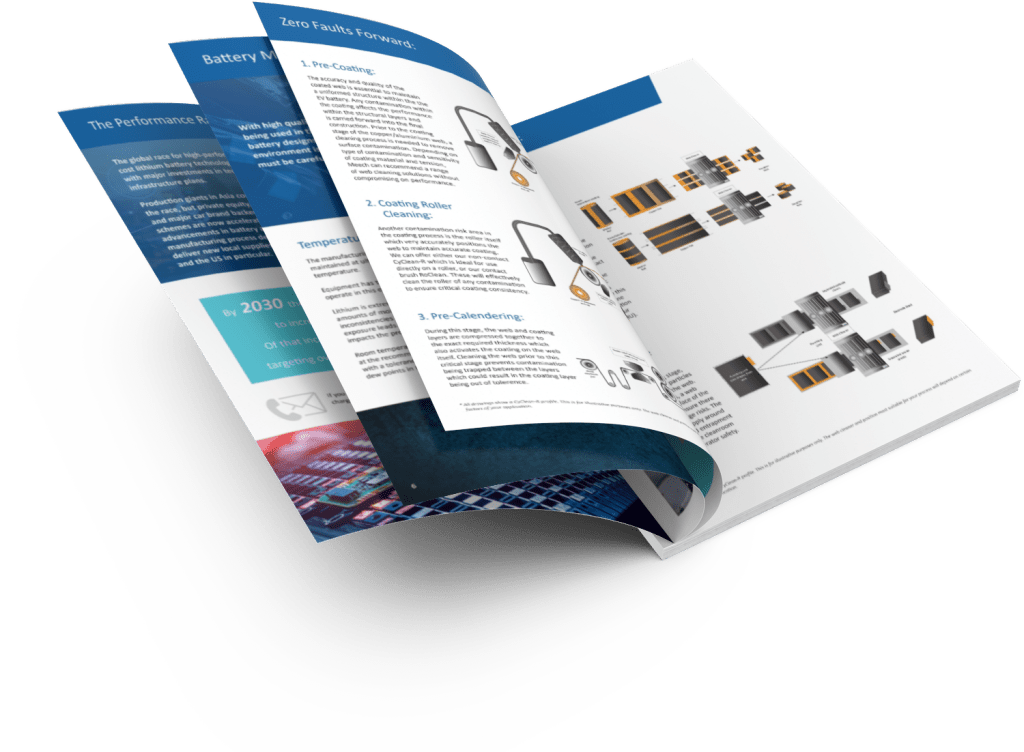