Textiles
Contamination removal in textile production
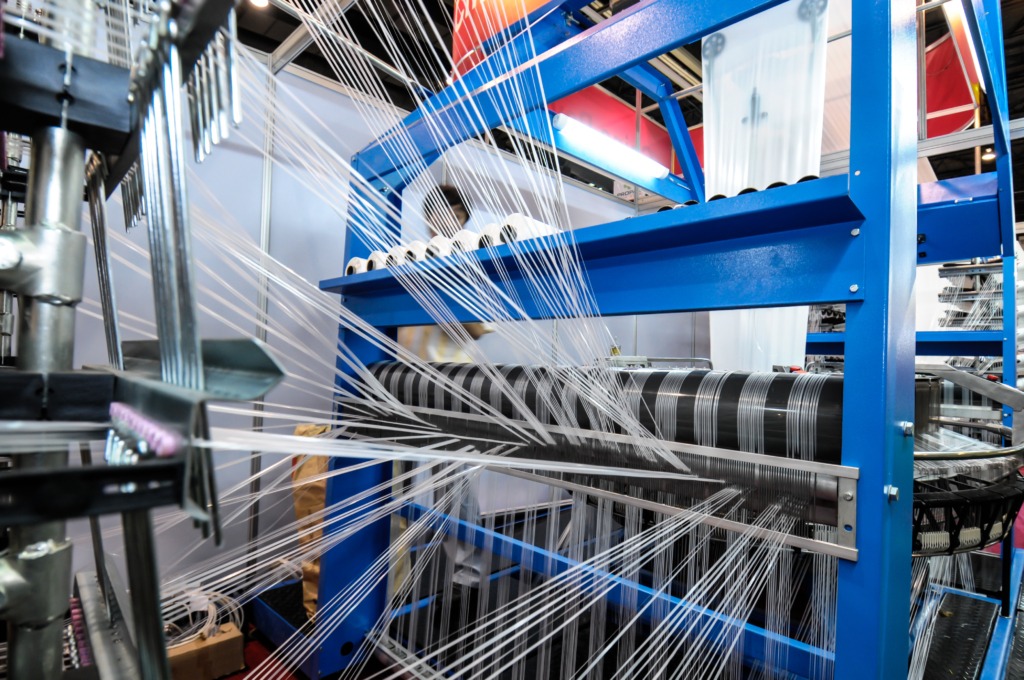
During textile production, the manipulation of fibres generates high levels of static charge which can lead to wide range of issues.
Processes such as carding, beaming, warping, stentering operations and handling machinery (e.g. laundry folders) generate particularly high levels of static. However, where synthetic fibres are concerned, ESD’s effects are even greater. As synthetic textiles continue to grow as a proportion of the overall market, the need for more robust static control solutions will grow with them.
Here at Meech Static Eliminators Ltd, we offer an advanced range of industrial static control and web cleaning solutions that are designed to neutralise the static charges on materials and avoid static related issues throughout during textiles manufacturing.
Our Zero Faults Forward Approach
We have identified a number of applications within textile manufacturing that are prone to static charge. By applying the right solutions at these points, you make sure there are no weak links to your production chain. We explore these below and demonstrate our solutions.
textile supply applications
It is critical that static electricity is controlled during the manufacturing of textiles. Below are some of the main areas affected by static charges during production, and our solutions to remove static charges and other contaminants:
Carding
In the carding process, high levels of static charges are generated and could damage or weaken the yarns. Therefore, these electrostatic charges must be neautralised, prior to the next manufacturing stage.
Our solution, is to install a pulsed DC static elimination bar such as our 960 (for mid-range) and 971IPS (for long-range) at the required distance and appropriate position to achieve static neutralisation. Any metal work between the ionising bar and the target area will prevent the ionising effect from neutralising the problem.
For instance, the recommended positioning for the Meech 976 bar is shown below. The distance between the combs and the belt should be the same, giving an approximate distance of 250mm from the comb / belt nip point.
Fibres Clinging To Combs On Textile Carding Machines
Fibre material is combed off a Doffer cylinder, either by an oscillating comb or by a rotary brush. High static charges are generated on the fibres. Static causes the fibres to cling onto the delivery transfer conveyor, resulting in a poor transfer of the product to the next process.
Our solution, is to mount a 915 ionising bar 200mm away from the comb neutralises the high static charges on the product and prevents the material from clinging onto the machine feed chutes or conveyor. The overall presentation of the finished product is also improved.
Warping & Beaming
During warping and beaming, static charges are generated on the fibres as they pass through the ceramic eyelets and the combs. The static charges generated on the individual fibres cause the fibres to either attract or repel. This fibre movement causes problems when the fibres pass through the eyelets and combs resulting in fibre breaks. It will also cause a poor presentation of the fibres onto the warping beam. These problems result in costly machine down time and product waste.
This issue can be resolved by installing our Model 915 shockless antistatic bar just prior to the problem areas. The ionised air flow eliminates the fibre movement, resulting in increased production output, quality and a reduction in waste.
Feeding from Creels
Yarn exiting the creels are heavily electrostatically charged due to friction in the ceramic eyelets. If the yarns aren’t neutralized, this could lead to yarns being repelled (a process known as ‘ballooning’ due to the shape it produces around the tip of supply bobbin) between the creel and the warper.
This issue can be resolved by installing multiple antistatic bars (short-range) in a row to cover multiple layers of yarn, or by using a long-range DC Ionising bar to neautralize static charges on on each layer of yarn coming from the creel.
Stentering Operations
During the stentering process, textiles are delivered directly onto a frame via a swing arm.
The following problems can arise:
- Static causes the product to cling or attract onto the frame sides
- Contamination of product due to dust attraction
- Operator shocks
Mounting a 971IPS on a bracket, allowing the bar to stand 200mm off the product path, behind the nip rollers on the swing arm ensures that the product is fed onto the frame free of static. The pendulum action sends waves of ions down on to the product allowing filling to be controlled with the same method.
The Model 971IPS bar also ensures the product is contaminant-free and the risk of shocks to the operator is removed.
Winding & Unwinding
During winding and unwinding, high levels of static charge is produced as a result of the contact and separation processes.
To overcome static issues, an effective static control solution such as installing a long-range static elimination bar (such as our 971IPS) or the appropriate web cleaner (such as our VacClean, CyClean or CyClean-R) should be introduced. This will neutralise any static charges caused during these processes process.
Feeding Sheet Folder Dropping Sheets Due To Static Attraction
Laundry folding machines handle items such as sheets, towels and table cloths. Such items are now normally in man-made fibres and high static charges are generated during transfer through the narrow conveyor systems and folding stations. The static charges cause the items to cling to the conveyor belts. As a result, they miss the folding unit and are then either automatically ejected from the machine or wrap around the rollers. Substituting the standard canvas conveyor belts with conductive belts does not resolve the problem.
Our solution, is to install our shockless 915 ionising bar prior to first folding station, as shown in the diagram. It is important that the top conveyor belts should be canvas rather than conductive. Not only is this a cheaper option but also performance is improved. The lower belts can be either canvas or conductive belts.
* All drawings are for illustrative purposes only. The position of the static control and web cleaning solutions most suitable for your process will depend on certain factors of your application.
Web Cleaning Solutions
Meech is a leading Web Cleaning manufacturer with a comprehensive range of four systems. Each system is based on a different cleaning principle, this uniquely allows us to provide our customers with a system best suited for their application. All Meech systems incorporate the latest shockless AC static control bars as standard which is crucial for comprehensive contamination removal. Meech has more than 200 successful web cleaning installations in a range of industries including Packaging, Printing and Converting.
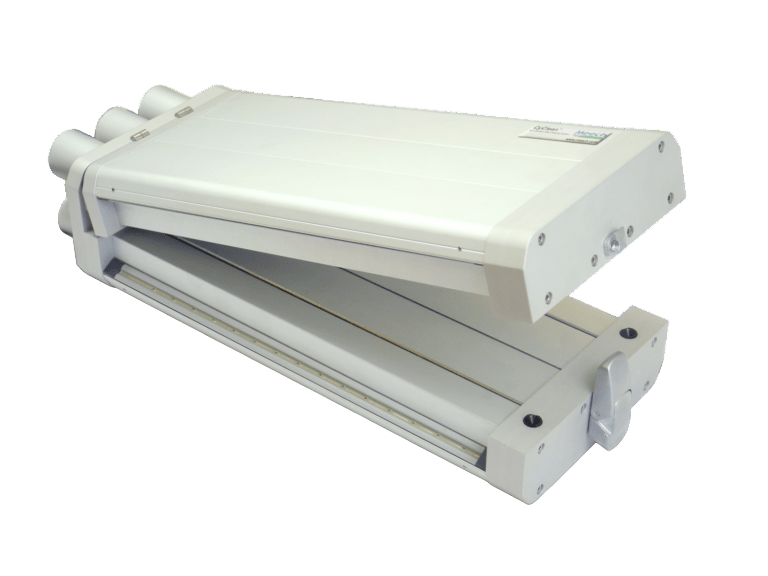
Meech CyClean™ has been designed in response to demand for a compact, high performance, non-contact web cleaner.
Through the application of advanced computational fluid dynamics, CyClean removes and extracts contamination below 1 micron.
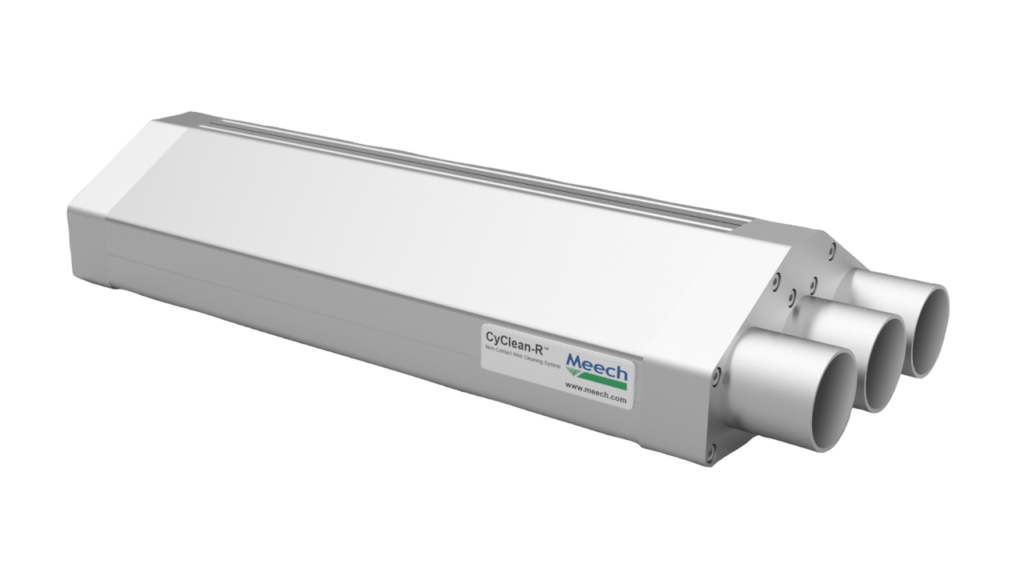
The CyClean-R provides a specialised solution for low-tension web cleaning.
The CyClean-R is designed to be positioned on the roller, where the web tension is at its highest, therefore bypassing the issues of low tension and still delivering excellent surface cleaning.
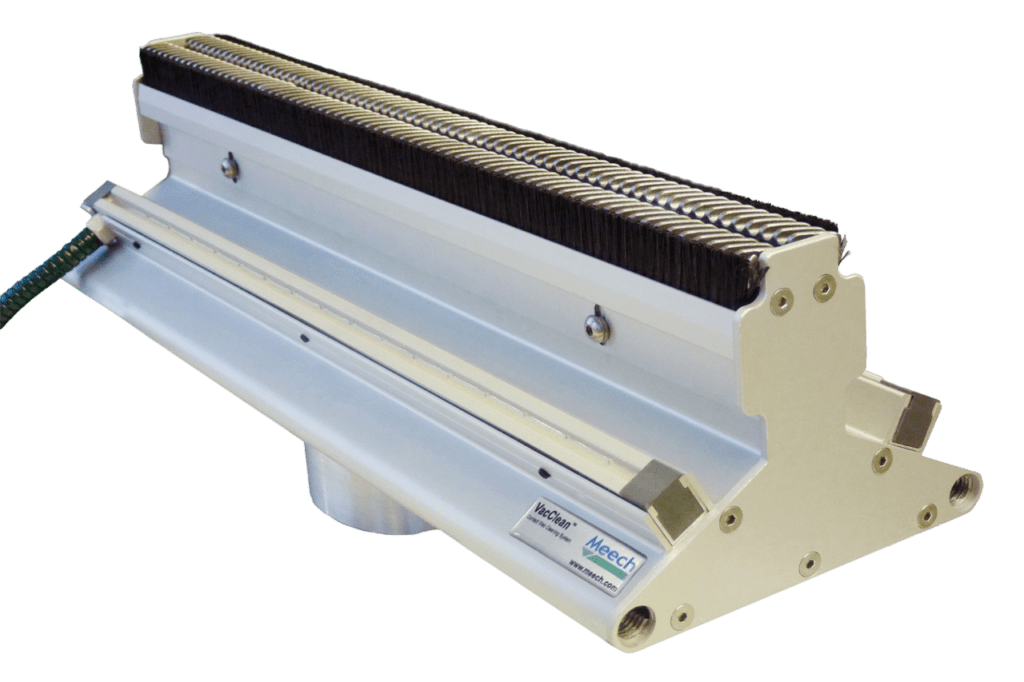
The Meech VacClean™ contact web cleaning system is an evolution of Meech’s successful Tornado system, of which there are hundreds of installations globally. VacClean systems incorporate an enhanced contact cleaning manifold with either an Air Handling Unit (AHU) or vacuum fan unit, depending on the installation environment and web width.
Static Control Solutions
Meech is a market leader in manufacturing and supplying static control products since the 1960’s; offering a wide range of electrostatic products that provide anti-static and ESD protection and measurement, static generation, electrostatic control and elimination.
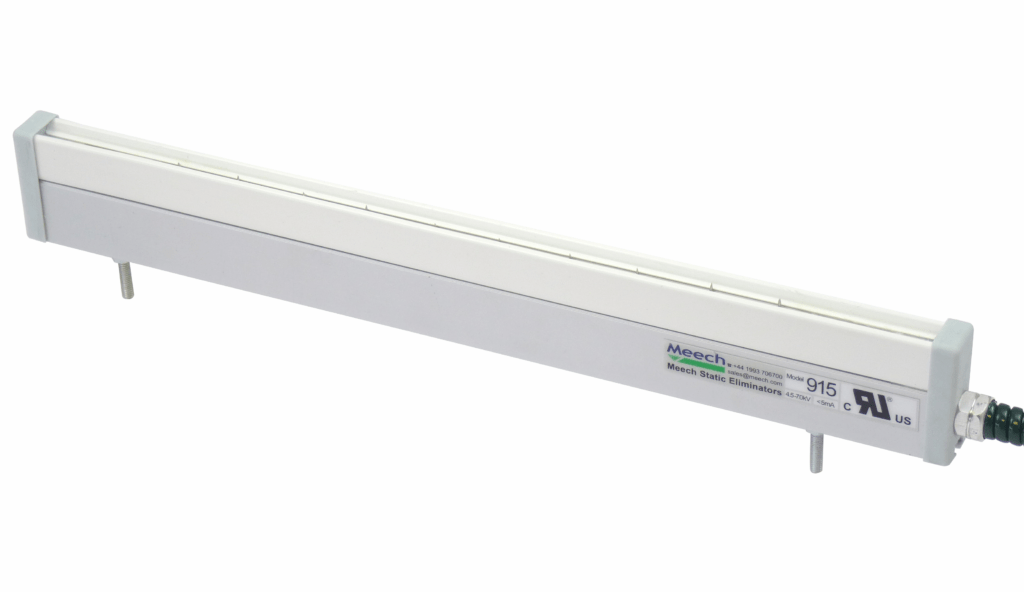
The 915 AC Anti-Static Bar offers fast and powerful static control for high speed applications.
The Meech Model 915 AC Anti-Static Bar has been designed to meet the most arduous of static elimination problems, including those encountered in high speed web applications.
The powerful performance of the Model 915 provides very fast decay times and effective ionisation up to distances of 150mm. The Model 915 bar is shockless and is easily maintained. It is powered by the Model 904.
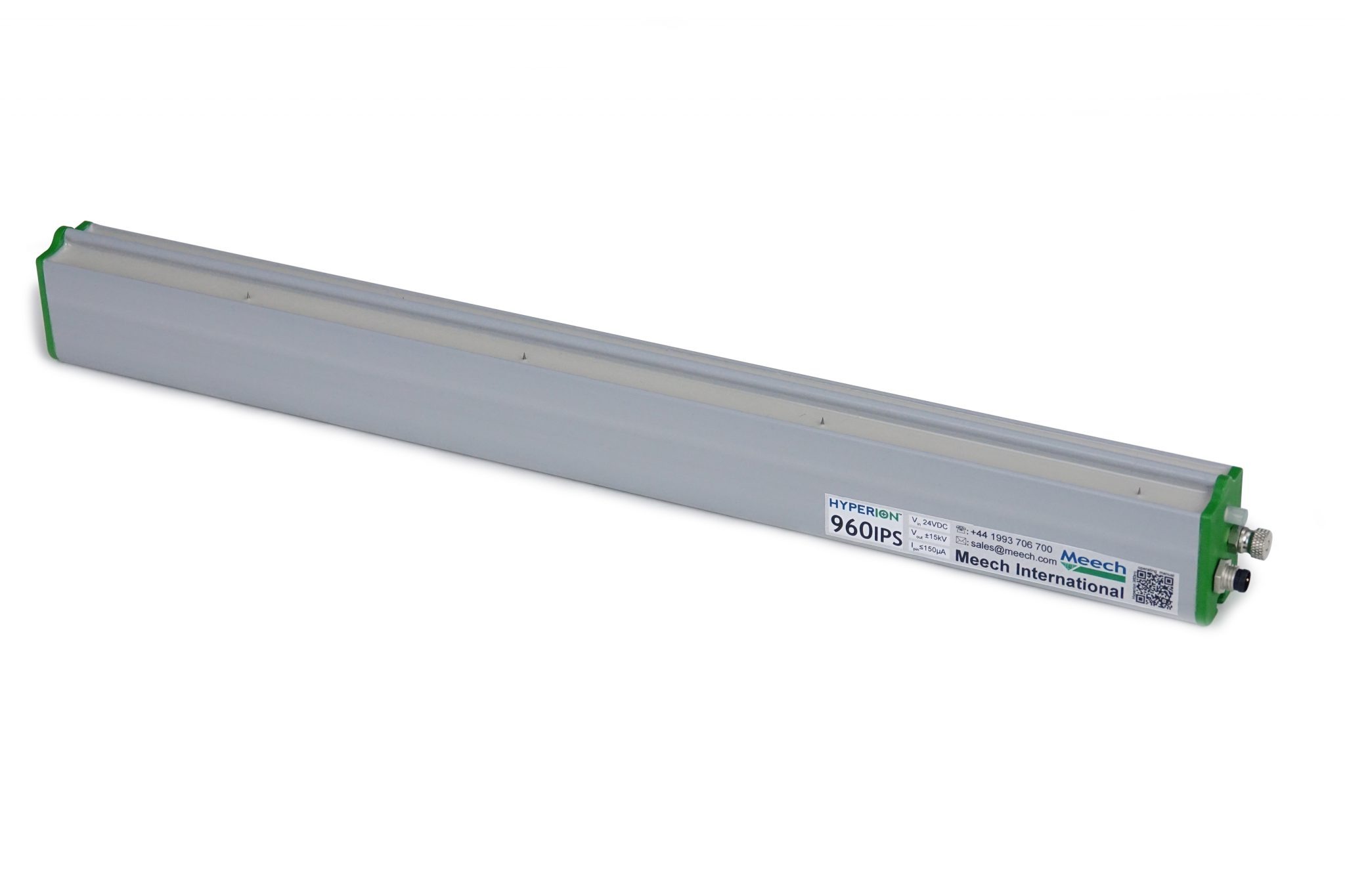
The new Hyperion 960IPS from Meech is a compact pulsed DC ionising bar with integrated high-voltage power supply (IPS). Powered by 24V DC, the 960IPS delivers powerful ionisation for mid-range applications.
The need for powerful ionisation to cope with modern fast machinery is answered by the Hyperion 960IPS. Compact dimensions of just 30mm x 45mm make it easy to install on printing and converting machinery. The 15KV pulsed DC output gives class-leading performance. The default settings will provide ideal static control on most installations with target distances from 150mm to 450 optimum performance e.g. for improving long-range performance.
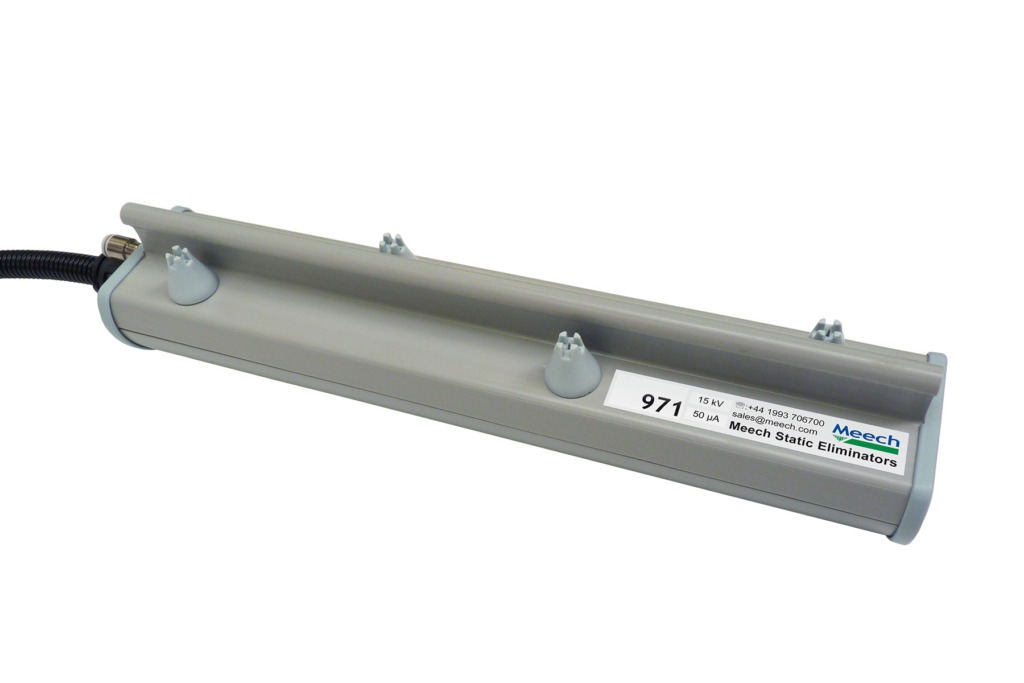
The 971 Pulsed DC bar delivers powerful, long range ionisation to control static electricity on a wide range of printing, converting and process machinery.
Using reliable Pulsed DC technology, the 971 delivers industry leading ionisation performance. Its great long range ability makes it ideal for use on applications such as rewinds and collection bins. In most installations, complete static control can be achieved without the need for air assistance. For more demanding applications, the integrated air-boost can be used to increase its capability at distance.
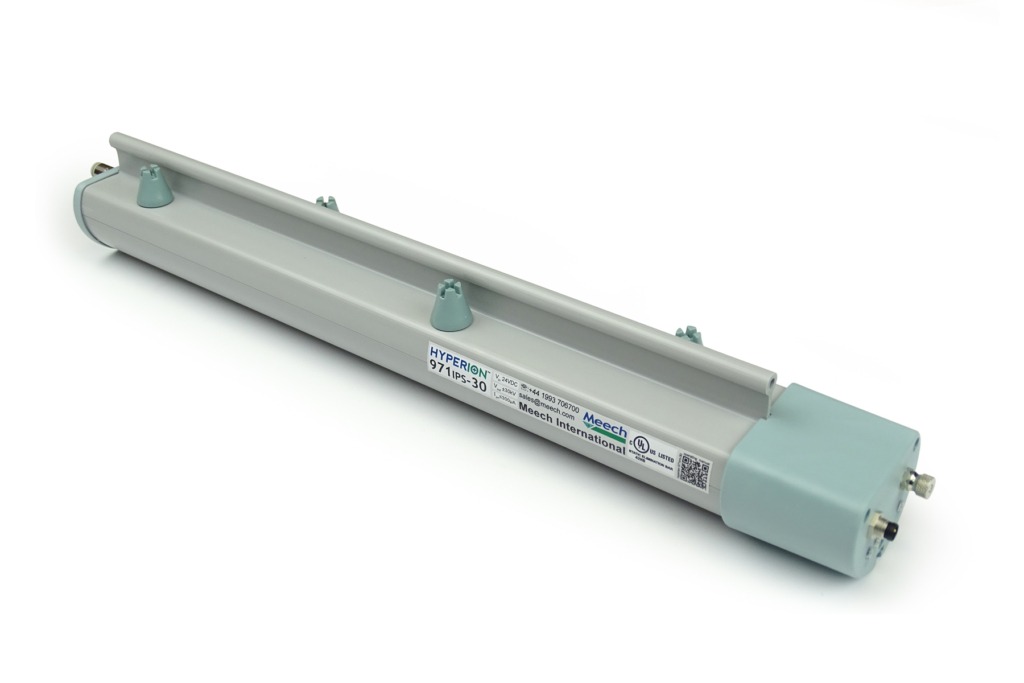
The Meech 971IPS-30 Extra Long-Range Pulsed DC Ionising Bar is the latest addition to the Meech Hyperion Range.
The 971IPS-30 is powered by an integrated +/- 30kV 24V DC power supply, making it the most powerful ionising bar in Meech’s range.
The 971IPS-30 is suitable for ultra-long range applications from 450 to 1500mm.
Equipped with Meech’s Ion Current Monitoring (ICM) technology, beam performance is maintained with local and remote alarms indicating when the beam needs cleaning. The Hyperion BarMaster remote programmer can also be used to adjust the frequency and balance of the bar, optimizing it for each application.
Could we help improve your medical manufacturing process?
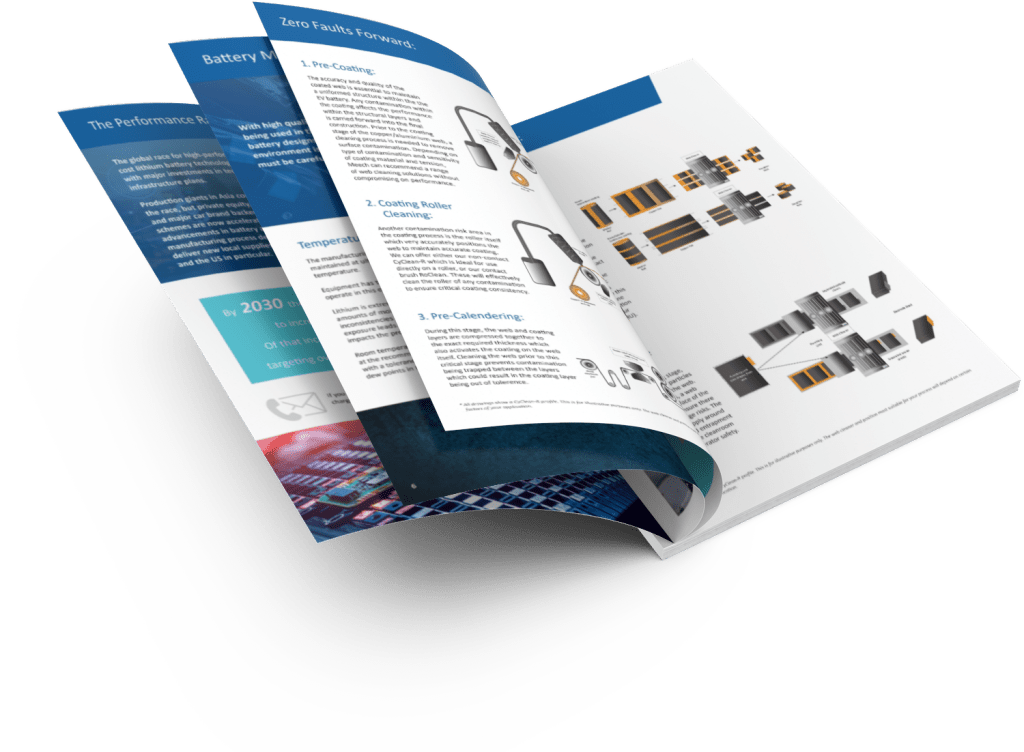